A preparing method for polyester composition
A composition and polyester technology, applied in the field of polyester composition preparation, can solve the problems of limited use, decreased film quality, increased filter pressure, etc., and achieves simple preparation process, low gel rate, and easy operation. Effect
- Summary
- Abstract
- Description
- Claims
- Application Information
AI Technical Summary
Problems solved by technology
Method used
Image
Examples
preparation example Construction
[0016] In the preparation method of the present invention, the aromatic dicarboxylic acid and the aliphatic dihydric alcohol are first subjected to an esterification reaction, and then the polymerization reaction is further carried out, specifically, during the period from the end of the esterification reaction to the start of the polymerization reaction Add antimony compound, phosphorus-containing inorganic acid or phosphorus-containing organic compound, and alkali metal phosphate to the reaction system to start the polymerization reaction. After the intrinsic viscosity of the polymerization reactant reaches 0.5dl / g and before the end of the polymerization reaction, Add manganese compound to the reaction system in the polymerization reactant, and continue the polymerization reaction until completion.
[0017] The manganese compound has the effect of inhibiting oxidation, can capture oxygen free radicals, and promote the inactivation of free radicals, which to a certain extent ...
Embodiment 1
[0046] At 250°C, 166 parts by weight of terephthalic acid (TPA) and 72 parts by weight of ethylene glycol (EG) (that is, the molar ratio of EG to TPA is 1.15:1) were subjected to esterification reaction, through the by-product water Production capacity, when the esterification reaction rate reaches over 97%, transfer the obtained new diethylene terephthalate (BHT) oligomers to the polymerization tank. Add antimony trioxide (AO) catalyst which is equivalent to 80ppm of the total amount of the polyester composition in terms of antimony to the polymerization kettle in sequence, add EG solution after 5 minutes, add 70ppm sodium dihydrogen phosphate (NaH 2 PO 4 2H 2 O) and the mixed solution of stabilizer phosphoric acid equivalent to 20ppm of the total amount of the polyester composition in terms of phosphorus element, the pressure is reduced and the temperature is raised 5 minutes after the addition is completed. When the reaction time is 3 hours and the intrinsic viscosity is 0...
Embodiment 2
[0048] At 250°C, 166 parts by weight of terephthalic acid (TPA) and 72 parts by weight of ethylene glycol (EG) (that is, the molar ratio of EG to TPA is 1.15:1) were subjected to esterification reaction, through the by-product water Production capacity, when the esterification reaction rate reaches over 97%, transfer the obtained new diethylene terephthalate (BHT) oligomers to the polymerization tank. Add antimony trioxide (AO) catalyst which is equivalent to 80ppm of the total amount of the polyester composition in terms of antimony to the polymerization kettle in sequence, add EG after 5 minutes, and add 70ppm of sodium dihydrogen phosphate (NaH 2 PO 4 2H 2 O) and the mixed solution of stabilizer phosphoric acid equivalent to 20ppm of the total amount of the polyester composition in terms of phosphorus element, start to reduce pressure and heat up 5 minutes after the addition, when the reaction time is 2 hours and 30 minutes, the intrinsic viscosity is 0.55dl / At the time ...
PUM
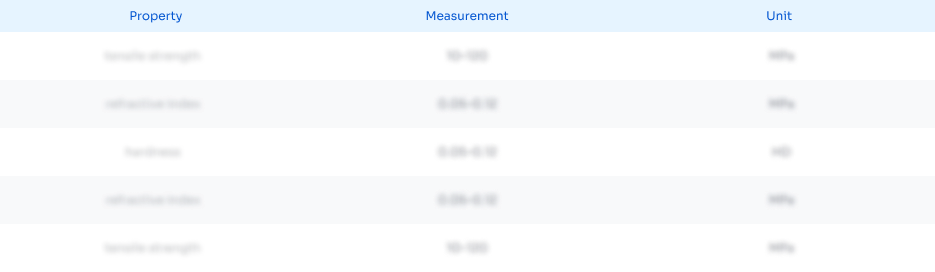
Abstract
Description
Claims
Application Information

- R&D
- Intellectual Property
- Life Sciences
- Materials
- Tech Scout
- Unparalleled Data Quality
- Higher Quality Content
- 60% Fewer Hallucinations
Browse by: Latest US Patents, China's latest patents, Technical Efficacy Thesaurus, Application Domain, Technology Topic, Popular Technical Reports.
© 2025 PatSnap. All rights reserved.Legal|Privacy policy|Modern Slavery Act Transparency Statement|Sitemap|About US| Contact US: help@patsnap.com