Method for separating zinc-cadmium-lead alloy materials from copper-cadmium slag and nickel-cobalt slag generated in zinc smelting process
A technology for copper-cadmium slag and nickel-cobalt slag is applied in the field of separating zinc-cadmium-lead alloy materials, which can solve the problems of large amount of pollutants, low metal recovery rate, lengthy process, etc., and achieves fast enrichment speed and comprehensive utilization rate of resources. High, simple separation process effect
- Summary
- Abstract
- Description
- Claims
- Application Information
AI Technical Summary
Problems solved by technology
Method used
Examples
Embodiment 1
[0026] This embodiment provides a method for separating zinc-cadmium-lead alloy materials from copper-cadmium slag and nickel-cobalt slag produced in the zinc smelting process. The dried copper cadmium slag is mixed according to copper cadmium slag: coal powder: quicklime (mass ratio) = 100: 0.5: 0.5. After the ingredients are mixed evenly, use a briquetting machine to press the ball under a pressure of 24MPa to make Put the mixture pellets in a graphite crucible and put them in a vacuum distillation furnace, turn on the vacuum pump, make the pressure in the vacuum furnace below 200Pa, start heating, heat it to 1000°C for 5 hours, and cool down after the heat preservation is over After reaching normal temperature, break the vacuum, and collect the distillate obtained by distillation, which is the separated lead-zinc-cadmium alloy material.
[0027] Weigh the distillation residue, analyze the content of lead, zinc and cadmium, and calculate the volatilization rate of lead, zin...
Embodiment 2
[0029] This embodiment provides a method for separating zinc-cadmium-lead alloy materials from copper-cadmium slag and nickel-cobalt slag produced in the zinc smelting process. The dried copper cadmium slag is mixed according to copper cadmium slag: coal powder: quicklime powder (mass ratio) = 100: 50: 50. After the ingredients are mixed evenly, use a ball pressing machine to press the ball under a pressure of 24MPa to make a ball of φ10mm Put the mixture pellets in a graphite crucible and put them in a vacuum distillation furnace, turn on the vacuum pump to make the pressure in the vacuum furnace below 200Pa, start heating, heat it to 1000°C for 5 hours, and cool down to room temperature after the heat preservation is over. After breaking the vacuum, collecting the distillate obtained by distillation is the separated lead-zinc-cadmium alloy material.
[0030] Weigh the distillation residue, analyze the content of lead, zinc and cadmium, and calculate the volatilization rate o...
Embodiment 3
[0032] This embodiment provides a method for separating zinc-cadmium-lead alloy materials from copper-cadmium slag and nickel-cobalt slag produced in the zinc smelting process. The dried copper cadmium slag is mixed according to copper cadmium slag: coal powder: quicklime powder (mass ratio) = 100: 0.5: 0.5, and after the ingredients are mixed evenly, use a ball pressing machine to press the ball at a pressure of 24MPa to make a ball of φ10mm Put the mixture pellets in a graphite crucible and put them in a vacuum distillation furnace, turn on the vacuum pump to make the pressure in the vacuum furnace below 200Pa, start heating, heat it to 900°C for 0.5 hours, and cool it down to room temperature after the heat preservation is over After breaking the vacuum, collecting the distillate obtained by distillation is the separated lead-zinc-cadmium alloy material.
[0033] Weigh the distillation residue, analyze the content of lead, zinc and cadmium, and calculate the volatilization ...
PUM
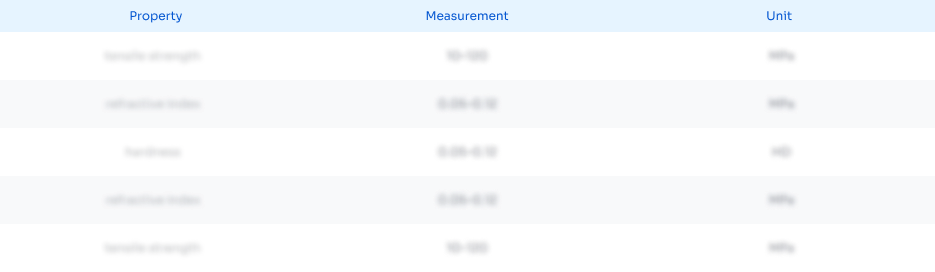
Abstract
Description
Claims
Application Information

- R&D
- Intellectual Property
- Life Sciences
- Materials
- Tech Scout
- Unparalleled Data Quality
- Higher Quality Content
- 60% Fewer Hallucinations
Browse by: Latest US Patents, China's latest patents, Technical Efficacy Thesaurus, Application Domain, Technology Topic, Popular Technical Reports.
© 2025 PatSnap. All rights reserved.Legal|Privacy policy|Modern Slavery Act Transparency Statement|Sitemap|About US| Contact US: help@patsnap.com