High-carbon high-chromium cold work die steel and preparation method thereof
A technology of cold working die steel, high carbon and high chromium, applied in the direction of improving process efficiency, etc., can solve the problems of low production efficiency, complex production process, small production batch, etc., to improve production efficiency, improve purity, reduce production cost effect
- Summary
- Abstract
- Description
- Claims
- Application Information
AI Technical Summary
Problems solved by technology
Method used
Image
Examples
preparation example Construction
[0024] The present invention also provides a preparation method of high-carbon and high-chromium cold-working die steel, comprising the following steps:
[0025] a. Ingredients: The return material of high-carbon and high-chromium cold-working die steel is used as the raw material, and the amount of the return material is 45% to 65%. Carbon steel, scrap steel, ferromolybdenum and ferrochrome alloy are added to make the C content 1.6 ~1.9%, the Mn content is adjusted to within 0.40%, the Cr content is adjusted to 11.30~12.0%, the Si content is adjusted to 0.50~0.8%, and the P content is adjusted to less than 0.025%; The mass percentage;
[0026] b. Smelting, refining, vacuum treatment and die-casting: smelting by return oxygen blowing method, steel is tapped after smelting, refined in LF furnace, and 0.4kg / t steel is fed with CaSi wire, 0.5kg / t steel is added with rare earth after VD vacuum treatment After metamorphic treatment, stir and blow with argon gas for 20min-30min, ad...
Embodiment 1
[0042] The preparation method of high carbon high chromium cold working die steel in the present embodiment:
[0043] a. Ingredients: use high-carbon, high-chromium cold-work die steel and returned materials of similar steel types as raw materials, and the amount of returned materials is 50%, and then add carbon steel, scrap steel, ferromolybdenum and ferrochrome alloy to make the C content match to 1.8%, Mn content to 0.38%, Cr content to 11.52%, Si content to 0.60%; P content to 0.022%.
[0044] b. Smelting, refining, vacuum treatment and die-casting: After batching, the initial molten steel is smelted in the EBT furnace by returning to the oxygen blowing method. After smelting, the steel is tapped. The tapping temperature is 1620 ° C. Refining in the LF furnace, deoxidation, desulfurization, Adjust the alloy elements, after LF refining, carry out VD vacuum treatment, after VD refining, feed CaSi wire 0.4kg / t, add rare earth 0.5kg / t for modification, stir and blow with argon...
Embodiment 2
[0049] The preparation method of high carbon high chromium cold working die steel in the present embodiment:
[0050] a. Ingredients: use high-carbon, high-chromium cold-work die steel and returned materials of similar steel types as raw materials, and the amount of returned materials is 55%, and then add carbon steel, scrap steel, ferromolybdenum and ferrochrome alloy to make the C content match to 1.87%, Mn content to 0.35%, Cr content to 11.82%, Si content to 0.70%; P content to 0.024%.
[0051] b. Smelting, refining, vacuum treatment and die-casting: After batching, the initial molten steel is smelted in the EBT furnace by returning to the oxygen blowing method. After smelting, the steel is tapped. The tapping temperature is 1650 ° C. Refining in the LF furnace, deoxidation, desulfurization, Adjust the alloying elements, after LF refining, carry out VD vacuum treatment, after VD refining, feed CaSi wire 0.4kg / t, add rare earth 0.5kg / t modification treatment, stir and blow ...
PUM
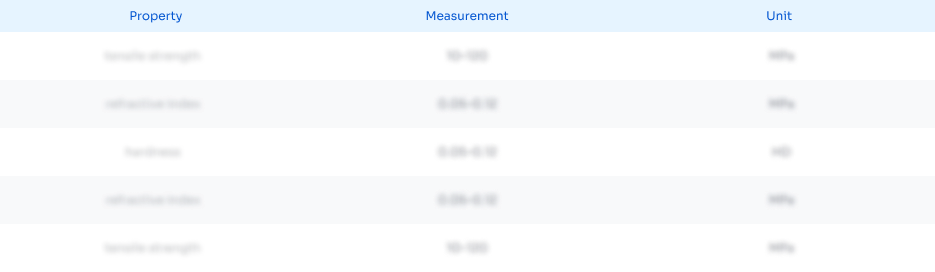
Abstract
Description
Claims
Application Information

- Generate Ideas
- Intellectual Property
- Life Sciences
- Materials
- Tech Scout
- Unparalleled Data Quality
- Higher Quality Content
- 60% Fewer Hallucinations
Browse by: Latest US Patents, China's latest patents, Technical Efficacy Thesaurus, Application Domain, Technology Topic, Popular Technical Reports.
© 2025 PatSnap. All rights reserved.Legal|Privacy policy|Modern Slavery Act Transparency Statement|Sitemap|About US| Contact US: help@patsnap.com