Preparation method and application of chloroprene-rubber-adding building material
A technology of neoprene and building materials, which is applied in the field of building materials, can solve problems affecting the service life of structural durability projects, deterioration of concrete structures, and low tensile strength, and is suitable for large-scale industrial applications, cheap raw materials, and practical strong effect
- Summary
- Abstract
- Description
- Claims
- Application Information
AI Technical Summary
Problems solved by technology
Method used
Examples
Embodiment 1
[0026] (1) Put 20 parts of Portland cement, 15 parts of perlite powder, and 8 parts of sepiolite into the ball mill, add stainless steel grinding balls, the ball-to-material ratio of the ball mill is 15:1, adjust the speed of the ball mill to 80r / min, and mill for 4 hours , collect the powder and pass through a 120-mesh sieve to obtain a mixed powder;
[0027] (2) Put 22 parts of carboxyl polyester resin in the reaction kettle, raise the temperature to 150°C, treat it for 2h under the condition of vacuum degree of -0.08Mpa, then raise the temperature to 175°C, add 6 parts of tyloxapol, polyethylene glycol 3 parts of ethylene glycol ester, 2 parts of methoxypolyethylene glycol, react for 1 hour under normal pressure, wash the reaction product with 3mol / L dilute hydrochloric acid for 2-3 times, and then wash with deionized water until neutral , to obtain modified carboxyl polyester resin;
[0028] (3) Mix 6 parts of polyacrylamide, 3 parts of cellulose acetate phthalate, and 1 ...
Embodiment 2
[0035] (1) Add 23 parts of Portland cement, 17 parts of perlite powder and 10 parts of sepiolite into the ball mill, add stainless steel grinding balls, the ball-to-material ratio of the ball mill is 15:1, adjust the speed of the ball mill to 90r / min, and mill for 5 hours , collect the powder and pass through a 120-mesh sieve to obtain a mixed powder;
[0036] (2) Put 25 parts of carboxyl polyester resin in the reaction kettle, raise the temperature to 150°C, treat it for 2.5h under the condition of vacuum degree of -0.08Mpa, then raise the temperature to 175°C, add 8 parts of tyloxapol, polyhexyl 4 parts of ethylene glycol diate and 3 parts of methoxypolyethylene glycol were reacted at normal pressure for 1 h, and the reaction product was washed 2-3 times with 3 mol / L dilute hydrochloric acid, and then washed with deionized water to medium property, to obtain modified carboxyl polyester resin;
[0037] (3) Mix 10 parts of polyacrylamide, 6 parts of cellulose acetate phthalat...
Embodiment 3
[0044] (1) Put 25 parts of Portland cement, 20 parts of perlite powder, and 12 parts of sepiolite into the ball mill, add stainless steel grinding balls, the ball-to-material ratio of the ball mill is 15:1, adjust the speed of the ball mill to 100r / min, and mill for 6 hours , collect the powder and pass through a 120-mesh sieve to obtain a mixed powder;
[0045] (2) Put 28 parts of carboxyl polyester resin in the reaction kettle, raise the temperature to 150°C, treat it for 3 hours under the condition of vacuum degree of -0.08Mpa, then raise the temperature to 175°C, add 10 parts of tyloxapol, polyhexyl Acetate ethylene glycol 5 parts, methoxypolyethylene glycol 4 parts, react under normal pressure for 1h, wash the reaction product with 3mol / L dilute hydrochloric acid for 2-3 times, and then wash with deionized water until neutral , to obtain modified carboxyl polyester resin;
[0046] (3) Mix 15 parts of polyacrylamide, 9 parts of cellulose acetate phthalate, and 3 parts of ...
PUM
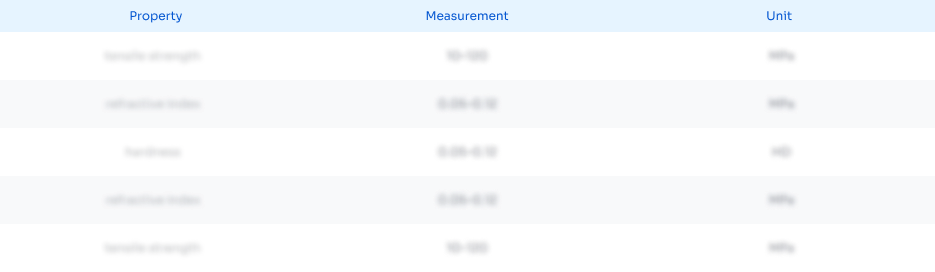
Abstract
Description
Claims
Application Information

- Generate Ideas
- Intellectual Property
- Life Sciences
- Materials
- Tech Scout
- Unparalleled Data Quality
- Higher Quality Content
- 60% Fewer Hallucinations
Browse by: Latest US Patents, China's latest patents, Technical Efficacy Thesaurus, Application Domain, Technology Topic, Popular Technical Reports.
© 2025 PatSnap. All rights reserved.Legal|Privacy policy|Modern Slavery Act Transparency Statement|Sitemap|About US| Contact US: help@patsnap.com