Method for preparing dipropylene glycol methyl ether by means of continuous reaction
A dipropylene glycol methyl ether, chemical reaction technology, applied in the preparation of ether from alkylene oxide, ether preparation, organic chemistry, etc., can solve the problems of inventory backlog, complex composition, increased by-products, etc., and achieve high production efficiency and less by-products , The effect of simple process
- Summary
- Abstract
- Description
- Claims
- Application Information
AI Technical Summary
Problems solved by technology
Method used
Examples
Embodiment 1
[0021] The technical specification of the pipeline reactor: ø10×1×200000 stainless steel tube, the reactor volume is 10L. The reaction adopts a constant temperature method: the pipeline reactor is placed in a constant temperature heating box with automatic temperature control and a built-in hot air circulation system.
[0022] The catalyst sodium methoxide was prepared in 2-methoxy-1-propanol according to 0.04% of the total mass of the raw materials, and the reaction system was firstly input and filled with the reaction system after preheating at a flow rate of 4.24L / h with a metering pump, and then the epoxy resin was started. Propane metering pump, the control flow rate is 0.76L / h, the molar ratio of 2-methoxy-1-propanol and propylene oxide is 4:1, and the reaction residence time is 2h. 2-Methoxy-1-propanol and propylene oxide are preheated to 120 ℃ through a static mixer, and then the reaction raw materials are preheated to 120 °C through a preheater, and are continuously i...
Embodiment 2
[0024] The technical specification of the pipeline reactor: ø10×1×200000 stainless steel tube, the reactor volume is 10L. The reaction adopts a combination of constant temperature and heat insulation: the first 40m pipeline reactor is placed in a constant temperature heating box with automatic temperature control and a built-in hot air circulation system, and the remaining 160m is well insulated.
[0025] The catalyst sodium methoxide was placed in 2-methoxy-1-propanol according to 0.06% of the total mass of the raw materials, and the reaction system was preheated with a metering pump at a flow rate of 3.50L / h and then filled with the reaction system. Then, the epoxy resin was started. Propane metering pump, the control flow rate is 0.5L / h, the molar ratio of 2-methoxy-1-propanol and propylene oxide is 5:1, and the reaction residence time is 2.5h (wherein the constant temperature reaction residence time is 0.5h, adiabatic The reaction residence time is 2h). 2-Methoxy-1-propan...
Embodiment 3
[0027] The technical specification of the pipeline reactor: ø10×1×200000 stainless steel tube, the reactor volume is 10L. The reaction adopts a constant temperature method: the pipeline reactor is placed in a constant temperature heating box with automatic temperature control and a built-in hot air circulation system.
[0028] The catalyst potassium methoxide was placed in 2-methoxy-1-propanol according to 0.08% of the total mass of the raw materials, and the metering pump was preheated at a flow rate of 2.98L / h, and the reaction system was first input and filled, and then the epoxy resin was started. Propane metering pump, the control flow rate is 0.35L / h, the molar ratio of 2-methoxy-1-propanol and propylene oxide is 6:1, and the reaction residence time is 3h. 2-Methoxy-1-propanol and propylene oxide are preheated to 110 ℃ through a static mixer, and then the reaction raw materials are preheated to 110 ℃ through a preheater, and are continuously input into the pipeline react...
PUM
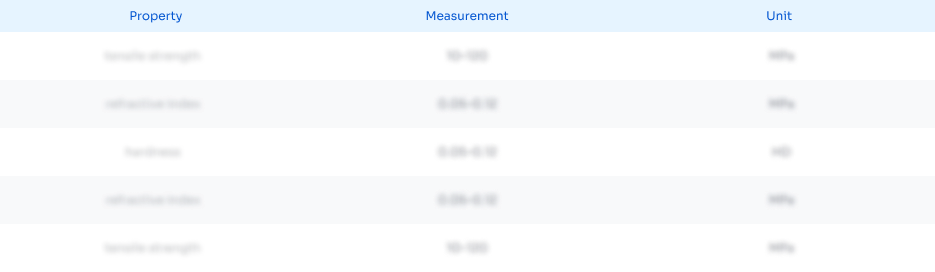
Abstract
Description
Claims
Application Information

- R&D
- Intellectual Property
- Life Sciences
- Materials
- Tech Scout
- Unparalleled Data Quality
- Higher Quality Content
- 60% Fewer Hallucinations
Browse by: Latest US Patents, China's latest patents, Technical Efficacy Thesaurus, Application Domain, Technology Topic, Popular Technical Reports.
© 2025 PatSnap. All rights reserved.Legal|Privacy policy|Modern Slavery Act Transparency Statement|Sitemap|About US| Contact US: help@patsnap.com