Polymer conductive composite material with stable volume resistivity under temperature changes and preparation method thereof
A conductive composite material and volume resistivity technology, which is applied to conductive materials dispersed in non-conductive inorganic materials and other directions to achieve the effects of reducing PTC effect, simple preparation method and process, and stabilizing volume resistivity
- Summary
- Abstract
- Description
- Claims
- Application Information
AI Technical Summary
Problems solved by technology
Method used
Image
Examples
Embodiment 1
[0033] 1) Add 5gMWNT into 200mL xylene, heat up to 70°C after ultrasonication for 30 minutes at room temperature, add 45g ethylene-ethyl acrylate copolymer EEA, stir for 30min under condensing reflux; add 100mL absolute ethanol, filter; After drying at 90°C for 24 hours, it was shredded to obtain a premix with 10% MWNT content;
[0034] 2) Mix 7.5g of the premix and 21.1g of EEA in a Haake rheometer at 120°C and 60r / m for 30min; after heating up to 140°C, add 16gCB, 4g of polyethylene wax, 0.4g of antioxidant 1010, After mixing at / m for 8 minutes, cut into pieces and granulate;
[0035] 3) Mix the mixture in the previous step with the crosslinking agent DCP at a ratio of 49:1, and mix it on the open mill at 100°C for 6 minutes; then crosslink it on a flat vulcanizer at 180°C, 20MPa, and press for 12 minutes, and hold the pressure Cool to normal temperature to obtain a composite material. The schematic diagram of the conductive network inside the composite material is shown ...
Embodiment 2
[0037] 1) Mix 2.5g of graphene sheet GNP and 25.1g of EVA in a Haake rheometer at 120°C and 60r / m for 30min; after heating up to 140°C, add 17.5g of CB, 4g of polyethylene wax, and 0.4g of antioxidant 1010 , mixed at 45r / m for 8 minutes, then cut into pieces and granulated;
[0038] 2) Mix the mixture of the previous step and the cross-linking agent DCP at a ratio of 99:1, and mix it on an open mill at 100°C for 6 minutes; then cross-link it on a flat vulcanizer at 180°C, 20MPa, and press for 12 minutes, and hold the pressure Cool to normal temperature to obtain a composite material. The schematic diagram of the conductive network inside the composite material is shown in figure 2 , the volume resistivity curve of the obtained composite material as a function of temperature is as follows Figure 4 The curve in 2.
Embodiment 3
[0040] 1) Add 5g of carbon nanofiber CNF into 200mL of xylene, heat up to 70°C after ultrasonication for 30 minutes at room temperature, add 45g of ethylene-vinyl acetate copolymer EVA, stir for 30min under condensing reflux; add 100mL of absolute ethanol, filter ; The filtrate was dried at 90°C for 24 hours and then shredded to obtain a premix with 10% GNFs content;
[0041] 2) Mix 7.5g of the premix and 22.1g of EVA in a Haake rheometer at 120°C and 60r / m for 30min; after heating up to 140°C, add 16gCB, 4g of polyethylene wax, 0.4g of antioxidant 1010, After mixing at / m for 8 minutes, cut into pieces and granulate;
[0042] 3) Mix the mixture in the previous step with the crosslinking agent DCP at a ratio of 49:1, and mix it on the open mill at 100°C for 6 minutes; then crosslink it on a flat vulcanizer at 180°C, 20MPa, and press for 12 minutes, and hold the pressure Cool to normal temperature to obtain a composite material. The schematic diagram of the conductive network...
PUM
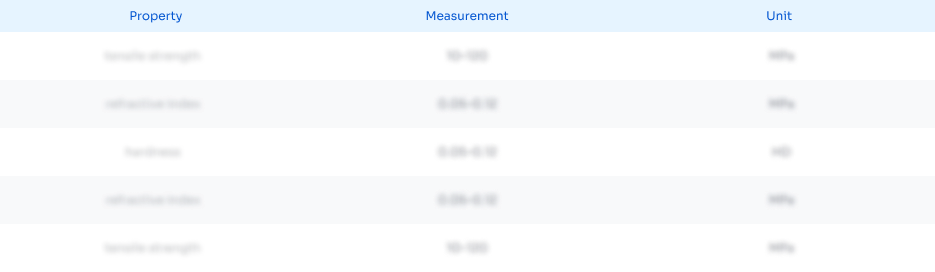
Abstract
Description
Claims
Application Information

- R&D
- Intellectual Property
- Life Sciences
- Materials
- Tech Scout
- Unparalleled Data Quality
- Higher Quality Content
- 60% Fewer Hallucinations
Browse by: Latest US Patents, China's latest patents, Technical Efficacy Thesaurus, Application Domain, Technology Topic, Popular Technical Reports.
© 2025 PatSnap. All rights reserved.Legal|Privacy policy|Modern Slavery Act Transparency Statement|Sitemap|About US| Contact US: help@patsnap.com