Deep hydrolysis method of aluminum nitride in aluminum ash
A technology of aluminum nitride and aluminum ash, which is applied in the direction of chemical instruments and methods, ammonium chloride, ammonium halide, etc., can solve the problems of long cycle, incomplete hydrolysis, and slow hydrolysis speed of aluminum nitride, so as to improve the hydrolysis efficiency, Realize the effect of resource utilization
- Summary
- Abstract
- Description
- Claims
- Application Information
AI Technical Summary
Problems solved by technology
Method used
Examples
Embodiment 1
[0025] First crush 1kg of aluminum ash with an impact crusher to less than 10mm, then heat the aluminum ash to 200°C, leaching the aluminum ash and water in a wet sealed grinding at a ratio of 3:1, the ammonia gas generated during the grinding process Absorb with water to obtain ammonia water, grind ore for 30 minutes, perform plate-and-frame filter press to obtain filter cake and filtrate, analyze the content of aluminum nitride in the filter cake, it is found that aluminum nitride hydrolyzed aluminum is 99.21%, and the filtrate is evaporated to obtain industrial Salt.
Embodiment 2
[0027] First crush 1kg of aluminum ash to less than 10mm with an impact crusher, then heat the aluminum ash to 300°C, leaching the aluminum ash and water according to the ratio of 1:3 by wet sealed grinding, and the ammonia gas generated during the grinding process Ammonium chloride was obtained by absorption with hydrochloric acid. After grinding for 90 minutes, plate and frame pressure filtration was carried out to obtain filter cake and filtrate. The content of aluminum nitride in the filter cake was analyzed. It was found that the hydrolyzed aluminum of aluminum nitride was 99.31%, and the filtrate evaporated Then get industrial salt.
Embodiment 3
[0029] First crush 1kg of aluminum ash to less than 10mm with an impact crusher, then heat the aluminum ash to 100°C, leaching the aluminum ash and hot water in a wet sealed grinding at a ratio of 2:1, the ammonia generated during the grinding process Ammonium sulfate was obtained by absorbing the gas with sulfuric acid. After grinding for 60 minutes, the plate and frame filter was carried out to obtain the filter cake and filtrate. The content of aluminum nitride in the filter cake was analyzed. It was found that the hydrolyzed aluminum of aluminum nitride was 99.51%, and the filtrate evaporated Then get industrial salt.
PUM
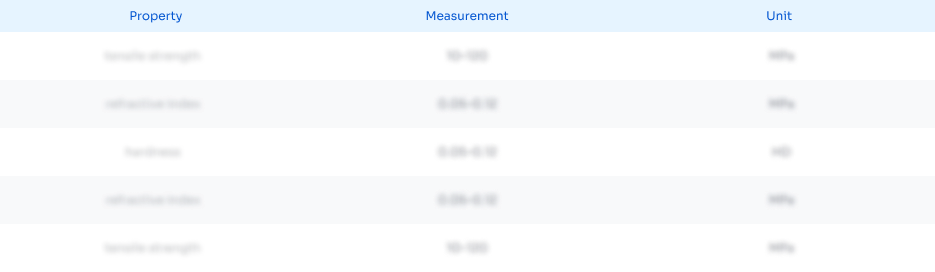
Abstract
Description
Claims
Application Information

- R&D Engineer
- R&D Manager
- IP Professional
- Industry Leading Data Capabilities
- Powerful AI technology
- Patent DNA Extraction
Browse by: Latest US Patents, China's latest patents, Technical Efficacy Thesaurus, Application Domain, Technology Topic, Popular Technical Reports.
© 2024 PatSnap. All rights reserved.Legal|Privacy policy|Modern Slavery Act Transparency Statement|Sitemap|About US| Contact US: help@patsnap.com