Method for optimizing production process of thionyl chloride
A technology of thionyl chloride and production process, which is applied in the field of optimizing the production process of thionyl chloride, can solve the problems such as the risk of overpressure leakage of distillation system pressure rise, material leakage environment, easy agglomeration of sulfur, etc., so as to prevent a large amount of sulfur from entering In the tower, the effect of reducing leakage and reducing the risk of leakage
- Summary
- Abstract
- Description
- Claims
- Application Information
AI Technical Summary
Problems solved by technology
Method used
Image
Examples
Embodiment 1
[0025] The method for optimizing the production process of thionyl chloride of the present invention comprises the following steps:
[0026] (1) The liquid sulfur level in the liquid sulfur tank 1 is 100mm, and after the liquid sulfur is metered by the metering pump 2, it is 160kg / h according to the feed rate and squeezed into the distillation tower 4 (the tower top temperature is 70 ℃, and the pressure is -5Kpa; The temperature at the bottom of the tower is 120 DEG C) in the atomization device 3;
[0027] (2) Thionyl chloride crude product feed rate is 7m 3 / h, mixed with liquid sulfur at the top of distillation tower 4;
[0028] (3) Sulfur dichloride in the crude thionyl chloride reacts with liquid sulfur to generate a heavier component, sulfur monochloride, which is extracted from the bottom of the distillation tower 4, and the remaining crude thionyl chloride enters reflux after being condensed by the condenser 5 In the tank 6 (the reflux ratio is 1:1.5), part of the liq...
Embodiment 2
[0030] The method for optimizing the production process of thionyl chloride of the present invention comprises the following steps:
[0031] (1) The liquid sulfur liquid level in the liquid sulfur tank 1 is 700mm, and after the liquid sulfur is measured by the metering pump 2, it is 170kg / h according to the feed rate and squeezed into the distillation tower 4 (the temperature at the top of the tower is 73°C, and the pressure is 10Kpa; The bottom temperature is 130 ℃) in the atomization device 3;
[0032] (2) Thionyl chloride crude product feed rate is 7.5m 3 / h, mixed with liquid sulfur at the top of distillation tower 4;
[0033] (3) Sulfur dichloride in the crude thionyl chloride reacts with liquid sulfur to generate a heavier component, sulfur monochloride, which is extracted from the bottom of the distillation tower 4, and the remaining crude thionyl chloride enters reflux after being condensed by the condenser 5 In the tank 6 (the reflux ratio is 1:2), part of the liqui...
Embodiment 3
[0035] The method for optimizing the production process of thionyl chloride of the present invention comprises the following steps:
[0036] (1) The liquid sulfur liquid level in the liquid sulfur tank 1 is 1000mm, and after the liquid sulfur is measured by the metering pump 2, it is 200kg / h according to the feed rate and squeezed into the distillation tower 4 (the temperature at the top of the tower is 80°C, and the pressure is 20Kpa; The bottom temperature is 135°C) in the atomization device;
[0037] (2) Thionyl chloride crude product feed rate is 8m 3 / h, mixed with liquid sulfur at the top of distillation tower 4;
[0038] (3) Sulfur dichloride in the crude thionyl chloride reacts with liquid sulfur to generate a heavier component, sulfur monochloride, which is extracted from the bottom of the distillation tower 4, and the remaining crude thionyl chloride enters reflux after being condensed by the condenser 5 In the tank 6 (the reflux ratio is 1:3), part of the liquid p...
PUM
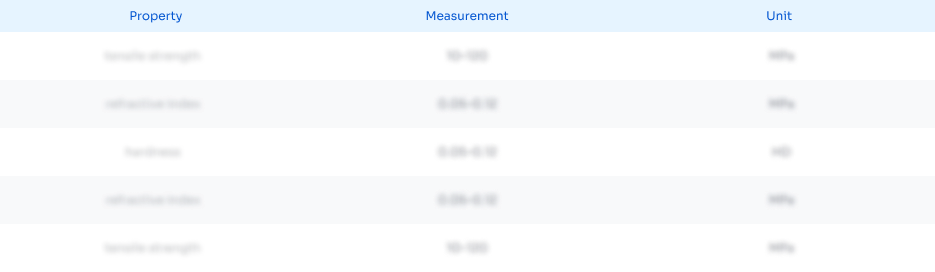
Abstract
Description
Claims
Application Information

- R&D
- Intellectual Property
- Life Sciences
- Materials
- Tech Scout
- Unparalleled Data Quality
- Higher Quality Content
- 60% Fewer Hallucinations
Browse by: Latest US Patents, China's latest patents, Technical Efficacy Thesaurus, Application Domain, Technology Topic, Popular Technical Reports.
© 2025 PatSnap. All rights reserved.Legal|Privacy policy|Modern Slavery Act Transparency Statement|Sitemap|About US| Contact US: help@patsnap.com