Flame-retardant adhesive and preparation method and application thereof
A technology of adhesives and flame-retardant adhesives, which is applied in the direction of adhesives, adhesive additives, adhesive types, etc., and can solve problems such as failure to meet strong bonding requirements, high curing temperature, and low cohesive strength of adhesives
- Summary
- Abstract
- Description
- Claims
- Application Information
AI Technical Summary
Problems solved by technology
Method used
Image
Examples
Embodiment approach
[0096] According to a preferred embodiment of the present invention, the weight ratio of water to formaldehyde is (0.9-2.4):1.
[0097] In the present invention, the form of the formaldehyde raw material is not limited, solid formaldehyde can be used, liquid formaldehyde can also be used, or the two can be used in combination, wherein, when using liquid formaldehyde, the consumption of water can be reduced as appropriate.
[0098] According to a preferred embodiment of the present invention, in step a, the temperature is raised to 60-120°C at a rate of 2-3°C / min, and the temperature is kept constant for 10-30min.
[0099] In a further preferred embodiment, the temperature is raised to 90-110° C. at a rate of 2-3° C. / min, and the temperature is kept constant for 15-25 minutes.
[0100] In a further preferred embodiment, the temperature is raised to 80-100° C. at a rate of 2-3° C. / min, and the temperature is kept constant for 20 minutes.
[0101] According to a preferred embodi...
Embodiment 1
[0169] (1) Preparation of phenolic resin
[0170] Weigh 1000g of solid formaldehyde and 2000g of demineralized water into the reaction kettle, turn on the stirring and condenser, raise the temperature of the material from room temperature to 85°C at a rate of 2-3°C / min, keep the temperature constant for 20 minutes, add 3600g of phenol, and use The hydrochloric acid solution with a mass concentration of 35% adjusts the pH of the material to 2.0, continues the constant temperature reaction for 4 hours, then vacuumizes and dehydrates the material, cools and discharges the material, pulverizes it and seals it for storage.
[0171] (2) Preparation of phenolic resin composition
[0172] Weigh 2000g of phenolic resin and 1200g of ethyl acetate into the reaction kettle, fill with nitrogen to remove the air, seal and stir until the phenolic resin is completely dissolved, then add 2000g of aluminum hydroxide, stir for 1 hour to mix the materials evenly, and pack the obtained product int...
Embodiment 2
[0178] (1) Preparation of phenolic resin
[0179] Weigh 1500g of solid formaldehyde and 2530g of demineralized water into the reaction kettle, turn on the stirring and condenser, raise the temperature of the material from room temperature to 95°C at a rate of 2-3°C / min, keep the temperature for 20 minutes, then add 5800g of phenol, Adjust the pH to 2.5 with 45% acetic acid solution, react at a constant temperature for 5 hours, then vacuumize and dehydrate the material, cool and discharge, pulverize and store in a sealed container.
[0180] (2) Preparation of phenolic resin composition
[0181] Weigh 2000g of phenolic resin and 1000g of dichloromethane into the reaction kettle, fill with nitrogen to remove the air, seal and stir until the phenolic resin is completely dissolved, then add 1800g of magnesium hydroxide, stir for 1.5 hours to mix the materials evenly, and distribute the obtained product in an airtight container. Store in a container filled with nitrogen and sealed....
PUM
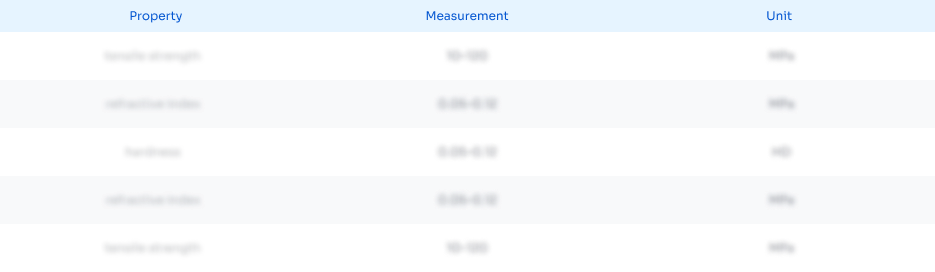
Abstract
Description
Claims
Application Information

- R&D Engineer
- R&D Manager
- IP Professional
- Industry Leading Data Capabilities
- Powerful AI technology
- Patent DNA Extraction
Browse by: Latest US Patents, China's latest patents, Technical Efficacy Thesaurus, Application Domain, Technology Topic, Popular Technical Reports.
© 2024 PatSnap. All rights reserved.Legal|Privacy policy|Modern Slavery Act Transparency Statement|Sitemap|About US| Contact US: help@patsnap.com