Supported noble metal catalysts with performance of resisting high-temperature sintering and preparing method thereof
A noble metal catalyst, sintering performance technology, applied in the field of catalysis, can solve the problem of deactivation of supported noble metal catalysts
- Summary
- Abstract
- Description
- Claims
- Application Information
AI Technical Summary
Problems solved by technology
Method used
Image
Examples
preparation example Construction
[0032] The present invention also provides a preparation method of a supported noble metal catalyst with high temperature sintering resistance, the method comprising:
[0033] Step 1: Add MO to the soluble precursor of the primary carrier x Soluble precursors to obtain composite nanoparticles;
[0034] Step 2: stirring and mixing the composite nanoparticles obtained in step 1 with the secondary carrier to obtain the primary carrier / stabilizer / secondary carrier;
[0035] Step 3: Use the primary carrier / stabilizer / secondary carrier obtained in step 2 with SiO 2 Coating, get primary carrier / stabilizer / secondary carrier @SiO 2 ;
[0036] Step 4: Selectively deposit the active component noble metal on the primary carrier / stabilizer / secondary carrier @SiO obtained in step 3 2 The surface of the primary support in the medium is obtained as a supported noble metal catalyst.
[0037] According to the present invention, MO is added to the soluble precursor of the primary carrier x...
Embodiment 1
[0068] Weigh 0.8g PVP, 138.9mg Ce(NO 3 ) 3 ·6H 2 O and 11.6mg Ni(NO 3 ) 3 ·6H 2 O was dissolved in 80mL of absolute ethanol, and after it was fully dissolved, 0.6mL of precipitant triethylamine was added dropwise and stirred for 0.5h, then heated at 180°C for 24h to obtain Ce 0.8 Ni 0.2 o 2 nanocomposite oxides.
[0069] Weigh 100mg commercial Al 2 o 3 , add 18mL Ce 0.8 Ni 0.2 o 2 The sol was first stirred at room temperature for 2 hours, then stirred and evaporated to dryness at 50° C., then heated to 500° C. at a heating rate of 3° C. / min, and calcined in air for 5 hours. at 5%H 2 / Ar heated at 10°C / min to 300°C, reduced for 3 hours, then raised to 750°C at a rate of 3°C / min in air atmosphere and calcined for 3 hours to obtain Ce 0.8 Ni 0.2-δ o 2-θ / NiAl 2 o 4 / Al 2 o3 catalyst.
[0070] Weigh Ce 0.8 Ni 0.2-δ o 2-θ / NiAl 2 o 4 / Al 2 o 3 Catalyst 50mg was dispersed in 80mL absolute ethanol, ammonia water 4mL was added and sonicated for 30min. Measu...
Embodiment 2
[0082] Weigh 3.2g ZrOCl 2 ·8H 2 O and 0.58g Ni(NO 3 ) 3 ·6H 2 O was dissolved in 20mL of secondary water, and Zr was weighed 4+ and Ni 2+ 6.2 g of the ligand sodium oleate was dissolved in a mixed solution of 40 mL of secondary water and 50 mL of absolute ethanol. Then the above two solutions were mixed, stirred and reacted for 1 hour, then 80 mL of cyclohexane was added to continue stirring and extracting for 1 hour, then transferred to a separatory funnel, allowed to stand for 2 hours and the upper layer solution was collected. Transfer the supernatant to a round-bottomed flask, and distill at 100°C under normal pressure to obtain a yellow viscous liquid. Add cyclohexane solution to the yellow viscous liquid and dilute to 20mL, Zr 0.8 Ni 0.2 o 2 The sol is sealed and stored.
[0083] 100mg commercial Al 2 o 3 Stir and mix with 2mL of the above sol for 2h, then stir and evaporate to dryness at 80°C, and successively in N 2 and in air at a rate of 3°C / min to 500°C...
PUM
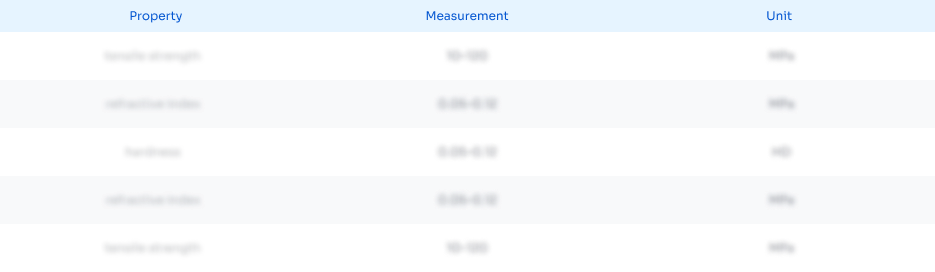
Abstract
Description
Claims
Application Information

- R&D
- Intellectual Property
- Life Sciences
- Materials
- Tech Scout
- Unparalleled Data Quality
- Higher Quality Content
- 60% Fewer Hallucinations
Browse by: Latest US Patents, China's latest patents, Technical Efficacy Thesaurus, Application Domain, Technology Topic, Popular Technical Reports.
© 2025 PatSnap. All rights reserved.Legal|Privacy policy|Modern Slavery Act Transparency Statement|Sitemap|About US| Contact US: help@patsnap.com