Preparation method of composite heat-insulating mortar based on shaped phase change material
A technology of composite thermal insulation mortar and phase change materials, which is applied in the field of building materials, can solve the problems of low utilization rate and insufficient resources per capita, and achieve the effects of good stability, cost reduction and excellent mechanical properties
- Summary
- Abstract
- Description
- Claims
- Application Information
AI Technical Summary
Problems solved by technology
Method used
Examples
Embodiment 1
[0023] A method for preparing a composite thermal insulation mortar based on a shaped phase change material, comprising the following steps:
[0024] (1) Mix and stir erythritol and purified water until the solid dissolves to obtain a solution; add expanded graphite to the solution mixed with titanate coupling agent and isopropanol at a mass ratio of 1:1.5, and stir at 500rpm Dry at 100-110°C under normal pressure for 2 hours, then dry under vacuum at 100-110°C for 3 hours, and finally place it in a muffle furnace at 500°C for 3 hours. After grinding, add it to the above solution, and stir and mix at 1000rpm for 30 minutes; Obtain a dispersion; vacuum dry the prepared dispersion at 100°C for 5 hours to obtain a mixed powder; wherein, the mass ratio of erythritol to purified water is 1:0.5; the mass ratio of erythritol to expanded graphite is 20: 1;
[0025] (2) Composite sintering is carried out after the mixed powder prepared in step (1) is pressed, and after sintering, it i...
Embodiment 2
[0028] A method for preparing a composite thermal insulation mortar based on a shaped phase change material, comprising the following steps:
[0029] (1) Mix and stir erythritol and purified water until the solid dissolves to obtain a solution; add expanded graphite to the solution mixed with titanate coupling agent and isopropanol at a mass ratio of 1:3, and stir at 500rpm Dry at 100-110°C under normal pressure for 4 hours, then dry at 100-110°C under vacuum for 5 hours, and finally place it in a muffle furnace at 700°C for 5 hours. After the grinding treatment, add it to the above solution, and stir and mix at 1000rpm for 30 minutes; Obtain a dispersion; dry the prepared dispersion in vacuum at 120°C for 15 hours to obtain a mixed powder; wherein, the mass ratio of erythritol to purified water is 1:2; the mass ratio of erythritol to expanded graphite is 20: 3;
[0030] (2) Composite sintering is carried out after the mixed powder prepared in step (1) is pressed, and after s...
Embodiment 3
[0033] A method for preparing a composite thermal insulation mortar based on a shaped phase change material, comprising the following steps:
[0034] (1) Mix and stir erythritol and pure water until the solid dissolves to obtain a solution; add expanded graphite to the solution mixed with titanate coupling agent and isopropanol at a mass ratio of 1:2, and stir at 500rpm Dry at 100-110°C under normal pressure for 3 hours, then dry at 100-110°C under vacuum for 3 hours, and finally place it in a muffle furnace at 550°C for 3 hours. After grinding, add it to the above solution, and stir and mix at 1000rpm for 30 minutes; Obtain a dispersion liquid; vacuum dry the prepared dispersion liquid at 105°C for 7 hours to obtain a mixed powder; wherein, the mass ratio of erythritol to purified water is 1:1; the mass ratio of erythritol to expanded graphite is 20: 1.5;
[0035] (2) Composite sintering is carried out after the mixed powder obtained in step (1) is pressed and molded, and af...
PUM
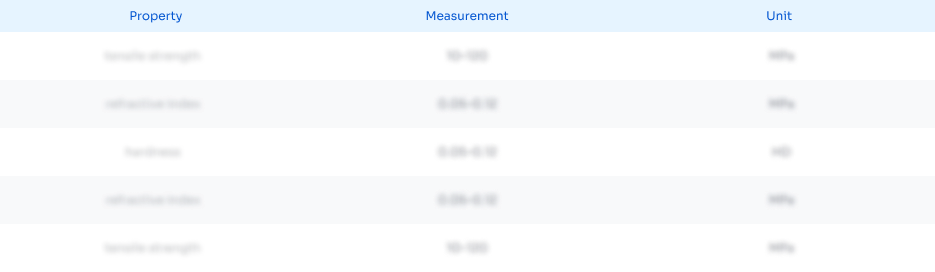
Abstract
Description
Claims
Application Information

- R&D Engineer
- R&D Manager
- IP Professional
- Industry Leading Data Capabilities
- Powerful AI technology
- Patent DNA Extraction
Browse by: Latest US Patents, China's latest patents, Technical Efficacy Thesaurus, Application Domain, Technology Topic, Popular Technical Reports.
© 2024 PatSnap. All rights reserved.Legal|Privacy policy|Modern Slavery Act Transparency Statement|Sitemap|About US| Contact US: help@patsnap.com