Preparation method of HDPE polymer film with high strength and high impact resistance
An impact-resistant, polymer film technology, applied in the field of HDPE polymer film preparation, can solve the problems of material rigidity reduction, low modulus, low strength, etc., and achieve reduced tensile strength, simple preparation method, and processing flow. The effect of sexual change
- Summary
- Abstract
- Description
- Claims
- Application Information
AI Technical Summary
Problems solved by technology
Method used
Image
Examples
Embodiment 1
[0019] A preparation method of a high-strength impact-resistant HDPE polymer film, comprising the following steps:
[0020] Step 1: Prepare materials: weigh HDPE, POE and CaCO3 for later use;
[0021] Step 2: Granulation: put POE / HDPE mass ratio of 5 / 95 into the Haake torque rheometer with temperature 170°C and rotation speed 40r / min, blend for 3 minutes, discharge and extrude and granulate;
[0022] Step 3: Add CaCO3: Add 5% CaCO3 to the pellets obtained in Step 2, increase the speed of the Haake torque rheometer by 50r / min, keep the temperature constant, and blend for 5 minutes to obtain a total of CaCO3 / POE / HDPE mixture particles;
[0023] Step 4: Place the CaCO3 / POE / HDPE blend particles prepared in step 3 in a dryer for drying;
[0024] Step 5: Add the dried CaCO3 / POE / HDPE blend particles in step 4 to a column-type flat vulcanizing machine with a temperature of 170 ℃ and a pressure of 3 MPa. After preheating, pressure keeping and cooling, press it into a waterproof roll ...
Embodiment 2
[0029] A preparation method of a high-strength impact-resistant HDPE polymer film, comprising the following steps:
[0030] Step 1: Prepare materials: weigh HDPE, POE and CaCO3 for later use;
[0031] Step 2: Granulation: Put POE / HDPE mass ratio of 10 / 90 into Huck torque rheometer with temperature of 175°C and rotation speed of 45r / min, blend for 4min, discharge, extrude and granulate;
[0032] Step 3: Add CaCO3: Add 10% CaCO3 to the pellets obtained in Step 2, increase the speed of the Haake torque rheometer to 60r / min, keep the temperature constant, and blend for 7 minutes to obtain a total of CaCO3 / POE / HDPE mixture particles;
[0033] Step 4: Place the CaCO3 / POE / HDPE blend particles prepared in step 3 in a dryer for drying;
[0034] Step 5: Add the dried CaCO3 / POE / HDPE blend particles in step 4 to a column-type flat vulcanizing machine with a temperature of 175°C and a pressure of 4 MPa. After preheating, pressure keeping and cooling, press it into a waterproof roll of a ...
Embodiment 3
[0039] A preparation method of a high-strength impact-resistant HDPE polymer film, comprising the following steps:
[0040] Step 1: Prepare materials: weigh HDPE, POE and CaCO3 for later use;
[0041] Step 2: Granulation: put POE / HDPE mass ratio of 15 / 85 into the Haake torque rheometer with temperature of 180°C and rotation speed of 50r / min, blend for 5min, discharge, extrude and granulate;
[0042] Step 3: Add CaCO3: Add 15% CaCO3 to the pellets obtained in Step 2, increase the speed of the Haake torque rheometer to 70r / min, keep the temperature constant, and blend for 8 minutes to obtain a total of CaCO3 / POE / HDPE mixture particles;
[0043] Step 4: Place the CaCO3 / POE / HDPE blend particles prepared in step 3 in a dryer for drying;
[0044] Step 5: Add the dried CaCO3 / POE / HDPE blend particles in step 4 to a column-type flat vulcanizing machine with a temperature of 180 ℃ and a pressure of 5 MPa, and press it into a waterproof roll with a certain thickness after preheating, p...
PUM
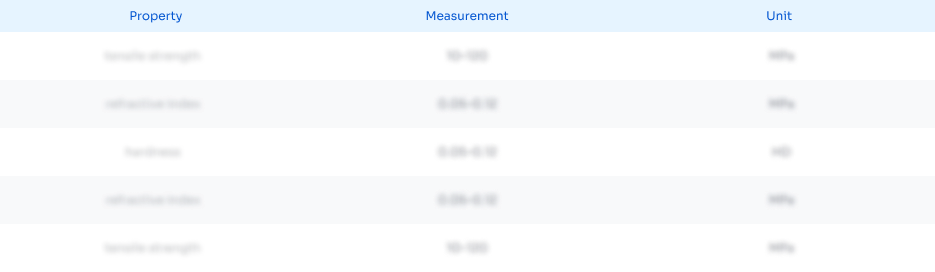
Abstract
Description
Claims
Application Information

- Generate Ideas
- Intellectual Property
- Life Sciences
- Materials
- Tech Scout
- Unparalleled Data Quality
- Higher Quality Content
- 60% Fewer Hallucinations
Browse by: Latest US Patents, China's latest patents, Technical Efficacy Thesaurus, Application Domain, Technology Topic, Popular Technical Reports.
© 2025 PatSnap. All rights reserved.Legal|Privacy policy|Modern Slavery Act Transparency Statement|Sitemap|About US| Contact US: help@patsnap.com