Aluminum alloy variable section extruded profile for spaceflight and preparation method of aluminum alloy variable section extruded profile
A technology for extruding profiles and aluminum alloys, which is applied in the field of aerospace aluminum alloy extruded profiles with variable cross-section and its preparation, can solve the problems of low strength and stress concentration in the connection area, and achieves the improvement of strength, and the reduction of crystallization and intragranular potential. The effect of poor and good use value and application prospect
- Summary
- Abstract
- Description
- Claims
- Application Information
AI Technical Summary
Problems solved by technology
Method used
Image
Examples
Embodiment 1
[0036] An aluminum alloy variable-section extruded profile for aerospace, which is composed of the following elements by weight percentage: Zn 5.0%, Cu2.0%, Mn 0.04%, Mg3.0%, Cr0.15%, Fe0.42%, Si≤0.25%, the remainder is Al.
[0037] The preparation method of the aerospace aluminum alloy multi-section extruded profile comprises the following steps:
[0038] (1) According to the element composition, select remelted aluminum ingots with a grade of ≥99.80%, zinc ingots with a purity of ≥99.90%, magnesium ingots with a purity of ≥99.95%, electrolytic copper plates with a purity of 99.99%, Al-4Cr alloy, Al-10Mn alloy, Al-10Fe alloy was used as the raw material.
[0039] (2) Use a resistance reverberatory furnace to melt the remelted aluminum ingot, Al-4Cr alloy, Al-10Mn alloy, and Al-10Fe alloy at 710 °C. After melting, add zinc ingot, magnesium ingot and electrolytic copper plate to the melt, stir and melt into an aluminum alloy melt.
Embodiment 2
[0050] An aluminum alloy variable-section extruded profile for aerospace, which is composed of the following elements by weight percentage: Zn 6.0%, Cu1.0%, Mn 0.1%, Mg2.0%, Cr0.25%, Fe0.35%, Si≤0.25%, the remainder is Al.
[0051] The preparation method of the aerospace aluminum alloy multi-section extruded profile comprises the following steps:
[0052] (1) According to the element composition, select remelted aluminum ingots with a grade of ≥99.80%, zinc ingots with a purity of ≥99.90%, magnesium ingots with a purity of ≥99.95%, electrolytic copper plates with a purity of 99.99%, Al-4Cr alloy, Al-10Mn alloy, Al-10Fe alloy was used as the raw material.
[0053] (2) Use a resistance reverberatory furnace to melt the remelted aluminum ingot, Al-4Cr alloy, Al-10Mn alloy, and Al-10Fe alloy at 750 °C. After melting, add zinc ingot, magnesium ingot and electrolytic copper plate to the melt, stir and melt into an aluminum alloy melt.
Embodiment 3
[0064] An aluminum alloy variable-section extruded profile for aerospace, which is composed of the following elements by weight percentage: Zn 6.0%, Cu2.0%, Mn 0.04%, Mg2.0%, Cr0.20%, Fe0.40%, Si≤0.25%, the remainder is Al.
[0065] The preparation method of the aerospace aluminum alloy multi-section extruded profile comprises the following steps:
[0066] (1) According to the element composition, select remelted aluminum ingots with a grade of ≥99.80%, zinc ingots with a purity of ≥99.90%, magnesium ingots with a purity of ≥99.95%, electrolytic copper plates with a purity of 99.99%, Al-4Cr alloy, Al-10Mn alloy, Al-10Fe alloy was used as the raw material.
[0067] (2) Use a resistance reverberatory furnace to melt the remelted aluminum ingot, Al-4Cr alloy, Al-10Mn alloy, and Al-10Fe alloy at 730 °C. After melting, add zinc ingot, magnesium ingot and electrolytic copper plate to the melt, stir and melt into an aluminum alloy melt.
PUM
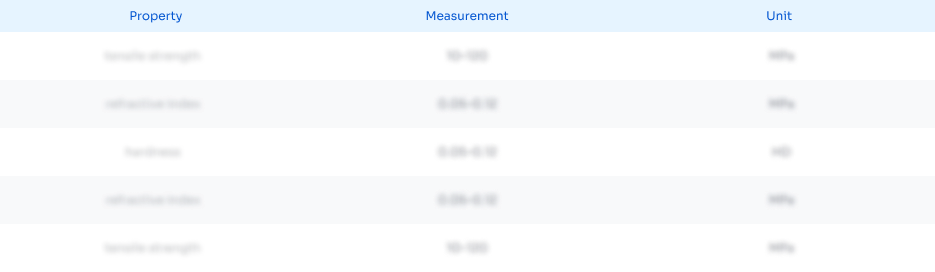
Abstract
Description
Claims
Application Information

- R&D
- Intellectual Property
- Life Sciences
- Materials
- Tech Scout
- Unparalleled Data Quality
- Higher Quality Content
- 60% Fewer Hallucinations
Browse by: Latest US Patents, China's latest patents, Technical Efficacy Thesaurus, Application Domain, Technology Topic, Popular Technical Reports.
© 2025 PatSnap. All rights reserved.Legal|Privacy policy|Modern Slavery Act Transparency Statement|Sitemap|About US| Contact US: help@patsnap.com