Method for synthesizing phenylacetic acid from carbonyl
A technology of oxo synthesis and phenylacetic acid, applied in carbon monoxide reaction to prepare carboxylic acid, carboxylate preparation, organic chemistry, etc., can solve the problem of no industrialization report. In China, there are Lanzhou Institute of Chemical Physics, Chinese Academy of Sciences, Sichuan University, Dalian University of Technology, etc. To achieve the effects of easy separation and treatment, easy recovery, and mild reaction conditions
- Summary
- Abstract
- Description
- Claims
- Application Information
AI Technical Summary
Problems solved by technology
Method used
Examples
Embodiment 1
[0035] Add a certain amount of cobalt chloride and methanol into the autoclave, replace it with CO gas for three times, slowly raise the temperature to 100~120℃ under stirring, and add CO gas to increase the internal pressure to 3.0~3.2MPa, continue After stirring, when the pressure in the kettle drops to 2.5MPa, ventilate to the original pressure again and continue until the internal pressure no longer drops. After maintaining for 8 hours, the pressure is released and the temperature is reduced to normal temperature. The suspension in the kettle is filtered, and the filter residue is used to recover cobalt. The filtrate is put into a storage tank and sealed with 0.2-0.3MPa CO to obtain a tetracarbonyl cobalt-methanol catalyst, which is metered out during the experiment.
[0036] In this embodiment, the molar ratio of catalyst to benzyl chloride is 0.02:1, and the molar ratio of benzyl chloride to NaOH is 0.25:1.
[0037] In a 1L reactor, replace with CO gas three times, add 3.04g ...
Embodiment 2
[0039] The methanol solution of cobalt tetracarbonyl in this example is the same batch of solution prepared in Example 1.
[0040] In this embodiment, the molar ratio of catalyst to benzyl chloride is 0.1:1, and the molar ratio of benzyl chloride to NaOH is 1:2.
[0041] In a 1L reactor, replace it with CO gas three times, add 17.56g of methanol solution containing cobalt tetracarbonyl, pass CO gas at a rate of 130mL / min, slowly increase the temperature to 65℃, keep the pressure at 0.1MPa, stir and start dripping Benzyl chloride and NaOH solution. The amount of benzyl chloride added was 130g, and the amount of NaOH solid was 82.2g. After the dropwise addition is completed, the reaction is continued for 4 hours, the temperature is lowered to room temperature, and air is introduced for 2 hours. The subsequent processing procedure is the same as in Example 1. 119.8 g of phenylacetic acid was obtained, the conversion rate of benzyl chloride was 99%, and the yield of phenylacetic aci...
Embodiment 3
[0043] The methanol solution of cobalt tetracarbonyl in this example is the same batch of solution prepared in Example 1.
[0044] In this embodiment, the molar ratio of catalyst to benzyl chloride is 0.05:1, and the molar ratio of benzyl chloride to NaOH is 1:2.
[0045] In a 1L reactor, replace with CO gas three times, add 8.78g of methanol solution containing cobalt tetracarbonyl, pass CO gas at a rate of 130mL / min, slowly increase the temperature to 90℃, keep the pressure at 0.5MPa, stir and start dripping Benzyl chloride and NaOH solution. The amount of benzyl chloride added was 130g, and the amount of NaOH solid was 82.2g. After the dropwise addition is completed, the reaction is continued for 8 hours, the temperature is lowered to room temperature, and air is introduced for 2 hours. The subsequent processing procedure is the same as in Example 1. 119.2 g of phenylacetic acid was obtained, the conversion rate of benzyl chloride was 99%, and the yield of phenylacetic acid w...
PUM
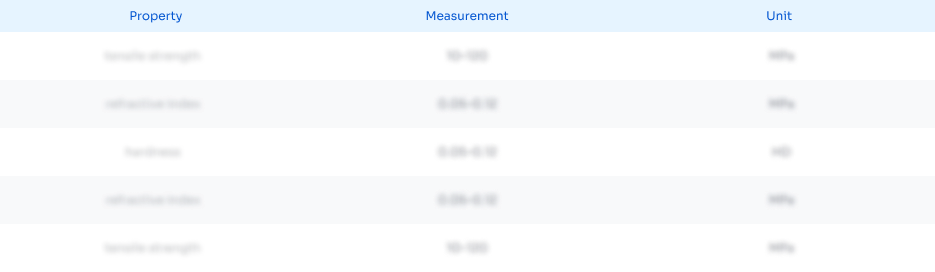
Abstract
Description
Claims
Application Information

- Generate Ideas
- Intellectual Property
- Life Sciences
- Materials
- Tech Scout
- Unparalleled Data Quality
- Higher Quality Content
- 60% Fewer Hallucinations
Browse by: Latest US Patents, China's latest patents, Technical Efficacy Thesaurus, Application Domain, Technology Topic, Popular Technical Reports.
© 2025 PatSnap. All rights reserved.Legal|Privacy policy|Modern Slavery Act Transparency Statement|Sitemap|About US| Contact US: help@patsnap.com