Slurry containing natural stone powder as well as preparation method and application of slurry
A natural stone powder and slurry technology, which is applied in the field of slurry containing natural stone powder and its preparation, can solve the problems of low smoothness, electrostatic induction, and low fastness, and achieve the advantages of simple preparation method, indoor temperature adjustment, and low production cost Effect
- Summary
- Abstract
- Description
- Claims
- Application Information
AI Technical Summary
Problems solved by technology
Method used
Examples
preparation example Construction
[0020] Among them, the preparation method of the modified acrylic resin includes the following steps: under the state of stirring and blowing nitrogen gas, adding an inorganic dispersant to the water and raising the temperature to 70-75°C; ~18h, then lower the temperature to 25~30°C to obtain modified acrylic resin; wherein, the mass ratio of water, inorganic dispersant, raw material monomer and initiator is (180~200):(0.9~1.1):(90~ 95): 1, the stirring rate is 80~100r / min; the inorganic dispersant is selected from one or more of calcium carbonate, aluminum oxide, magnesium hydroxide, basic magnesium carbonate and calcium hydroxyphosphate; the raw material monomer includes The first monomer, the second monomer and the third monomer, the mass ratio of the first monomer, the second monomer and the third monomer is (10~15):(20~30):1; wherein, the first One monomer is methyl methacrylate and / or methyl acrylate, the second monomer is ethyl acrylate and / or ethyl methacrylate, and th...
Embodiment 1
[0027] This embodiment provides a slurry containing natural stone powder. The raw material components include: 40 parts by weight of natural stone powder, 30 parts by weight of viscosifying emulsion, 4 parts by weight of silica sol, 45 parts by weight of modified acrylic resin and 5 parts by weight of triisopropanolamine;
[0028]Wherein, the preparation method of the modified acrylic resin comprises the following steps: under the stirring rate of 80r / min and the state of nitrogen flow, add the inorganic dispersant magnesium hydroxide in the water and heat up to 70°C; then add the raw material monomer and the initiator Oxidize dibenzoyl, mix evenly, react at constant temperature for 15 hours, and then lower the temperature to 25°C to obtain a modified acrylic resin; wherein, the mass ratio of water, inorganic dispersant, raw material monomer and initiator is 180:0.9:90:1 Raw material monomer comprises the first monomer methyl acrylate, the second monomer ethyl methacrylate and...
Embodiment 2
[0033] This embodiment provides a slurry containing natural stone powder. The raw material components include: 50 parts by weight of natural stone powder, 20 parts by weight of viscosifying emulsion, 6 parts by weight of silica sol, 35 parts by weight of modified acrylic resin and 10 parts by weight of triisopropanolamine;
[0034] Wherein, the preparation method of the modified acrylic resin comprises the following steps: under the stirring speed of 100r / min and the state of blowing nitrogen, add the inorganic dispersant magnesium hydroxide in water and raise the temperature to 75°C; then add the raw material monomer and the initiator Oxidize dibenzoyl, mix uniformly, react at constant temperature for 18 hours, and then lower the temperature to 30°C to obtain a modified acrylic resin; wherein, the mass ratio of water, inorganic dispersant, raw material monomer and initiator is 200:1.1:95:1 Raw material monomer comprises the first monomer methyl acrylate, the second monomer et...
PUM
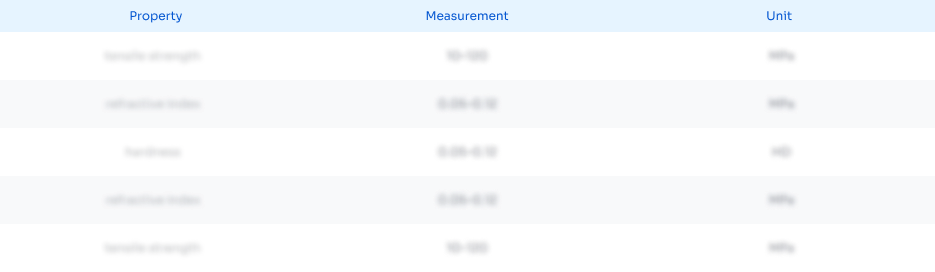
Abstract
Description
Claims
Application Information

- Generate Ideas
- Intellectual Property
- Life Sciences
- Materials
- Tech Scout
- Unparalleled Data Quality
- Higher Quality Content
- 60% Fewer Hallucinations
Browse by: Latest US Patents, China's latest patents, Technical Efficacy Thesaurus, Application Domain, Technology Topic, Popular Technical Reports.
© 2025 PatSnap. All rights reserved.Legal|Privacy policy|Modern Slavery Act Transparency Statement|Sitemap|About US| Contact US: help@patsnap.com