Preparation method for solid catalyst for ozone heterogeneous oxidization
A heterogeneous oxidation, solid catalyst technology, applied in the direction of catalyst activation/preparation, physical/chemical process catalyst, metal/metal oxide/metal hydroxide catalyst, etc., can solve the problem of poor toxicity resistance, easy loss of catalytic activity, Problems such as low catalyst adsorption
- Summary
- Abstract
- Description
- Claims
- Application Information
AI Technical Summary
Problems solved by technology
Method used
Examples
Embodiment 1
[0007] Embodiment 1:1.35g lithium hypochlorite, 1.65g bis(acetylacetonate) beryllium, 140ml deionized water, join volume and be that in the sealable reactor of 500ml, stir and mix evenly, the weight concentration of this aqueous solution is 2.1%, times Lithium chlorate: bis(acetylacetonate) beryllium weight ratio=1:1.2; add deionized water to wash to neutral, dry at 103°C to remove moisture, and then sieve 2.75g of perlite with -200 mesh to +400 mesh standard sieve , 3.75g albite, 4.75g montmorillonite, 5.75g sylvite, 6.75g amazonite, 7.75g lithium limestone, lithium hypochlorite and bis(acetylacetonate) beryllium weight (3g): porous material Weight (31.5g) = 1:10.5, heat up to 36°C, continue to stir for 3.2h, filter, dry at 103°C and obtain 31g of pore-enlarging modified carrier; in a 500ml ultrasonic reactor, put the pore-enlarging modified carrier 31g, then add 3.25g nonylphenol base diquaternary ammonium salt and be dissolved in the aqueous solution of 100ml deionized wate...
Embodiment 2
[0008] Embodiment 2: 0.24g lithium hypochlorite, 0.36g bis(acetylacetonate) beryllium, 10ml deionized water, join volume and be that in the sealable reactor of 100ml, stir and mix evenly, the weight concentration of this aqueous solution is 5.7%, times Lithium chlorate: the weight ratio of bis(acetylacetonate) beryllium=1:1.5; add deionized water to wash to neutral, dry at 103°C to remove moisture, and then sieve 1.45g perlite of -200 mesh to +400 mesh standard sieve , 1.65g albite, 1.85g montmorillonite, 2.05g sylvite, 2.25g amazonite, 2.45g lithium limestone, lithium hypochlorite and bis(acetylacetonate) beryllium weight (0.6g): Porous material The weight (11.7g)=1:19.5, heat up to 48°C, continue to stir and react for 5.8h, filter, dry at 105°C and obtain 11.5g of pore-enlarging modified carrier; in a 100ml ultrasonic reactor, put the pore-enlarging modified Sexual carrier 11.5g, add the aqueous solution that 2.2g nonylphenol base biquaternary ammonium salt is dissolved in 2...
PUM
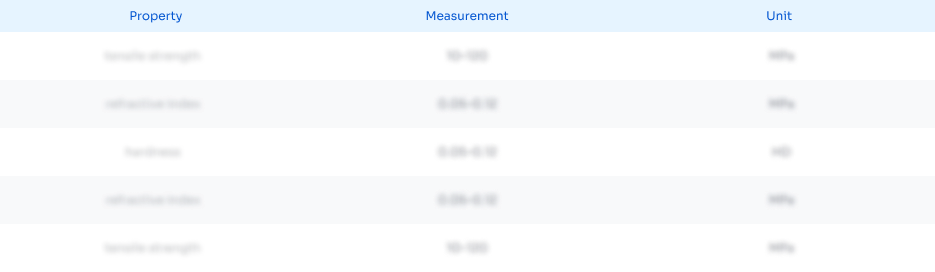
Abstract
Description
Claims
Application Information

- R&D
- Intellectual Property
- Life Sciences
- Materials
- Tech Scout
- Unparalleled Data Quality
- Higher Quality Content
- 60% Fewer Hallucinations
Browse by: Latest US Patents, China's latest patents, Technical Efficacy Thesaurus, Application Domain, Technology Topic, Popular Technical Reports.
© 2025 PatSnap. All rights reserved.Legal|Privacy policy|Modern Slavery Act Transparency Statement|Sitemap|About US| Contact US: help@patsnap.com