1500-1700 DEG C carbon/carbon composite material surface oxidation-resistant coating and preparation method
A carbon composite material and anti-oxidation coating technology, which is applied in the field of 1500-1700 ℃ anti-oxidation coating and preparation on the surface of carbon/carbon composite material, can solve the problem of mismatch of thermal expansion coefficient between the coating and the coating, and improve the anti-oxidation Oxidation performance, simple operation, cost saving effect
- Summary
- Abstract
- Description
- Claims
- Application Information
AI Technical Summary
Problems solved by technology
Method used
Image
Examples
Embodiment 1
[0026] 1) After polishing the C / C composite material with a size of 8mm×8mm×8mm with No. 100, No. 500 and No. 1000 sandpaper in sequence, it was ultrasonically cleaned with absolute ethanol for 30 minutes, and the ultrasonic power was set to 90W. Dry in the oven for later use.
[0027] 2) Weigh the Si powder with a mass fraction of 70-85% and the C powder with a mass fraction of 15-30%, respectively. Then place it in a ball mill for ball milling and mixing for 2 to 4 hours and stir evenly for later use.
[0028] 3) HfO with a mass fraction of 5-15% 2 Powder, 70-85% Si powder, 2-5% B4 C powder and 15-30% carbon powder were weighed separately, then placed in a ball mill and mixed for 2-4 hours and stirred evenly as raw material powder for the first layer of gradient coating on the surface of SiC-coated C / C composite materials; 15-30% HfO 2 Powder, 50-70% Si powder, 3-10% B 4 C powder and 10-20% carbon powder were weighed separately, and then placed in a ball mill and mixed f...
Embodiment 2
[0035] 1) After polishing the C / C composite material with a size of 8mm×8mm×8mm with No. 100, No. 500 and No. 1000 sandpaper in sequence, it was ultrasonically cleaned with absolute ethanol for 30 minutes, and the ultrasonic power was set to 90W. Dry in the oven for later use.
[0036] 2) Weigh the Si powder with a mass fraction of 70-85% and the C powder with a mass fraction of 15-30%, respectively. Then place it in a ball mill for ball milling and mixing for 2 to 4 hours and stir evenly for later use.
[0037] 3) HfO with a mass fraction of 5-15% 2 Powder, 70-85% Si powder, 2-5% B 4 C powder and 15-30% carbon powder were weighed separately, then placed in a ball mill and mixed for 2-4 hours and stirred evenly as raw material powder for the first layer of gradient coating on the surface of SiC-coated C / C composite materials; 15-30% HfO 2 Powder, 50-70% Si powder, 3-10% B 4 C powder and 10-20% carbon powder were weighed separately, and then placed in a ball mill and mixed...
Embodiment 3
[0044] 1) After polishing the C / C composite material with a size of 8mm×8mm×8mm with No. 100, No. 500 and No. 1000 sandpaper in sequence, it was ultrasonically cleaned with absolute ethanol for 30 minutes, and the ultrasonic power was set to 90W. Dry in the oven for later use.
[0045] 2) Weigh the Si powder with a mass fraction of 70-85% and the C powder with a mass fraction of 15-30%, respectively. Then place it in a ball mill for ball milling and mixing for 2 to 4 hours and stir evenly for later use.
[0046] 3) HfO with a mass fraction of 5-15% 2 Powder, 70-85% Si powder, 2-5% B 4 C powder and 15-30% carbon powder were weighed separately, then placed in a ball mill and mixed for 2-4 hours and stirred evenly as raw material powder for the first layer of gradient coating on the surface of SiC-coated C / C composite materials; 15-30% HfO 2 Powder, 50-70% Si powder, 3-10% B 4 C powder and 10-20% carbon powder were weighed separately, and then placed in a ball mill and mixed...
PUM
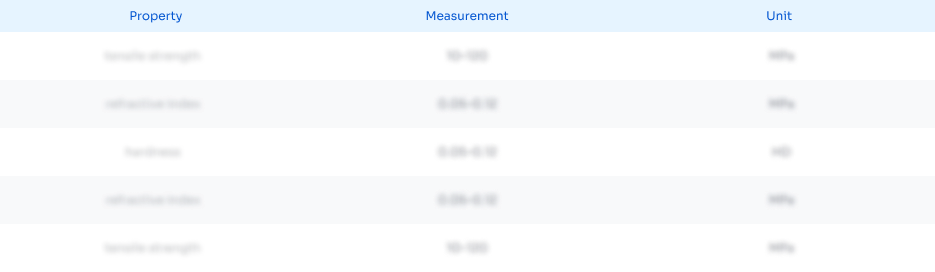
Abstract
Description
Claims
Application Information

- R&D
- Intellectual Property
- Life Sciences
- Materials
- Tech Scout
- Unparalleled Data Quality
- Higher Quality Content
- 60% Fewer Hallucinations
Browse by: Latest US Patents, China's latest patents, Technical Efficacy Thesaurus, Application Domain, Technology Topic, Popular Technical Reports.
© 2025 PatSnap. All rights reserved.Legal|Privacy policy|Modern Slavery Act Transparency Statement|Sitemap|About US| Contact US: help@patsnap.com