Synthetic fiber dyeing dispersion dye microcapsule and preparation method thereof
A technology of disperse dyes and synthetic fibers, which is applied in the direction of microcapsule preparation, dyeing method, microsphere preparation, etc. It can solve the problems of increasing the difficulty of wastewater treatment and organic acid residue, achieve good isolation effect, improve utilization rate, and reduce processing difficulty Effect
- Summary
- Abstract
- Description
- Claims
- Application Information
AI Technical Summary
Problems solved by technology
Method used
Examples
Embodiment 1
[0027] (1) Wall material preparation: first mix 100g N-hydroxyethylacrylamide, 200g N-isopropylacrylamide, 8g cross-linking agent N,N′-methylenebisacrylamide and 10g emulsifier dodecyl Dissolve sodium sulfate in deionized water, keep stirring at 35-45°C for 0.5h under the protection of nitrogen, then raise the temperature to 70-80°C and keep stirring for 0.5h, add 10g of initiator ammonium persulfate, continue to heat at 70-80°C Keep stirring for 3 hours, then add 500g carboxymethyl-β-cyclodextrin and 5g 98% concentrated sulfuric acid, heat up to reflux state and keep stirring for 3 hours, the resulting mixture is concentrated under reduced pressure to make a paste, and the paste is naturally cooled to room temperature Send it into a freeze dryer, and dry the obtained solid to make a fine powder through a superfine pulverizer, that is, the wall material;
[0028] (2) Single-layer wall construction: Mix 100g disperse dye with 3000g deionized water, stir and disperse evenly, add...
Embodiment 2
[0031] (1) Wall material preparation: first mix 100g N-hydroxyethylacrylamide, 200g N-isopropylacrylamide, 8g cross-linking agent N,N′-methylenebisacrylamide and 10g emulsifier dodecyl Dissolve sodium sulfate in deionized water, keep stirring at 35-45°C for 0.5h under the protection of nitrogen, then raise the temperature to 70-80°C and keep stirring for 0.5h, add 10g of initiator ammonium persulfate, continue to heat at 70-80°C Keep stirring for 3 hours, then add 500g carboxymethyl-β-cyclodextrin and 5g 98% concentrated sulfuric acid, heat up to reflux state and keep stirring for 3 hours, the resulting mixture is concentrated under reduced pressure to make a paste, and the paste is naturally cooled to room temperature Send it into a freeze dryer, and dry the obtained solid to make a fine powder through a superfine pulverizer, that is, the wall material;
[0032] (2) Single-layer wall construction: Mix 100g disperse dye with 3000g deionized water, stir and disperse evenly, add...
Embodiment 3
[0046] Adopt embodiment 1-2, comparative example 1-3 to prepare disperse dye microcapsules respectively, wherein disperse dye all adopts the C.I. disperse blue 56 that same manufacturer produces, and test the relevant performance index of prepared disperse dye microcapsule, test result is as table 1.
[0047] The performance index test result of the prepared disperse dye microcapsules of the present invention of table 1
[0048] group
PUM
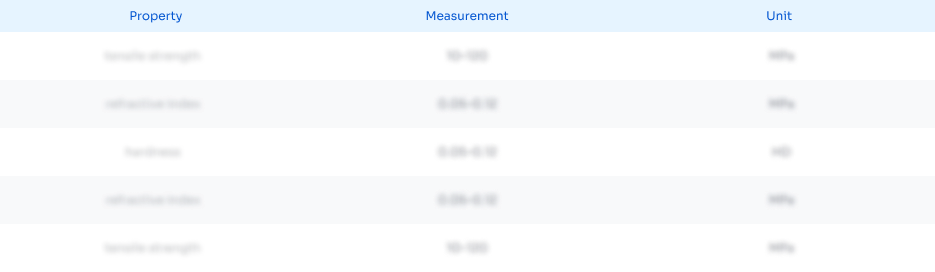
Abstract
Description
Claims
Application Information

- R&D Engineer
- R&D Manager
- IP Professional
- Industry Leading Data Capabilities
- Powerful AI technology
- Patent DNA Extraction
Browse by: Latest US Patents, China's latest patents, Technical Efficacy Thesaurus, Application Domain, Technology Topic, Popular Technical Reports.
© 2024 PatSnap. All rights reserved.Legal|Privacy policy|Modern Slavery Act Transparency Statement|Sitemap|About US| Contact US: help@patsnap.com