Preparation method of carbon material surface boride-modified silicon-based antioxidation coating layer
An anti-oxidation coating and carbon material technology, which is applied in the field of preparation of boride MB2 modified silicon-based anti-oxidation coatings on the surface of carbon materials, can solve the problems of difficult control of phase composition and coating thickness, etc.
- Summary
- Abstract
- Description
- Claims
- Application Information
AI Technical Summary
Problems solved by technology
Method used
Image
Examples
preparation example Construction
[0032] The preparation method of the anti-oxidation coating, first configure MB with controllable content 2 Slurry, where MB 2 In M=Zr, Ta or Hf, brush, dip or spray MB on the surface of carbon material substrate with SiC inner coating 2 The preset layer of the slurry, after the preset layer is obtained, is sintered and combined by ultra-high temperature heat treatment to form a coating.
[0033] The specific steps are:
[0034] Step 1: Ultrasonic cleaning and drying of the carbon material polished by sandpaper with different roughnesses, the carbon material is graphite or C / C composite material;
[0035] Step 2: Prepare the SiC inner coating: uniformly mix Si powder with a mass fraction of 70-90% and C powder with 10-30% and dry it, then put the carbon material treated in step 1 into a graphite crucible and bake it with Wrap the dried powder, then put the graphite crucible with powder and carbon material into the ultra-high temperature heat treatment furnace, pass it into ...
Embodiment 1
[0045] Step 1: Ultrasonic cleaning and drying of graphite after sanding with different roughnesses.
[0046] Step 2: Prepare the SiC inner coating: evenly mix Si powder with a mass fraction of 85% and C powder with 15% and dry it, then put the graphite treated in step 1 into a graphite crucible and use the dried powder Then put the graphite crucible with powder and graphite into the ultra-high temperature heat treatment furnace, pass it into the argon atmosphere for protection, and raise the temperature of the ultra-high temperature heat treatment furnace to 2150 °C at a heating rate of 10 °C / min, keep it for 2 hours, The graphite surface gets a SiC inner coating.
[0047] Step 3: Preparation of TaB 2 -SiC overcoat: TaB 2 Powder (80wt.%), SiC powder (5wt.%), Si powder (10wt.%) and C powder (5wt.%) are evenly mixed and dried, then add a certain amount of silica sol (the volume of silica sol is mixed with The mass ratio of the powder is 2.5ml / g) and placed in a ball mill for ...
Embodiment 2
[0051] Step 1: Ultrasonic cleaning and drying of graphite after sanding with different roughnesses.
[0052] Step 2: Prepare the SiC inner coating: evenly mix Si powder with a mass fraction of 75% and C powder with 25% and dry it, then put the graphite treated in step 1 into a graphite crucible and use the dried powder Then put the graphite crucible with powder and graphite into the ultra-high temperature heat treatment furnace, pass it into the argon atmosphere for protection, and raise the temperature of the ultra-high temperature heat treatment furnace to 2050 °C at a heating rate of 15 °C / min, keep it for 4 hours, The graphite surface gets a SiC inner coating.
[0053] Step 3: Preparation of HfB 2 -SiC overcoat: HfB 2 Powder (60wt.%), SiC powder (10wt.%), Si powder (20wt.%) and C powder (10wt.%) are evenly mixed and dried, then add a certain amount of silica sol (the volume of silica sol is mixed with The ratio of powder mass is 2ml / g) and placed in a ball mill to mix e...
PUM
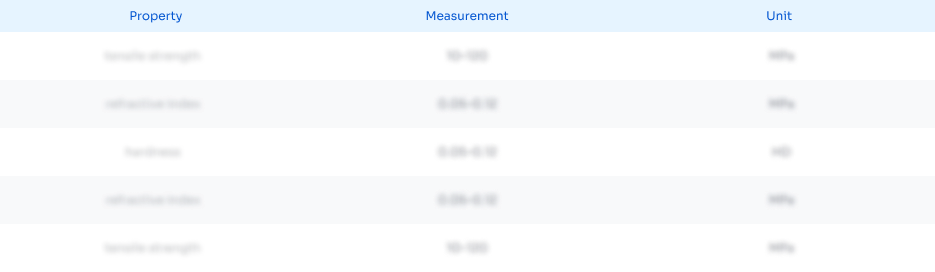
Abstract
Description
Claims
Application Information

- R&D Engineer
- R&D Manager
- IP Professional
- Industry Leading Data Capabilities
- Powerful AI technology
- Patent DNA Extraction
Browse by: Latest US Patents, China's latest patents, Technical Efficacy Thesaurus, Application Domain, Technology Topic, Popular Technical Reports.
© 2024 PatSnap. All rights reserved.Legal|Privacy policy|Modern Slavery Act Transparency Statement|Sitemap|About US| Contact US: help@patsnap.com