Cobalt-based high temperature alloy, preparation method thereof and application in heavy-duty gas turbine
A superalloy and gas turbine technology, which is applied in the field of cobalt-based superalloy and its preparation, can solve the problems such as the inability to meet the design requirements that the inlet temperature of the gas turbine is continuously increased, and achieve the effects of excellent high temperature mechanical properties, high high temperature strength, and excellent oxidation resistance.
- Summary
- Abstract
- Description
- Claims
- Application Information
AI Technical Summary
Problems solved by technology
Method used
Image
Examples
Embodiment 1
[0049] The composition of the alloy in this example (alloy in Example 1) is shown in Table 1, and the preparation process was adopted: melt treatment at 1620°C for 10 minutes, pouring at 1470°C, and shell temperature at 1020°C. Alloy cast structure such as figure 1 As shown, the alloy consists of γ matrix, γ / M 23 C 6 Eutectic, MC and M 23 C 6 carbide composition.
Embodiment 2
[0051] The composition of the alloy in this example (alloy in Example 2) is shown in Table 1, the preparation process adopted is the same as in Example 1, and the tensile properties of the alloy are shown in Table 2. The tensile properties of Mar-M 509 alloy, a typical foreign reburned guide vane material, are shown in Table 3. Through comparison, it can be found that the tensile properties of the alloy of the present invention are slightly higher than that of the Mar-M 509 alloy. Composite curves of thermal strength parameters of comparative alloys ( figure 2 ) It can be seen that the durability performance of the alloy of the present invention at medium and high temperatures is higher than that of the same type of Mar-M 509 equiaxed cobalt-based superalloy.
[0052] The tensile properties of table 2 embodiment 2 alloy
[0053]
[0054] Table 3 Tensile properties of Mar-M 509 alloy
[0055]
Embodiment 3
[0057] The composition of the alloy of this embodiment (the alloy of Embodiment 3) is shown in Table 1, and the preparation process adopted is the same as that of Embodiment 1. The 900°C low cycle fatigue performance of the alloy is as follows: image 3 As shown, it can be seen that the 900°C low cycle fatigue performance of the alloy of the present invention is higher than that of the same kind of Mar-M 509 equiaxed cobalt-based superalloy. at the same time, Figure 4 The hot corrosion weight gain variation curve of the alloy of the present invention at 900°C is shown, and the results show that the hot corrosion resistance of the alloy is equivalent to that of the FSX-414 alloy, and far superior to the hot corrosion resistant equiaxed crystal M38 alloy of the trump card.
PUM
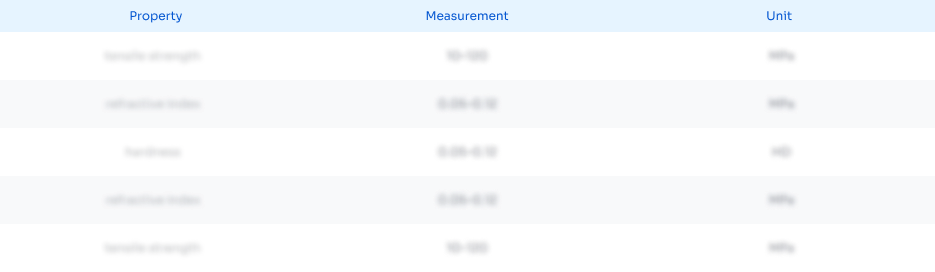
Abstract
Description
Claims
Application Information

- R&D Engineer
- R&D Manager
- IP Professional
- Industry Leading Data Capabilities
- Powerful AI technology
- Patent DNA Extraction
Browse by: Latest US Patents, China's latest patents, Technical Efficacy Thesaurus, Application Domain, Technology Topic, Popular Technical Reports.
© 2024 PatSnap. All rights reserved.Legal|Privacy policy|Modern Slavery Act Transparency Statement|Sitemap|About US| Contact US: help@patsnap.com