Application of synthetic calcium carbonate as high paper filler and preparation method of high paper filler
A papermaking filler, calcium silicate technology, applied in the field of papermaking, can solve the problems of short mixing time of filler and fiber, unable to meet the requirements of paper index, unable to add traditional filler, etc., to achieve good suspension, improve opacity, improve non-toxicity The effect of transparency
- Summary
- Abstract
- Description
- Claims
- Application Information
AI Technical Summary
Problems solved by technology
Method used
Image
Examples
preparation example Construction
[0046] Preparation of synthetic calcium silicate powder:
[0047] Adopt liquid phase dynamic hydrothermal synthesis method, comprise the following steps:
[0048] A, raw material preparation: prepare lime emulsion and sodium silicate solution, described lime emulsion is obtained after digesting and diluting active quicklime by calcining limestone, wherein the concentration of lime emulsion is controlled so that the CaO concentration is 140-220g / L, and the silicon The sodium silicate solution is obtained by diluting high-purity quartz sand with alkali, and the obtained sodium silicate solution is controlled to contain SiO 2 35-140g / L;
[0049] B. Hydrothermal synthesis of calcium silicate: control of CaO / SiO in sodium silicate solution and lime emulsion 2 The molar ratio is 0.95-1.05, the water-solid mass ratio (5-15): 1, mix evenly, heat up to 75-100°C, control the temperature rise and reaction time to 1-2.5h, and the stirring speed is 100-400rpm;
[0050] C. Preparation o...
Embodiment 1
[0055] The plant pulp board adopts bleached kraft softwood pulp board, and the mass ratio of bleached kraft softwood pulp board to synthetic calcium silicate powder filler is controlled to be 50:50.
[0056] Take the bleached kraft softwood pulp board and disintegrate it with a hydraulic pulper, send it to the pulp storage tank before knocking, and adjust the mass fraction concentration of the pulp to 6.0%; beat it with a disc refiner to a Canadian standard freeness of 275mL Finally, adjust the slurry concentration to a mass fraction of 4.0%, and send it to the slurry storage tank after knocking;
[0057] The synthetic calcium silicate powder is made into an emulsion in water under the action of a high-speed disperser, and the synthetic calcium silicate powder is prepared into a calcium silicate slurry with a concentration of 5%-15%. After passing through the sieving equipment, the synthetic calcium silicate powder filler is driven into the pulp storage tank after beating, and...
Embodiment 2
[0062] The plant pulp board adopts bleached kraft softwood pulp board and bleached hardwood pulp board, and the mass ratio of plant pulp board to synthetic calcium carbonate powder filler is 48:52, of which bleached kraft softwood pulp board and bleached hardwood pulp board The mass ratio of the plates was 15:33.
[0063] Disintegrate and disperse the bleached kraft softwood pulp board and the bleached hardwood pulp board with a hydraulic pulper respectively, and send them to two pulp storage tanks before knocking, and adjust the mass fraction concentration of the pulp to 4.5%; After beating the above two kinds of wood pulp to Canadian standard freeness of 265mL (softwood pulp) and 300mL (hardwood pulp), adjust the pulp concentration to a mass fraction of 4.0%, and send it to the pulp storage tank after beating;
[0064] The synthetic calcium silicate powder is made into an emulsified liquid in water under the action of a high-speed disperser. After passing through the sieving...
PUM
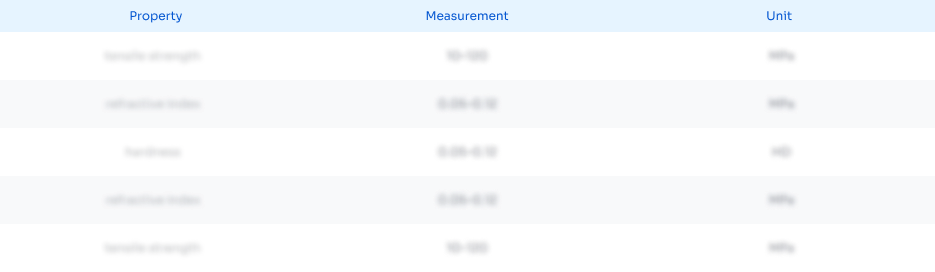
Abstract
Description
Claims
Application Information

- R&D
- Intellectual Property
- Life Sciences
- Materials
- Tech Scout
- Unparalleled Data Quality
- Higher Quality Content
- 60% Fewer Hallucinations
Browse by: Latest US Patents, China's latest patents, Technical Efficacy Thesaurus, Application Domain, Technology Topic, Popular Technical Reports.
© 2025 PatSnap. All rights reserved.Legal|Privacy policy|Modern Slavery Act Transparency Statement|Sitemap|About US| Contact US: help@patsnap.com