Preparation method of anti-corrosion rare earth permanent magnet material
A technology of rare earth permanent magnets and preparation steps, which is applied in the direction of magnetic materials, inductance/transformer/magnet manufacturing, magnetic objects, etc. It can solve the problems of poor anti-corrosion performance, low working temperature, and low Curie temperature, and achieve thermal shock resistance. The effect of increasing, increasing working temperature, and increasing Curie temperature
- Summary
- Abstract
- Description
- Claims
- Application Information
AI Technical Summary
Problems solved by technology
Method used
Image
Examples
example 1
[0027]Prepare a sodium borohydride solution with a mass fraction of 10%, add a mass fraction of 40% sodium hydroxide solution to the sodium borohydride solution to adjust the pH to 10.8, obtain an alkalized sodium borohydride solution, and prepare a mass fraction of 5% sulfuric acid Ferrous solution, under the protection of nitrogen, add the alkalized sodium borohydride solution dropwise to the ferrous sulfate solution, stir until no bubbles are generated, and obtain a black suspension; Min speed centrifugation for 10 min, remove the supernatant and separate the black precipitate, wash the black precipitate with water and absolute ethanol three times in turn, transfer to a vacuum drying oven with a set temperature of 70°C for 20 h to obtain nano Iron powder: Disperse 30g of nano-iron powder in 100mL of cyclohexane, place it in an ultrasonic oscillator and ultrasonically treat it at a frequency of 30kHz for 15min, filter and separate to obtain ultrasonically treated iron powder,...
example 2
[0029] Prepare a sodium borohydride solution with a mass fraction of 10%, add a mass fraction of 40% sodium hydroxide solution to the sodium borohydride solution to adjust the pH to 10.9, obtain an alkalized sodium borohydride solution, and prepare a mass fraction of 5% sulfuric acid Ferrous solution, under the protection of nitrogen, add the alkalized sodium borohydride solution dropwise to the ferrous sulfate solution, stir until no bubbles are generated, and obtain a black suspension; The speed of centrifugation was 11min, and the supernatant was removed to separate the black precipitate, which was washed with water and absolute ethanol four times in turn, and then transferred to a vacuum drying oven with a set temperature of 75°C for 22 hours to obtain nano Iron powder: Disperse 34g of nano-iron powder in 110mL of cyclohexane, place it in an ultrasonic oscillator and ultrasonically treat it at a frequency of 31kHz for 18min, filter and separate to obtain ultrasonically trea...
example 3
[0031] Prepare a sodium borohydride solution with a mass fraction of 10%, add a mass fraction of 40% sodium hydroxide solution to the sodium borohydride solution to adjust the pH to 11.2, obtain an alkalized sodium borohydride solution, and prepare a mass fraction of 5% sulfuric acid Ferrous solution, under the protection of nitrogen, add the alkalized sodium borohydride solution dropwise to the ferrous sulfate solution, stir until no bubbles are generated, and obtain a black suspension; Min speed centrifugation for 12 minutes, remove the supernatant and separate the black precipitate, wash the black precipitate with water and absolute ethanol for 5 times, then transfer to a vacuum drying oven with a set temperature of 80°C for 24 hours to obtain nano Iron powder: Disperse 35g of nano-iron powder in 120mL of cyclohexane, place it in an ultrasonic oscillator for 20min at a frequency of 32kHz, and then filter and separate to obtain ultrasonically treated iron powder. Disperse the...
PUM
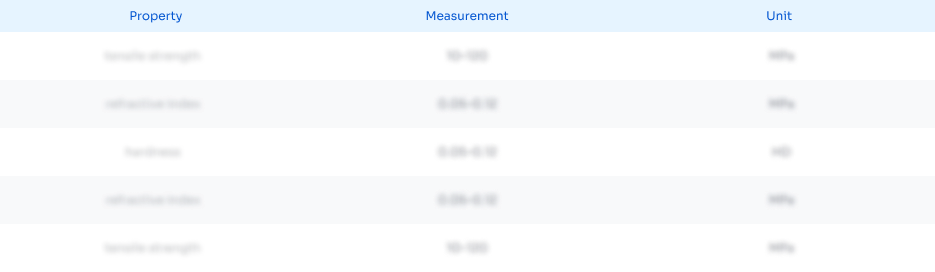
Abstract
Description
Claims
Application Information

- R&D Engineer
- R&D Manager
- IP Professional
- Industry Leading Data Capabilities
- Powerful AI technology
- Patent DNA Extraction
Browse by: Latest US Patents, China's latest patents, Technical Efficacy Thesaurus, Application Domain, Technology Topic, Popular Technical Reports.
© 2024 PatSnap. All rights reserved.Legal|Privacy policy|Modern Slavery Act Transparency Statement|Sitemap|About US| Contact US: help@patsnap.com