Bisphenol A formaldehyde phenolic resin and synthetic method thereof
A technology of phenolic resin and synthesis method, applied in the direction of aldehyde/ketone condensation polymer adhesive, adhesive type, adhesive, etc., can solve the problems of difficult separation and purification, high content of free formaldehyde, small molecular weight, etc.
- Summary
- Abstract
- Description
- Claims
- Application Information
AI Technical Summary
Problems solved by technology
Method used
Image
Examples
Embodiment 1
[0042] Step 1. Add 11.4g of bisphenol A and 25mL of n-butanol into a 50ml three-neck round bottom flask equipped with mechanical stirring and reflux condensing device, stir and heat up to 60°C until the bisphenol A is completely dissolved and the reaction system is clear and transparent .
[0043] Step 2. Reflux to room temperature with water cooling, then add 4.5 g of 37% formaldehyde aqueous solution and 0.13 g of p-toluenesulfonic acid at one time to form a mixed solution; stir the mixed solution while heating to 95° C. at a stirring rate of 450 r / min; Reacted at this temperature for 7h to generate a purple liquid.
[0044] Step 3, distill off n-butanol and a small amount of water under normal pressure, then remove the remaining water under reduced pressure until there is no water drop back, and the product becomes a purple-red viscous liquid.
[0045] Step 4, wash with boiling water 3 times to remove unreacted bisphenol A, finally dehydrate under reduced pressure, dry in ...
Embodiment 2
[0047] Step 1. Add 10g of bisphenol A and 20mL of n-butanol into a 50ml three-neck round bottom flask equipped with mechanical stirring and reflux condensing device, stir and raise the temperature to 70°C until the bisphenol A is completely dissolved and the reaction system is clear and transparent.
[0048] Step 2. Cool and reflux with water to room temperature, then add 5 g of 37% formaldehyde aqueous solution and 0.4 g of p-toluenesulfonic acid at one time to form a mixed solution; stir the mixed solution while heating to 80°C with a stirring rate of 450r / min; Reaction at this temperature for 5h produces a purple liquid.
[0049] Step 3, distill off n-butanol and a small amount of water under normal pressure, then remove the remaining water under reduced pressure until there is no water drop back, and the product becomes a purple-red viscous liquid.
[0050] Step 4, wash with boiling water 5 times to remove unreacted bisphenol A, finally dehydrate under reduced pressure, dr...
Embodiment 3
[0052] Step 1. Add 30g of bisphenol A and 30mL of n-butanol into a 50ml three-necked round bottom flask equipped with a mechanical stirring and reflux condensing device, stir and heat up to 80°C until the bisphenol A is completely dissolved and the reaction system is clear and transparent.
[0053] Step 2. Reflux with water to room temperature, then add 6.7g of 37% formaldehyde solution and 0.3g of p-toluenesulfonic acid at one time to form a mixed solution; stir the mixed solution while heating to 85°C with a stirring rate of 450r / min; Reaction at this temperature for 8h, resulting in a purple liquid.
[0054] Step 3, distill off n-butanol and a small amount of water under normal pressure, then remove the remaining water under reduced pressure until there is no water drop back, and the product becomes a purple-red viscous liquid.
[0055] Step 4, wash with boiling water 4 times to remove unreacted bisphenol A, finally dehydrate under reduced pressure, dry in a vacuum oven at ...
PUM
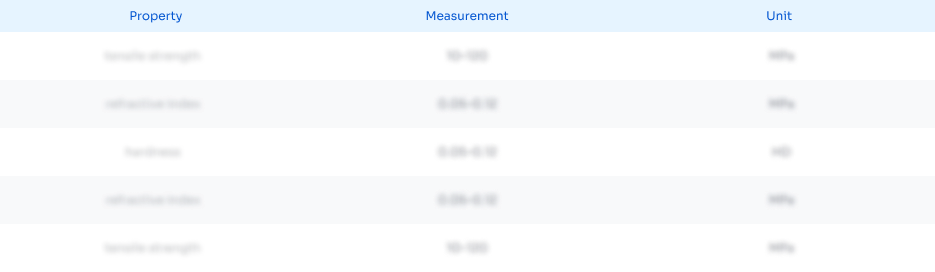
Abstract
Description
Claims
Application Information

- R&D Engineer
- R&D Manager
- IP Professional
- Industry Leading Data Capabilities
- Powerful AI technology
- Patent DNA Extraction
Browse by: Latest US Patents, China's latest patents, Technical Efficacy Thesaurus, Application Domain, Technology Topic, Popular Technical Reports.
© 2024 PatSnap. All rights reserved.Legal|Privacy policy|Modern Slavery Act Transparency Statement|Sitemap|About US| Contact US: help@patsnap.com