Preparation method for in-situ forming of hexagonal phosphorspath coating on surface of titanium-based nanotube
A technology of hexagonal flakes and nanotubes is applied in the field of preparation of in-situ formation of hexagonal flake apatite coating on the surface of titanium-based nanotubes, which can solve the problems of high temperature, lack of chemical action, large internal stress, etc.
- Summary
- Abstract
- Description
- Claims
- Application Information
AI Technical Summary
Problems solved by technology
Method used
Image
Examples
Embodiment 1
[0019] Take a 1cm × 1cm pure titanium sheet and polish it with silicon carbide sandpaper from 400 mesh, 800 mesh, 1200 mesh, and 1500 mesh in sequence until the surface is smooth, ultrasonicate in acetone, ethanol and deionized water for 10 minutes in sequence, and dry it for later use. Take 30 g of glycerol and deionized water respectively, add 0.06 g of ammonium fluoride to form a glycerin / deionized water / ammonium fluoride system electrolyte, use polished and smooth titanium as the anode, platinum as the cathode, and a voltage of 25 V Anodized in the electrolyte for 2 h under the same conditions, the samples were taken out, washed with deionized water, dried naturally and then placed in a muffle furnace, heated from room temperature to 400 °C at a heating rate of 2 °C / min. Cool down (see pictures of titanium nanotubes Figure 1 ). The sample was placed in a calcium chloride polyvinyl alcohol aqueous solution with a concentration of 0.1 M, placed in a vacuum oven, evacuated ...
Embodiment 2
[0021] Take a 2cm × 1cm pure titanium sheet and polish it with silicon carbide sandpaper from 400 mesh, 800 mesh, 1200 mesh, and 1500 mesh in sequence until the surface is smooth, ultrasonicate in acetone, ethanol and deionized water for 10 minutes in sequence, and dry it for later use. Take 40 g of glycerol and deionized water respectively, add 0.08 g of ammonium fluoride to form a glycerin / deionized water / ammonium fluoride system electrolyte, use polished and smooth titanium as the anode, platinum as the cathode, and a voltage of 25 V Anodized in the electrolyte for 3 h under the same conditions, the samples were taken out, washed with deionized water, dried naturally, then placed in a muffle furnace, and heated from room temperature to 350 °C at a heating rate of 1 °C / min. Cool down. Place the sample in a calcium chloride polyvinyl alcohol aqueous solution with a concentration of 0.05 M, place it in a vacuum oven, evacuate to 20 Pa at 37°C, take it out after holding the pre...
Embodiment 3
[0023] Take a 1cm × 1cm pure titanium sheet and polish it with silicon carbide sandpaper from 400 mesh, 800 mesh, 1200 mesh, and 1500 mesh in sequence until the surface is smooth, ultrasonicate in acetone, ethanol and deionized water for 10 minutes in sequence, and dry it for later use. Take 10 g of glycerol and deionized water respectively, add 0.02 g of ammonium fluoride to form a glycerin / deionized water / ammonium fluoride system electrolyte, use a polished and smooth titanium sheet as the anode, and a platinum sheet as the cathode, with a voltage of 25 V Anodized in the electrolyte for 1 h under the same conditions, the samples were taken out, washed with deionized water, dried naturally, then placed in a muffle furnace, heated from room temperature to 400 °C at a heating rate of 3 °C / min, and kept for 2 h. Cool down. Place the sample in a calcium chloride polyvinyl alcohol aqueous solution with a concentration of 0.2 M, place it in a vacuum oven, evacuate to 30 Pa at 37°C,...
PUM
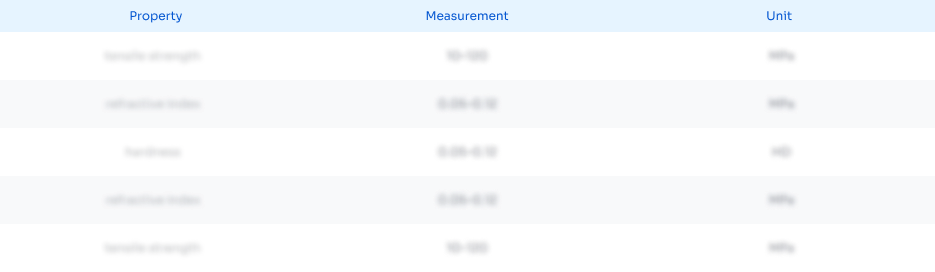
Abstract
Description
Claims
Application Information

- R&D Engineer
- R&D Manager
- IP Professional
- Industry Leading Data Capabilities
- Powerful AI technology
- Patent DNA Extraction
Browse by: Latest US Patents, China's latest patents, Technical Efficacy Thesaurus, Application Domain, Technology Topic, Popular Technical Reports.
© 2024 PatSnap. All rights reserved.Legal|Privacy policy|Modern Slavery Act Transparency Statement|Sitemap|About US| Contact US: help@patsnap.com