Molybdenum cleaning metallurgy method
A clean and molybdenite technology, applied in the field of molybdenum clean metallurgy, can solve environmental pollution and other problems, achieve the effects of simplifying the smelting process, solving sulfur dioxide pollution, and being easy to promote industrialization
- Summary
- Abstract
- Description
- Claims
- Application Information
AI Technical Summary
Problems solved by technology
Method used
Examples
Embodiment 1
[0033] (1) Using the calcified molybdenum calcined sand of molybdenite as raw material, the molybdenum content is 13.2%, and it is leached with 4mol / L nitric acid under normal pressure conditions of 95°C, and the leaching liquid-solid ratio (L / Kg) is 3:1 , the leaching time is 2h, and the nitric acid leach solution containing molybdenum is obtained, and the leaching rate of molybdenum is 99.2%;
[0034] (2) Using 10% P507+90% sulfonated kerosene as the extraction agent, extracting molybdenum under the condition of O / A=2:1, the extraction method is 5-stage countercurrent extraction, and the extraction rate of molybdenum can reach 95% %above. The loaded organic phase and raffinate are obtained by extraction, wherein the loaded phase is subjected to back-extraction of molybdenum, and the raffinate is recycled to step (1) for use after supplementing the nitric acid consumed in the leaching process.
[0035] (3) Use hydrogen peroxide with a mass concentration of 10% as the strippi...
Embodiment 2
[0038] (1) The calcified molybdenum calcined sand of molybdenite is used as raw material, the molybdenum content is 14.5%, and it is leached with 3mol / L hydrochloric acid under normal pressure conditions of 85°C, and the leaching liquid-solid ratio (L / Kg) is 5:1 , the leaching time is 4h to obtain molybdenum-containing hydrochloric acid leaching solution, and the leaching rate of molybdenum is 99.5%;
[0039] (2) Using 30% Cyanex272+70% sulfonated kerosene as the extraction agent, extracting molybdenum under the condition of O / A=1:1, the extraction method is 3-stage countercurrent extraction, and the extraction rate of molybdenum can reach 90.5 %above. The loaded organic phase and raffinate are obtained by extraction, wherein the loaded phase is subjected to back-extraction of molybdenum, and the raffinate is recycled to step (1) for use after supplementing the hydrochloric acid consumed in the leaching process.
[0040] (3) With a mass concentration of 20% hydrogen peroxide ...
Embodiment 3
[0043](1) Using calcified molybdenum calcined sand of molybdenite as raw material, the content of molybdenum is 12.5%, and it is leached with 2mol / L sulfuric acid under normal pressure conditions of 75°C, and the leaching liquid-solid ratio (L / Kg) is 10:1 , the leaching time is 6h to obtain molybdenum-containing sulfuric acid leaching solution, and the leaching rate of molybdenum is 99.6%;
[0044] (2) Using 50% P204 + 50% sulfonated kerosene as the extraction agent, the extraction of molybdenum is carried out under the condition of O / A = 1:3, the extraction method is 5-stage countercurrent extraction, and the extraction rate of molybdenum can reach 99.1% %above. Extraction obtains a loaded organic phase and a raffinate, wherein the loaded phase is subjected to back-extraction of molybdenum, and the raffinate is recycled to step (1) for use after supplementing the sulfuric acid consumed in the leaching process.
[0045] (3) With a mass concentration of 15% hydrogen peroxide s...
PUM
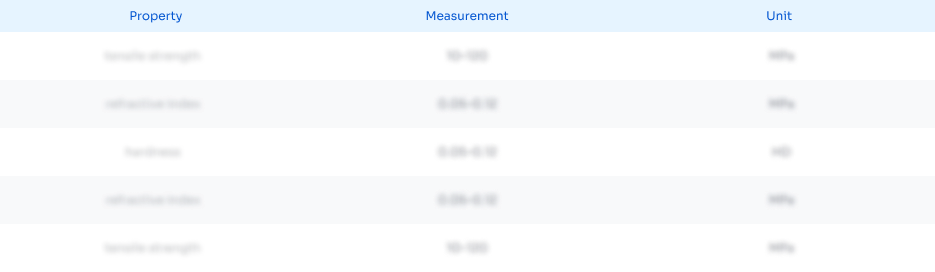
Abstract
Description
Claims
Application Information

- R&D Engineer
- R&D Manager
- IP Professional
- Industry Leading Data Capabilities
- Powerful AI technology
- Patent DNA Extraction
Browse by: Latest US Patents, China's latest patents, Technical Efficacy Thesaurus, Application Domain, Technology Topic, Popular Technical Reports.
© 2024 PatSnap. All rights reserved.Legal|Privacy policy|Modern Slavery Act Transparency Statement|Sitemap|About US| Contact US: help@patsnap.com