High-resistance corrosion-resistant electric heating alloy wire for heating tile and preparation method thereof
An electrothermal alloy and high-resistance technology, applied in the field of alloys, can solve the problem that nickel-chromium electrothermal alloy wires need to be improved, and achieve the effects of improving the structure and performance, improving the resistivity of products, and prolonging the service life.
- Summary
- Abstract
- Description
- Claims
- Application Information
AI Technical Summary
Problems solved by technology
Method used
Examples
Embodiment 1
[0021] The invention proposes a high-resistance corrosion-resistant electric heating alloy wire for heating tiles, which includes the following components by mass fraction: C: 0.08%, Mn: 0.35%, Si: 1.2%, Cr: 18.2%, Al: 0.5%, Fe: 0.4%, Zr: 0.15%, Nd: 0.04%, Ce: 0.12%, and the balance is Ni and unavoidable impurities.
[0022] The present invention also proposes a method for preparing a high-resistance corrosion-resistant electrothermal alloy wire for heating tiles, comprising the following steps:
[0023] S1. Melting: batching according to the ingredients, then melting in an argon atmosphere, removing impurities and pouring to obtain ingots;
[0024] S2. Homogenizing annealing: the ingot is placed in a heat treatment furnace at 880°C for 10 hours, and then cooled with the furnace to obtain material A;
[0025] S3, hot-rolled wire rod: subject material A to hot-rolled wire rod to obtain material B;
[0026] S4, solid solution treatment: put material B at 1020°C for 80 minutes ...
Embodiment 2
[0030] A high-resistance and corrosion-resistant electrothermal alloy wire for heating tiles proposed by the present invention comprises the following components by mass fraction: C: 0.14%, Mn: 0.55%, Si: 0.8%, Cr: 18.8%, Al: 0.6%, Fe: 0.26%, Zr: 0.18%, Nd: 0.07%, Ce: 0.08%, and the balance is Ni and unavoidable impurities.
[0031] The present invention also proposes a method for preparing a high-resistance corrosion-resistant electrothermal alloy wire for heating tiles, comprising the following steps:
[0032] S1. Melting: batching according to the ingredients, then smelting in an argon atmosphere, casting and molding after removing impurities, and obtaining ingots; wherein, the smelting process also includes deoxidation and desulfurization treatments;
[0033] S2. Homogenization annealing: place the cast ingot in a heat treatment furnace at 920°C for 9 hours, then cool with the furnace to obtain material A;
[0034] S3. Hot-rolled wire rod: hot-roll the material A as a wir...
Embodiment 3
[0039] The invention proposes a high-resistance corrosion-resistant electric heating alloy wire for heating tiles, which comprises the following components by mass fraction: C: 0.12%, Mn: 0.45%, Si: 0.95%, Cr: 19.2%, Al: 0.65%, Fe: 0.3%, Zr: 0.22%, Nd: 0.06%, Ce: 0.1%, and the balance is Ni and unavoidable impurities.
[0040] The present invention also proposes a method for preparing a high-resistance corrosion-resistant electrothermal alloy wire for heating tiles, comprising the following steps:
[0041] S1. Melting: batching according to the ingredients, then smelting in an argon atmosphere, casting and molding after removing impurities, and obtaining ingots; wherein, the smelting process also includes deoxidation and desulfurization treatments;
[0042] S2. Homogenizing annealing: the ingot is placed in a heat treatment furnace at 900°C for 9.5 hours, and then cooled with the furnace to obtain material A;
[0043] S3. Hot-rolled wire rod: hot-roll the wire rod of material...
PUM
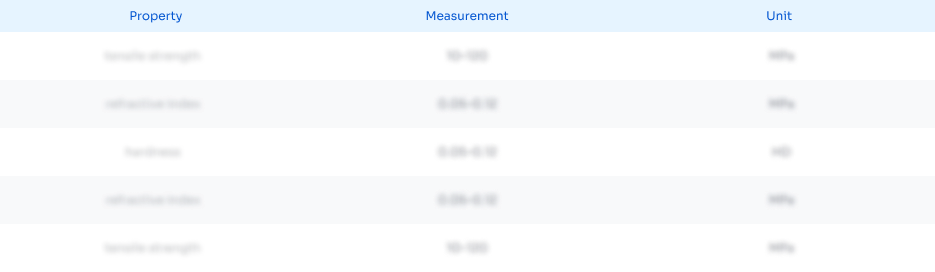
Abstract
Description
Claims
Application Information

- Generate Ideas
- Intellectual Property
- Life Sciences
- Materials
- Tech Scout
- Unparalleled Data Quality
- Higher Quality Content
- 60% Fewer Hallucinations
Browse by: Latest US Patents, China's latest patents, Technical Efficacy Thesaurus, Application Domain, Technology Topic, Popular Technical Reports.
© 2025 PatSnap. All rights reserved.Legal|Privacy policy|Modern Slavery Act Transparency Statement|Sitemap|About US| Contact US: help@patsnap.com