Method for improving corrosion performance of surface of light alloy friction-stir welding joint
A friction stir and welded joint technology, applied in welding equipment, non-electric welding equipment, metal processing equipment, etc., can solve the problem of low interface strength, and achieve the effect of improving joint performance, joint structure strengthening, and improving mechanical properties and stability.
- Summary
- Abstract
- Description
- Claims
- Application Information
AI Technical Summary
Problems solved by technology
Method used
Image
Examples
Embodiment Construction
[0018] The present invention will be described in further detail below in conjunction with the accompanying drawings.
[0019] 1) According to the method of the present invention, first, the 6mm thick AZ91E magnesium alloy is subjected to friction stir welding, the welding speed is 100mm / min, the rotation speed of the stirring head is 500r / min, and the downward pressure is controlled to 0.2mm.
[0020] 2) Subsequently, the welding surface is subjected to cold spraying treatment, and the spraying particles are pure aluminum-alumina mixed particles, wherein the pure aluminum particles account for 50%, and the aluminum oxide particles account for 50%. The particle size is 20-30μm, the powder feeding rate is 30g / min, the powder feeding distance is 25mm, and the final coating thickness is 2mm.
[0021] 3) For the post-weld heat treatment of the cold spray coating, the heat treatment temperature is 400°C, the heat treatment time is 2h, the heat treatment atmosphere is an argon envir...
PUM
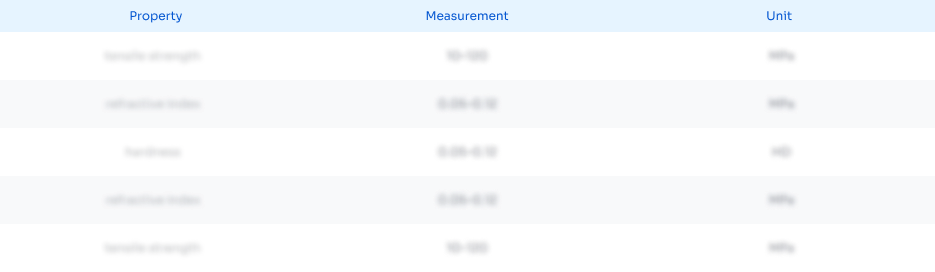
Abstract
Description
Claims
Application Information

- R&D
- Intellectual Property
- Life Sciences
- Materials
- Tech Scout
- Unparalleled Data Quality
- Higher Quality Content
- 60% Fewer Hallucinations
Browse by: Latest US Patents, China's latest patents, Technical Efficacy Thesaurus, Application Domain, Technology Topic, Popular Technical Reports.
© 2025 PatSnap. All rights reserved.Legal|Privacy policy|Modern Slavery Act Transparency Statement|Sitemap|About US| Contact US: help@patsnap.com