Diffraction grating etcher
A diffraction grating and etching machine technology, which is applied in the field of photolithography to ensure the quality and integrity and the sealing effect.
- Summary
- Abstract
- Description
- Claims
- Application Information
AI Technical Summary
Problems solved by technology
Method used
Image
Examples
Embodiment Construction
[0026] In order to make the technical means, creative features, goals and effects achieved by the present invention easy to understand, the present invention will be further described below in conjunction with specific embodiments.
[0027] Such as Figure 1-4As shown, a diffraction grating etching machine according to the present invention includes a first fixed casing 1, a transmission mechanism 2, a second fixed casing 3, an etching mechanism 4, a feeding mechanism 5, a sealing mechanism 6, and an adjustment mechanism 7 and a photolithography mechanism 8, the first fixed housing 1 is provided with the photolithography mechanism 8; the first fixed housing 1 is provided with the feeding mechanism 5, and the feeding mechanism 5 includes the second A hydraulic cylinder 51 and a second bearing plate 52, the second hydraulic cylinder 51 is located at the bottom of the slide chamber of the first fixed housing 1, and the top of the second hydraulic cylinder 51 is connected to the s...
PUM
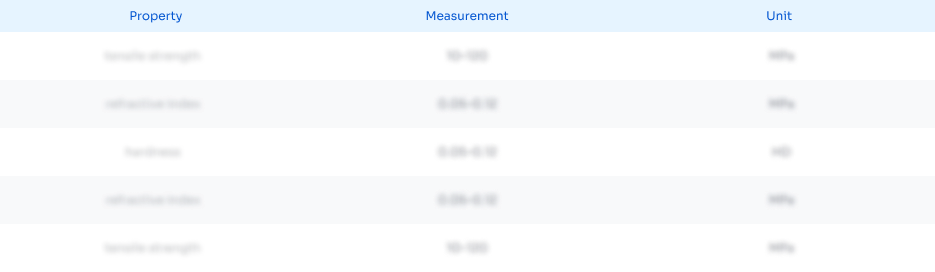
Abstract
Description
Claims
Application Information

- R&D
- Intellectual Property
- Life Sciences
- Materials
- Tech Scout
- Unparalleled Data Quality
- Higher Quality Content
- 60% Fewer Hallucinations
Browse by: Latest US Patents, China's latest patents, Technical Efficacy Thesaurus, Application Domain, Technology Topic, Popular Technical Reports.
© 2025 PatSnap. All rights reserved.Legal|Privacy policy|Modern Slavery Act Transparency Statement|Sitemap|About US| Contact US: help@patsnap.com