Method for dyeing polyester ultrafine fiber brushed cloth
A technology of polyester microfiber and dyeing method, which is applied in dyeing method, textile and papermaking, etc., can solve the problems of accelerated dyeing speed, lower dyeing and finishing efficiency of polyester brushed cloth, and high dyeing cost, so as to avoid the reduction of even dyeing rate. , good emulsification stability, improve the effect of dyeing effect
- Summary
- Abstract
- Description
- Claims
- Application Information
AI Technical Summary
Problems solved by technology
Method used
Examples
Embodiment 1
[0018] Example 1. A method for dyeing polyester microfiber brushed cloth, comprising the following steps:
[0019] ①Put the pre-shaped polyester superfine fiber brushed cloth into the dyeing machine, and add a bath of dyeing solution for fiber opening and dyeing. The bath dyeing solution includes the following raw materials: alkaline degreasing agent TF-103 (Transfar Zhilian Co., Ltd.) 1g / L, leveling agent JX-F (Penglai Jiaxin Dyestuff Chemical Co., Ltd.) 3g / L, sodium hydroxide 5g / L and high alkali-resistant disperse dyes; among them, the high alkali-resistant disperse dyes are any one or more combinations of HA-4RS yellow, HA-R red and HA-2BN dark blue (dye) of Penglai Jiaxin Dyestuff Chemical Co., Ltd. , the amount of high alkali-resistant disperse dye is 1% owf; the bath ratio of one-bath dyeing agent for fiber-opening dyeing is 1:15; A cloth is obtained;
[0020] ②Heat the dye solution from room temperature to 60 °C at a rate of 2 °C / min, then heat the dye solution from...
Embodiment 2
[0026] Example 2. A method for dyeing polyester microfiber brushed cloth, comprising the following steps:
[0027] ①Put the pre-shaped polyester superfine fiber brushed cloth into the dyeing machine, and add a bath of dyeing solution for fiber opening and dyeing. The bath dyeing solution includes the following raw materials: alkaline degreasing agent TF-103 (Transfar Zhilian Co., Ltd.) 2g / L, leveling agent JX-F (Penglai Jiaxin Dyestuff Chemical Co., Ltd.) 2g / L, sodium hydroxide 8g / L and high alkali-resistant disperse dyes; wherein the high alkali-resistant disperse dyes are any one or more combinations of HA-4RS yellow, HA-R red and HA-2BN dark blue, and the dosage of high alkali-resistant disperse dyes is 4 %owf; the bath ratio of the first bath dyeing agent for fiber opening dyeing is 1:10; get A cloth;
[0028] ②Heat the dye solution from room temperature to 60 °C at a rate of 3 °C / min, then heat the dye solution from 60 °C to 110 °C at a rate of 0.5 °C / min, and then soa...
Embodiment 3
[0032] Example 3. A kind of dyeing method of pure polyester jeanette (75D * 150D / 288F), comprises the following steps:
[0033] ①Put the pre-shaped polyester superfine fiber brushed cloth into the dyeing machine, and add a bath of dyeing solution for fiber opening and dyeing. The bath dyeing solution includes the following raw materials: alkaline degreasing agent TF-103 (Transfar Zhilian Co., Ltd.) 1.5g / L, leveling agent JX-F (Penglai Jiaxin Dyestuff Chemical Co., Ltd.) 2.5g / L, hydroxide Sodium 6g / L and high alkali-resistant disperse dyes; the proportion of high alkali-resistant disperse dyes is HA-4RS yellow 0.2% owf, HA-R red 0.5% owf and HA-2BN dark blue 1.5% owf; fiber opening dyeing one bath The bath ratio of the dye is 1:13; A cloth is obtained;
[0034] ②Heat the dye solution from room temperature to 60 °C at a rate of 2.5 °C / min, then heat the dye solution from 60 °C to 110 °C at a rate of 0.6 °C / min, and then soak for 15 minutes; obtain B cloth;
[0035] ③Heat the ...
PUM
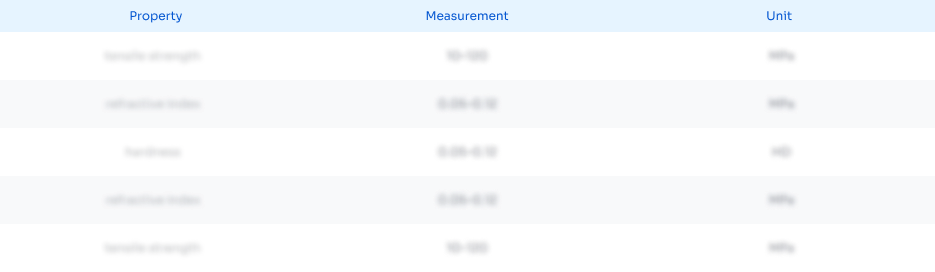
Abstract
Description
Claims
Application Information

- Generate Ideas
- Intellectual Property
- Life Sciences
- Materials
- Tech Scout
- Unparalleled Data Quality
- Higher Quality Content
- 60% Fewer Hallucinations
Browse by: Latest US Patents, China's latest patents, Technical Efficacy Thesaurus, Application Domain, Technology Topic, Popular Technical Reports.
© 2025 PatSnap. All rights reserved.Legal|Privacy policy|Modern Slavery Act Transparency Statement|Sitemap|About US| Contact US: help@patsnap.com