Electrode foil corrosion method of low-contact resistance low-voltage aluminium electrolytic capacitor
A technology of aluminum electrolytic capacitors and low contact resistance, applied in electrolytic capacitors, capacitors, circuits, etc., can solve the problems of high electrode foil contact resistance, poor cleaning effect, and large amount of corrosion in the corrosion layer
- Summary
- Abstract
- Description
- Claims
- Application Information
AI Technical Summary
Problems solved by technology
Method used
Image
Examples
Embodiment 1
[0023] (a) Place the low-voltage anode foil of the electrolytic capacitor in 0.01wt% sodium hydroxide solution and soak it for 3 minutes at a temperature of 40°C;
[0024] (b) The anode foil obtained in step (a) is treated with 6wt% hydrochloric acid and 0.1wt% sulfuric acid at a temperature of 30°C and a current density of 0.3A / cm² for 20 seconds;
[0025] (c) The anode foil obtained in step (b) is treated with 6wt% hydrochloric acid and 0.1wt% sulfuric acid at a temperature of 30°C for 20 seconds;
[0026] (d) Wash the anode foil obtained in step (c) with tap water at a temperature of 40°C for 30 seconds;
[0027] (e) Repeat steps (b), (c), (d) 4 times;
[0028] (f) The anode foil obtained in step (e) is subjected to hole expansion corrosion in 6wt% hydrochloric acid, 0.1wt% sulfuric acid, 0.01wt% phosphoric acid corrosion solution, the current density is 0.1A / cm², the temperature is 30°C, and the sine wave Change the frequency of 5~35Hz from low to high for low frequency ...
Embodiment 2
[0036] (a) Place the low-voltage anode light foil of the electrolytic capacitor in 0.5wt% sodium hydroxide solution and soak at 50°C for 2 minutes;
[0037] (b) The anode foil obtained in step (a) is treated with 8wt% hydrochloric acid and 0.3wt% sulfuric acid for 40 seconds at a temperature of 40°C and a current density of 0.5A / cm²;
[0038] (c) The anode foil obtained in step (b) is treated with 8wt% hydrochloric acid and 0.3wt% sulfuric acid at a temperature of 40°C for 40 seconds;
[0039] (d) Wash the anode foil obtained in step (c) with tap water at a temperature of 45°C for 40 seconds;
[0040] (e) Repeat steps (b), (c), (d) 4 times;
[0041] (f) The anode foil obtained in step (e) is subjected to hole expansion corrosion in 8wt% hydrochloric acid, 0.3wt% sulfuric acid, 0.1wt% phosphoric acid corrosion solution, the current density is 0.3A / cm², the temperature is 35°C, according to the sine wave Change the frequency of 5~35Hz from low to high for low frequency corrosi...
Embodiment 3
[0049] (a) Place the low-voltage anode foil of the electrolytic capacitor in a 2wt% sodium hydroxide solution and soak for 1 minute at a temperature of 55°C;
[0050] (b) The anode foil obtained in step (a) is treated with 10wt% hydrochloric acid and 0.5wt% sulfuric acid at a temperature of 45°C and a current density of 0.7A / cm² for 60 seconds;
[0051] (c) The anode foil obtained in step (b) is treated with 10wt% hydrochloric acid and 0.5wt% sulfuric acid at a temperature of 45°C for 60 seconds;
[0052] (d) Wash the anode foil obtained in step (c) with tap water at a temperature of 50°C for 60 seconds;
[0053] (e) Repeat steps (b), (c), (d) 4 times;
[0054] (f) The anode foil obtained in step (e) is subjected to hole expansion corrosion in 10wt% hydrochloric acid, 0.5wt% sulfuric acid, 0.5wt% phosphoric acid corrosion solution, the current density is 0.4A / cm², the temperature is 40°C, and the sine wave Change the frequency of 5~35Hz from low to high for low frequency cor...
PUM
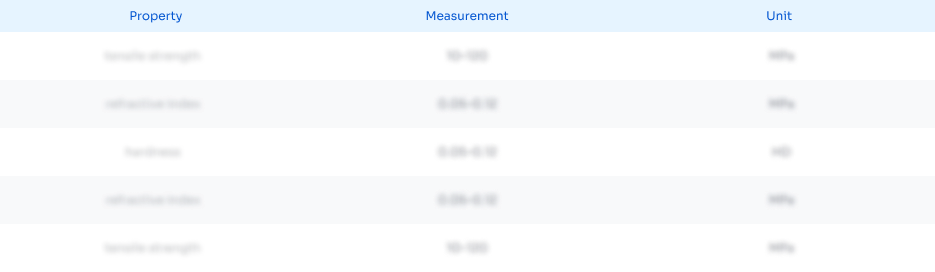
Abstract
Description
Claims
Application Information

- R&D
- Intellectual Property
- Life Sciences
- Materials
- Tech Scout
- Unparalleled Data Quality
- Higher Quality Content
- 60% Fewer Hallucinations
Browse by: Latest US Patents, China's latest patents, Technical Efficacy Thesaurus, Application Domain, Technology Topic, Popular Technical Reports.
© 2025 PatSnap. All rights reserved.Legal|Privacy policy|Modern Slavery Act Transparency Statement|Sitemap|About US| Contact US: help@patsnap.com