Production technology for coated glass fiber gridding cloth
A technology of glass fiber and production technology, which is applied in the field of mesh cloth production technology, can solve the problems of uneven surface of mesh cloth, unsatisfactory strength, difficult quality control, etc., and achieve shrinkage deformation, light weight, and good alkali resistance Effect
- Summary
- Abstract
- Description
- Claims
- Application Information
AI Technical Summary
Problems solved by technology
Method used
Examples
Embodiment 1
[0021] A production process for coating glass fiber mesh cloth, comprising the following steps:
[0022] 1) Weigh the raw materials according to the formula and set aside;
[0023] 2) Stir the raw materials with a mixer to mix the raw and auxiliary materials evenly; then continuously transport the mixed raw materials to the screw extruder through a vacuum suction device; the raw materials become viscous after being melted and compressed by the screw extruder The melt is then transported to the melt filter through the melt pipeline for filtration;
[0024] 3) Send the melt obtained in step 2) into the metering pump, and send it into the spinning box under the control of the metering pump, and perform the spinning operation to obtain filaments. The aperture of the spinneret is 0.6mm;
[0025] 4) Airflow traction is carried out on the tow to form a fiber web embryo body. The airflow pressure of the traction airflow is 3000pa, and the airflow velocity is 5.2m / s. The fiber web emb...
Embodiment 2
[0034] A production process for coating glass fiber mesh cloth, comprising the following steps:
[0035] 1) Weigh the raw materials according to the formula and set aside;
[0036] 2) Stir the raw materials with a mixer to mix the raw and auxiliary materials evenly; then continuously transport the mixed raw materials to the screw extruder through a vacuum suction device; the raw materials become viscous after being melted and compressed by the screw extruder The melt is then transported to the melt filter through the melt pipeline for filtration;
[0037] 3) Send the melt obtained in step 2) into the metering pump, and send it into the spinning box under the control of the metering pump, and perform the spinning operation to obtain filaments. The aperture of the spinneret is 0.6mm;
[0038] 4) Airflow traction is carried out on the tow to form a fiber web embryo body. The airflow pressure of the traction airflow is 3000pa, and the airflow velocity is 5.2m / s. The fiber web emb...
Embodiment 3
[0047] A production process for coating glass fiber mesh cloth, comprising the following steps:
[0048] 1) Weigh the raw materials according to the formula and set aside;
[0049] 2) Stir the raw materials with a mixer to mix the raw and auxiliary materials evenly; then continuously transport the mixed raw materials to the screw extruder through a vacuum suction device; the raw materials become viscous after being melted and compressed by the screw extruder The melt is then transported to the melt filter through the melt pipeline for filtration;
[0050] 3) Send the melt obtained in step 2) into the metering pump, and send it into the spinning box under the control of the metering pump, and perform the spinning operation to obtain filaments. The aperture of the spinneret is 0.6mm;
[0051] 4) Airflow traction is carried out on the tow to form a fiber web embryo body. The airflow pressure of the traction airflow is 3000pa, and the airflow velocity is 5.2m / s. The fiber web emb...
PUM
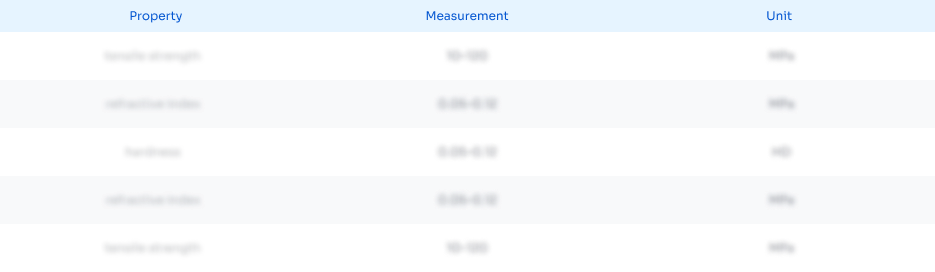
Abstract
Description
Claims
Application Information

- R&D Engineer
- R&D Manager
- IP Professional
- Industry Leading Data Capabilities
- Powerful AI technology
- Patent DNA Extraction
Browse by: Latest US Patents, China's latest patents, Technical Efficacy Thesaurus, Application Domain, Technology Topic, Popular Technical Reports.
© 2024 PatSnap. All rights reserved.Legal|Privacy policy|Modern Slavery Act Transparency Statement|Sitemap|About US| Contact US: help@patsnap.com