Waterborne self-emulsifying epoxy modified alkyd resin and anticorrosive coating thereof
A self-emulsifying epoxy and alkyd resin technology, used in anti-corrosion coatings, polyester coatings, coatings, etc., can solve the problems of narrow application range, complex preparation process and poor storage stability of water-based alkyd resins, and achieve convenient construction. , Good storage stability and strong adhesion
- Summary
- Abstract
- Description
- Claims
- Application Information
AI Technical Summary
Problems solved by technology
Method used
Image
Examples
Embodiment 1
[0028] (1) Preparation of water-based self-emulsifying epoxy-modified alkyd resin
[0029] In reactor, add 300g linolenic acid, 30g pentaerythritol, 100g ethylene glycol, 20g neopentyl glycol, molecular weight are 600 polyethylene glycol 100g, 20g benzoic acid, 80g maleic anhydride, 30g trimellitic anhydride and 150g xylene, heat up Carry out esterification reaction at 180-220°C for 6-10 hours, continuously divide water during the reaction, measure the acid value of the reactant, after the acid value reaches 80-150mg KOH / g, add 80g of epoxy resin E51 to the reaction In the material, continue to react for 4-6 hours, measure the acid value continuously during the reaction process, until the acid value reaches < 30mg KOH / g, after the solvent is removed under reduced pressure, the temperature is lowered to 70-80°C, and then 700g of deionized water is added to prepare a solid Self-emulsifying epoxy-modified alkyd resin with a content of about 50% has a white emulsion appearance, an...
Embodiment 2
[0032] (1) Preparation of water-based self-emulsifying epoxy-modified alkyd resin
[0033] Add 300g linolenic acid, 30g trimethylolpropane, 100g ethylene glycol, 20g neopentyl glycol, 100g polyethylene glycol monomethyl ether with a molecular weight of 600, 20g benzoic acid, 80g maleic anhydride, 30g Trimellitic anhydride and 150g xylene, heated up to 180-220°C, carried out esterification reaction for 6-10 hours, water was continuously separated during the reaction, and the acid value of the reactant was measured. After the acid value reached 80-150mg KOH / g, 100g Epoxy resin E51 was added to the reactant, and the reaction was continued for 4-6 hours. During the reaction, the acid value was continuously measured until the acid value reached < 30mg KOH / g. 750g of deionized water to prepare a self-emulsifying epoxy-modified alkyd resin with a solid content of about 45%. The appearance is a white emulsion. The prepared resin does not precipitate or delaminate during heat storage (...
Embodiment 3
[0036] (1) Preparation of water-based self-emulsifying epoxy-modified alkyd resin
[0037] Add 350g oleic acid, 30g trimethylolpropane, 80g ethylene glycol, 20g neopentyl glycol, molecular weight 800 polyethylene glycol monomethyl ether 100g, 20g benzoic acid, 70g maleic anhydride, 25g trimellitic anhydride in the reaction kettle And 150g xylene, warming up to 180-220°C, carry out esterification reaction for 6-10 hours, continuously divide water during the reaction, measure the acid value of the reactant, after the acid value reaches 80-150mg KOH / g, 70g ring Add oxygen resin E51 to the reactant and continue to react for 4-6 hours. During the reaction, measure the acid value continuously until the acid value reaches < 30mg KOH / g. After removing the solvent under reduced pressure, cool down to 70-80°C and then add 750g Deionized water is used to prepare a self-emulsifying epoxy-modified alkyd resin with a solid content of about 45%. The appearance is a white emulsion. The prepar...
PUM
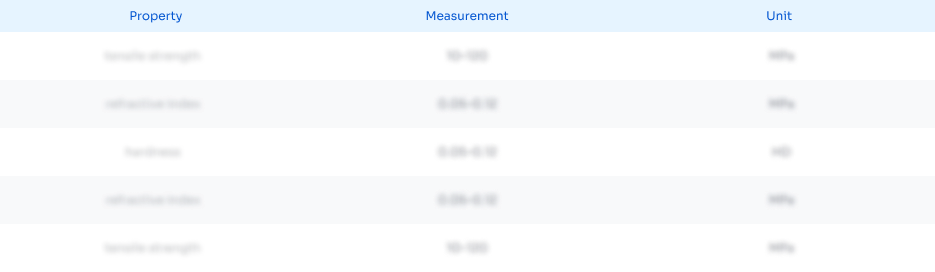
Abstract
Description
Claims
Application Information

- R&D
- Intellectual Property
- Life Sciences
- Materials
- Tech Scout
- Unparalleled Data Quality
- Higher Quality Content
- 60% Fewer Hallucinations
Browse by: Latest US Patents, China's latest patents, Technical Efficacy Thesaurus, Application Domain, Technology Topic, Popular Technical Reports.
© 2025 PatSnap. All rights reserved.Legal|Privacy policy|Modern Slavery Act Transparency Statement|Sitemap|About US| Contact US: help@patsnap.com