A kind of pyrolysis gasoline hydrotreating catalyst and its preparation method
A technology for hydrofining and pyrolysis of gasoline, which is applied in the field of oil refining and chemical industry, and can solve the problem of low catalyst hydrogenation activity
- Summary
- Abstract
- Description
- Claims
- Application Information
AI Technical Summary
Problems solved by technology
Method used
Examples
Embodiment 1
[0019] 1. Preparation of nickel-doped lanthanum ferrite
[0020] Under stirring conditions, dissolve 2.51mol lanthanum nitrate in 120mL water, add citric acid and stir to dissolve; then add 4.79mol iron nitrate, then add 190g sodium polyacrylate, then add 42g nickel nitrate aqueous solution, continue stirring for 30min, after drying Drying, roasting and grinding to obtain nickel-doped lanthanum ferrite.
[0021] 2. Preparation of silica-alumina carrier
[0022] Dissolve 5g of sodium polyacrylate in nitric acid, then add 38g of microsilica powder and 50g of pseudoboehmite powder, and stir evenly to obtain a mixture of microsilica powder-pseudoboehmite-sodium polyacrylate (abbreviated silicon-aluminum-organic mixture) , take 1 / 8 of the amount for later use, and add citric acid to 4.5g of nickel-doped lanthanum ferrite for later use. Add 300g of pseudo-boehmite powder and 25.0g of fenugreek powder into the kneader, add nitric acid, then add 40.2g of sodium polyacrylate nitric a...
Embodiment 2
[0026]The preparation of nickel-doped lanthanum ferrite is the same as in Example 1, except that 260g of sodium polyacrylate is added, and the preparation of the silica-alumina carrier is the same as in Example 1. The silica-alumina carrier contains 4.4wt% of silicon oxide, 5.7wt% % nickel-doped lanthanum ferrite, 1.2wt% magnesium, carrier mesopores accounted for 63.8% of the total pores, and macropores accounted for 25.9% of the total pores. The unit content of sodium polyacrylate in the alumina precursor is 3 times higher than the content of sodium polyacrylate in the silicon source-organic polymer mixture. The preparation method of catalyst 2 is the same as that of Example 1. The content of molybdenum oxide in catalyst 2 is 12.5%, the content of cobalt oxide is 3.8%, the content of nickel oxide is 2.7%, and the content of strontium oxide is 1.9%.
Embodiment 3
[0028] The preparation of nickel-doped lanthanum ferrite is the same as in Example 1, except that 220g of polyacrylic acid is added, and the preparation of the silica-alumina carrier is the same as in Example 1. The silica-alumina carrier contains 8.4wt% of silicon oxide, 2.6wt% The nickel-doped lanthanum ferrite, 2.1wt% magnesium, the support mesopores accounted for 54.9% of the total pores, and the macropores accounted for 33.1% of the total pores. The unit content of polyacrylic acid in the alumina precursor is 3.3 times higher than that in the silicon source-organic polymer mixture. The preparation method of catalyst 3 is the same as that of Example 1. The content of catalyst 3 is 13.7% molybdenum oxide, 4.1% cobalt oxide, 1.5% nickel oxide and 1.3% strontium oxide.
PUM
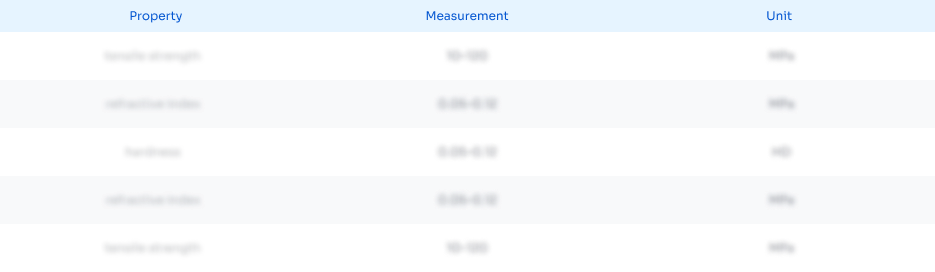
Abstract
Description
Claims
Application Information

- R&D
- Intellectual Property
- Life Sciences
- Materials
- Tech Scout
- Unparalleled Data Quality
- Higher Quality Content
- 60% Fewer Hallucinations
Browse by: Latest US Patents, China's latest patents, Technical Efficacy Thesaurus, Application Domain, Technology Topic, Popular Technical Reports.
© 2025 PatSnap. All rights reserved.Legal|Privacy policy|Modern Slavery Act Transparency Statement|Sitemap|About US| Contact US: help@patsnap.com