Preparation method of p-diethylbenzene catalyst by using high-efficiency alkylation of ethylbenzene
A technology of diethylbenzene catalyst and p-diethylbenzene, which is applied in the direction of catalyst activation/preparation, carbon compound catalyst, physical/chemical process catalyst, etc., and can solve the problem of low ethylbenzene conversion rate, low ethanol utilization rate, and poor repeatability of catalyst regeneration problems such as simplification of impregnation steps, reduction of production costs, and improvement of catalyst stability
- Summary
- Abstract
- Description
- Claims
- Application Information
AI Technical Summary
Problems solved by technology
Method used
Image
Examples
Embodiment 1
[0024] Weigh 133g of nano-hydrogen ZSM-5 molecular sieve with a grain size of 50-100nm, add 120g of pseudoboehmite and 3g of scallop powder, mix well, then add 21.45g of magnesium acetate, 42.24g of phosphoric acid and 117g of dilute nitric acid solution , kneaded and extruded to form a strip, dried at 550°C for 4 hours, and hydrothermally treated at 450°C for 6 hours. The obtained carrier was placed in a cyclohexane solution containing 34.22g of simethicone oil for equal volume impregnation for 6 hours. After drying, it was heated at 550 The p-diethylbenzene catalyst can be obtained by calcination at ℃ for 4 hours, and it is loaded into a fixed bed reactor to evaluate the alkylation reaction of ethylphenylethanol. The reaction temperature is 360°C, the reaction pressure is normal pressure, and the molar ratio of ethylbenzene to ethanol is 2:1, and the space velocity of the liquid phase raw material is 3h -1 , the conversion rate of ethylbenzene is 19.8%, the selectivity to di...
Embodiment 2
[0026] Weigh 266g of nano-hydrogen ZSM-5 molecular sieve, the grain size is 50-150nm, add 240g of pseudoboehmite, 6g of methyl cellulose, mix well, add 38.16g of magnesium nitrate, 45.4g of diammonium hydrogen phosphate and 235g of Dilute nitric acid solution, knead and extrude into strips, dry at 550°C for 4 hours, and hydrothermally treat at 500°C for 4 hours. The obtained carrier is placed in a methylcyclohexane solution containing 65.4g of tetraethyl orthosilicate for equal volume impregnation After drying for 4 hours at 550°C, the p-diethylbenzene catalyst can be obtained. Put it into a fixed-bed reactor to evaluate the alkylation reaction of ethyl styrene. The reaction temperature is 360°C, and the reaction pressure is normal pressure. The molar ratio of benzene to ethylene is 3:1, and the space velocity of the liquid phase raw material is 3h -1 , the conversion rate of ethylbenzene is 18.4%, the selectivity to diethylbenzene is 97.4%, and the reaction time is 323h.
Embodiment 3
[0028] Weigh 133g of nano-hydrogen ZSM-5 molecular sieve with a crystal grain size of 100-200nm, add 110g of pseudoboehmite and 3g of turnip powder, mix well, add 30.32g of magnesium sulfate, 42.58g of ammonium dihydrogen phosphate and 105g of dilute Nitric acid solution, kneaded and extruded to form a strip, dried at 550°C for 6h, and hydrothermally treated at 550°C for 3h, and the obtained carrier was placed in a cyclopentane solution containing 40.85g of diethyl silicone oil for 8h of equal volume. After drying After roasting at 550°C for 6 hours, the p-diethylbenzene catalyst can be obtained, and it is put into a fixed bed reactor to evaluate the alkylation reaction of ethylbenzene and ethanol. The reaction temperature is 380°C, the reaction pressure is normal pressure, and the ratio of ethylbenzene and ethanol The molar ratio is 8:1, and the space velocity of the liquid phase raw material is 8h -1 , the ethylbenzene conversion rate is 12.1%, the p-diethylbenzene selectivi...
PUM
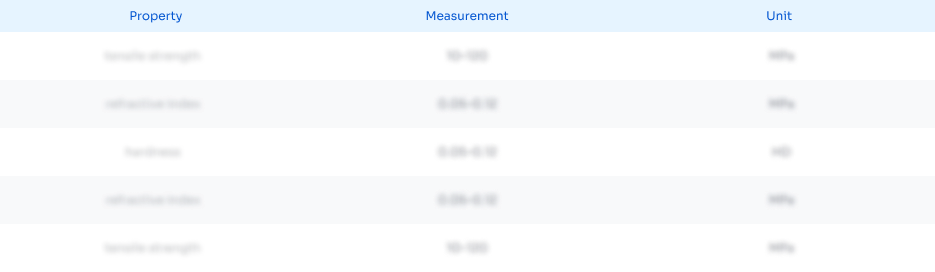
Abstract
Description
Claims
Application Information

- R&D Engineer
- R&D Manager
- IP Professional
- Industry Leading Data Capabilities
- Powerful AI technology
- Patent DNA Extraction
Browse by: Latest US Patents, China's latest patents, Technical Efficacy Thesaurus, Application Domain, Technology Topic, Popular Technical Reports.
© 2024 PatSnap. All rights reserved.Legal|Privacy policy|Modern Slavery Act Transparency Statement|Sitemap|About US| Contact US: help@patsnap.com