Wrought superalloy production process
A deformed superalloy, production process technology, applied in the field of metal materials, can solve the problems of complex powder metallurgy process, long process flow, high production cost of deformed superalloy turbine disk, etc., to improve high temperature oxidation resistance, increase expansion path, excellent The effect of machinability
- Summary
- Abstract
- Description
- Claims
- Application Information
AI Technical Summary
Problems solved by technology
Method used
Examples
Embodiment 1
[0043] The production process of deformed superalloy includes the following steps:
[0044] Step S1, pretreatment of alloy raw materials: according to the following parts by weight: 2 parts of molybdenum, 40 parts of nickel, 5 parts of aluminum, 0.5 parts of yttrium oxide, 0.2 parts of lanthanum oxide, and 0.1 part of chopped carbon fiber. Premixing;
[0045] Step S2: Prepare the alloy according to the above element ratio, and then smelt it in a vacuum induction furnace. During the smelting process, control the melting temperature: 1530°C; control the molten steel refining temperature: 1500°C; tap the steel at the end of smelting, and pour the solution into an alloy electrode;
[0046] Step S3: Perform electroslag remelting on the alloy electrode obtained in step S2, and remelt it into an electroslag ingot; electroslag remelting uses pre-melted slag, and the mass ratio of the slag system is Al 2 o 3 : TiO 2 : CaO: MgO = 20: 10: 2.8: 5;
[0047] Step S4: Carrying out vacuum...
Embodiment 2
[0053] The production process of deformed superalloy includes the following steps:
[0054] Step S1, pretreatment of alloy raw materials: according to the following parts by weight: 2.5 parts of molybdenum, 45 parts of nickel, 7.5 parts of aluminum, 0.8 parts of yttrium oxide, 0.25 parts of lanthanum oxide, and 0.15 parts of chopped carbon fiber. Premixing;
[0055] Step S2: Prepare the alloy according to the above element ratio, and then smelt it in a vacuum induction furnace. During the smelting process, control the melting temperature: 1550°C; control the molten steel refining temperature: 1540°C; tap the steel at the end of smelting, and pour the solution into an alloy electrode;
[0056] Step S3: Perform electroslag remelting on the alloy electrode obtained in step S2, and remelt it into an electroslag ingot; electroslag remelting uses pre-melted slag, and the mass ratio of the slag system is Al 2 o 3 : TiO 2 : CaO: MgO = 20: 10: 2.8: 5;
[0057] Step S4: Carry out va...
Embodiment 3
[0063] The production process of deformed superalloy includes the following steps:
[0064] Step S1, pretreatment of alloy raw materials: according to the following parts by weight: 3 parts of molybdenum, 50 parts of nickel, 8 parts of aluminum, 1 part of yttrium oxide, 0.3 parts of lanthanum oxide, and 0.2 parts of chopped carbon fiber. Premixing;
[0065] Step S2: Prepare the alloy according to the above element ratio, and then smelt it in a vacuum induction furnace. During the smelting process, control the melting temperature: 1580°C; control the molten steel refining temperature: 1570°C; tap the steel at the end of smelting, and pour the solution into an alloy electrode;
[0066] Step S3: Perform electroslag remelting on the alloy electrode obtained in step S2, and remelt it into an electroslag ingot; electroslag remelting uses pre-melted slag, and the mass ratio of the slag system is Al 2 o 3 : TiO 2 : CaO: MgO = 20: 10: 2.8: 5;
[0067] Step S4: Carry out vacuum cons...
PUM
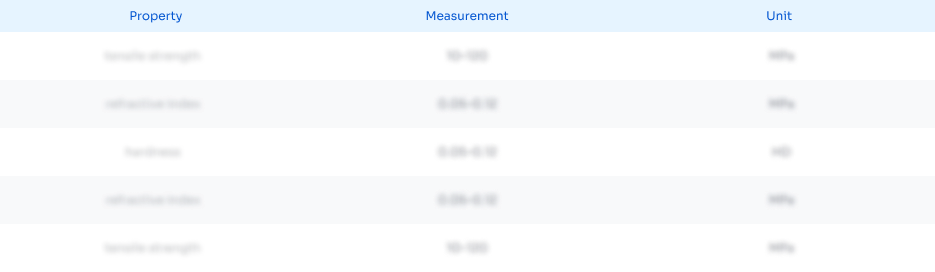
Abstract
Description
Claims
Application Information

- R&D
- Intellectual Property
- Life Sciences
- Materials
- Tech Scout
- Unparalleled Data Quality
- Higher Quality Content
- 60% Fewer Hallucinations
Browse by: Latest US Patents, China's latest patents, Technical Efficacy Thesaurus, Application Domain, Technology Topic, Popular Technical Reports.
© 2025 PatSnap. All rights reserved.Legal|Privacy policy|Modern Slavery Act Transparency Statement|Sitemap|About US| Contact US: help@patsnap.com