An industrial in-situ synthesis method of W-based composite powder that can add WC strengthening phase
A composite powder, in-situ synthesis technology, used in the field of refractory metals and powder metallurgy
- Summary
- Abstract
- Description
- Claims
- Application Information
AI Technical Summary
Problems solved by technology
Method used
Image
Examples
Embodiment 1
[0024] First, weigh 370 grams of WC and mix them with absolute ethanol, and perform ball milling. The mass ratio of balls to powder is 10:1, the speed of the ball mill is 2000r / min, and the milling time is 65h; weigh 129 grams of WO 3 Mix with absolute ethanol, and perform ball milling, the mass ratio of balls to powder is 5:1, the speed of the ball mill is 520r / min, and the ball milling time is 50h. Then ball milled WC, WO 3The powder is mixed by ball milling twice, the mass ratio of balls to powder is 3:1, the volume ratio of absolute ethanol to material is 1:1, the rotational speed of the ball mill is 200r / min, and the ball milling time is 20 hours. After that, put the above powder in a drying oven for drying treatment, and then put it in a vacuum furnace for reaction. The vacuum degree is 10 Pa, and the temperature is raised to 950 ° C for 3 hours to prepare a composite powder with WC evenly distributed on the W matrix. The mass ratio of WC is 10wt.%. In this embodiment,...
Embodiment 2
[0026] First take 375 grams of WC and mix them with absolute ethanol, and carry out ball milling, the mass ratio of balls and powder is 10:1, the rotating speed of ball mill is 2000r / min, and the ball milling time is 65h; It is 150-200nm, so the CuO raw material is not pretreated by ball milling. Afterwards, CuO and WC after ball milling were mixed by secondary ball milling. The mass ratio of balls to powder was 3:1, the volume ratio of absolute ethanol to material was 1:1, the speed of ball mill was 320r / min, and the ball milling time was 30 hours. Afterwards, the above-mentioned powder was placed in a drying oven for drying treatment, and then placed in a tube furnace for reaction. The argon protective atmosphere was used, and the flow rate was 1L / min. The temperature was raised to 850°C and kept for 3h, and the W25Cu matrix was prepared. Composite powder, wherein the mass ratio of WC is 15wt.%. In this embodiment, the microscopic appearance of the raw material powder and t...
PUM
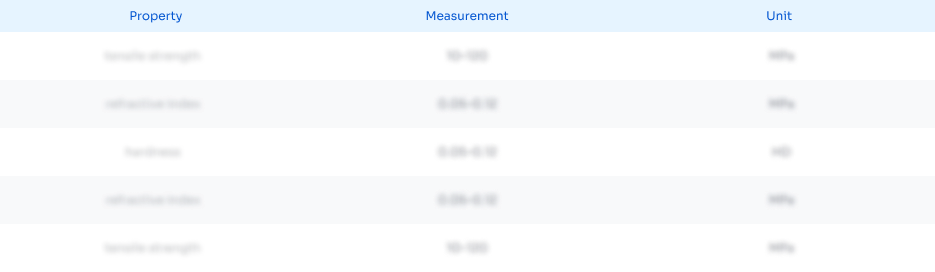
Abstract
Description
Claims
Application Information

- R&D
- Intellectual Property
- Life Sciences
- Materials
- Tech Scout
- Unparalleled Data Quality
- Higher Quality Content
- 60% Fewer Hallucinations
Browse by: Latest US Patents, China's latest patents, Technical Efficacy Thesaurus, Application Domain, Technology Topic, Popular Technical Reports.
© 2025 PatSnap. All rights reserved.Legal|Privacy policy|Modern Slavery Act Transparency Statement|Sitemap|About US| Contact US: help@patsnap.com