Preparation method of high toughness metal ceramic
A cermet, high toughness technology, applied in chemical instruments and methods, crystal growth, self-solids, etc., can solve the problems of low fracture toughness, unsatisfactory toughening effect, poor compatibility between toughening filler and technical matrix, etc. , to achieve the effect of improving toughening effect and improving compatibility
- Summary
- Abstract
- Description
- Claims
- Application Information
AI Technical Summary
Problems solved by technology
Method used
Examples
example 1
[0025] Mix the rice husk and 30% sodium hydroxide solution with a mass fraction of 1:3, heat and boil for 30 minutes, filter to obtain the filter residue after boiling, rinse 3 times with clean water, and then filter the filter residue with a mass fraction of 35%. Soak in sodium silicate solution for 10 hours to obtain the soaked filter residue; mix the soaked filter residue with 1mol / L hydrochloric acid at a mass ratio of 1:5, put it into an ultrasonic oscillator, and treat it with ultrasonic oscillation at a frequency of 30kHz for 20min, and the ultrasonic oscillation treatment is completed Afterwards, filter and separate to obtain the oscillating filter residue; put the oscillating filter residue into a carbonization furnace, and keep carbonization at a temperature of 700 °C for 1 hour under nitrogen protection to obtain a carbonized filter residue, and then put the carbonized filter residue into a vacuum sintering furnace, and use 50 mL / Inject argon gas into the furnace at...
example 2
[0027]According to the mass ratio of 1:3, the rice husk and the 30% sodium hydroxide solution were mixed, heated and boiled for 35 minutes, filtered to obtain the filter residue after boiling, rinsed with water for 4 times, and then the filter residue was mixed with a mass fraction of 35%. Soak in sodium silicate solution for 11 hours to obtain the soaked filter residue; mix the soaked filter residue with 1mol / L hydrochloric acid at a mass ratio of 1:5, put it into an ultrasonic oscillator, and treat it with ultrasonic oscillation at a frequency of 35kHz for 25min, and the ultrasonic oscillation treatment is completed Finally, filter and separate to obtain the oscillating filter residue; put the oscillating filter residue in a carbonization furnace, and keep carbonized at a temperature of 750°C for 1 hour under nitrogen protection to obtain a carbonized filter residue, and then put the carbonized filter residue into a vacuum sintering furnace, and use 50mL / Pass argon gas into ...
example 3
[0029] According to the mass ratio of 1:3, rice husk and 30% sodium hydroxide solution were mixed, heated and boiled for 40 minutes, filtered to obtain filter residue after boiling, rinsed with water for 5 times, and then filtered with 35% mass fraction Soak in sodium silicate solution for 12 hours to obtain the soaked filter residue; mix the soaked filter residue with 1mol / L hydrochloric acid at a mass ratio of 1:5, put it into an ultrasonic oscillator, and treat it with ultrasonic oscillation at a frequency of 40kHz for 30min, and the ultrasonic oscillation treatment is completed Finally, filter and separate to obtain the oscillating filter residue; put the oscillating filter residue in a carbonization furnace, and keep carbonization at a temperature of 800°C for 2 hours under the protection of nitrogen to obtain a carbonized filter residue, and then put the carbonized filter residue into a vacuum sintering furnace at a rate of 50 mL / Pass argon gas into the furnace at a rate...
PUM
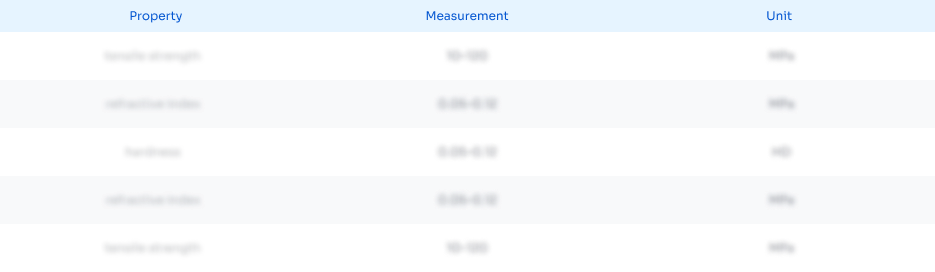
Abstract
Description
Claims
Application Information

- R&D
- Intellectual Property
- Life Sciences
- Materials
- Tech Scout
- Unparalleled Data Quality
- Higher Quality Content
- 60% Fewer Hallucinations
Browse by: Latest US Patents, China's latest patents, Technical Efficacy Thesaurus, Application Domain, Technology Topic, Popular Technical Reports.
© 2025 PatSnap. All rights reserved.Legal|Privacy policy|Modern Slavery Act Transparency Statement|Sitemap|About US| Contact US: help@patsnap.com