A method for preparing aluminum nitride
A technology of aluminum nitride and alumina, which is applied in the field of material science, can solve the problems of a large amount of nitrogen-containing waste gas or other waste gas, and achieve the effects of shortening the carbon removal steps, shortening the reaction time, and facilitating industrialization
- Summary
- Abstract
- Description
- Claims
- Application Information
AI Technical Summary
Problems solved by technology
Method used
Examples
Embodiment 1
[0032] Embodiment 1: the preparation method of aluminum nitride powder of this embodiment, concrete steps are as follows:
[0033] The first stage, carbon thermal reduction of alumina under vacuum to prepare solid products mainly of aluminum carbide and aluminum oxide carbon
[0034] (1) Mix alumina powder and graphite powder at a mass ratio of 2.8:1 to obtain mixed raw materials;
[0035] (2) Put the mixed raw materials of step (1) in the reaction furnace, evacuate the reaction furnace until the pressure is lower than 5Pa, raise the temperature to 1300°C, and keep the temperature for 50 minutes, and continue to evacuate during the heat preservation process;
[0036] (3) After the heat preservation is completed, start to cool down. After the temperature drops to room temperature, stop vacuuming, open the reaction furnace, and take out the reaction product, which is mainly composed of aluminum carbide and aluminum carbon oxide;
[0037] The second stage, nitriding to prepare a...
Embodiment 2
[0041] Embodiment 2: the preparation method of aluminum nitride powder of this embodiment, concrete steps are as follows:
[0042] The first stage, carbon thermal reduction of alumina under vacuum to prepare solid products mainly of aluminum carbide and aluminum oxide carbon
[0043] (1) Mix alumina powder and graphite powder at a mass ratio of 2.8:1 to obtain mixed raw materials;
[0044] (2) Put the mixed raw materials in step (1) in the reaction furnace, evacuate the reaction furnace until the pressure is lower than 3Pa, raise the temperature to 1400°C, keep the temperature for 40 minutes, and continue to evacuate during the heat preservation process;
[0045] (3) After the heat preservation is completed, start to cool down. After the temperature drops to room temperature, stop vacuuming, open the vacuum furnace, and take out the reaction product, which is mainly composed of aluminum carbide and aluminum carbon oxide;
[0046] The second stage, nitriding to prepare aluminu...
Embodiment 3
[0050] Embodiment 3: the preparation method of aluminum nitride powder of this embodiment, concrete steps are as follows:
[0051] The first stage, carbon thermal reduction of alumina under vacuum to prepare solid products mainly of aluminum carbide and aluminum oxide carbon
[0052] (1) Mix alumina powder and carbon black at a mass ratio of 2.9:1 and mix them evenly to obtain mixed raw materials;
[0053] (2) Put the mixed raw materials in step (1) in the reaction furnace, evacuate the reaction furnace until the pressure is lower than 1Pa, raise the temperature to 1500°C, keep the temperature for 30 minutes, and continue to evacuate during the heat preservation process;
[0054] (3) After the heat preservation is completed, start to cool down. After the temperature drops to room temperature, stop vacuuming, open the reaction furnace, and take out the reaction product, which is mainly composed of aluminum carbide and aluminum carbon oxide;
[0055] The second stage, nitriding...
PUM
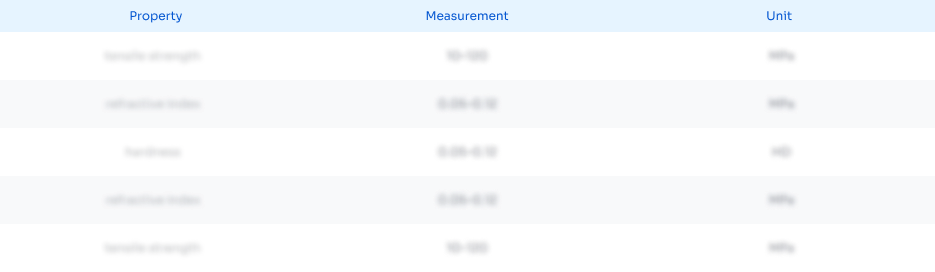
Abstract
Description
Claims
Application Information

- Generate Ideas
- Intellectual Property
- Life Sciences
- Materials
- Tech Scout
- Unparalleled Data Quality
- Higher Quality Content
- 60% Fewer Hallucinations
Browse by: Latest US Patents, China's latest patents, Technical Efficacy Thesaurus, Application Domain, Technology Topic, Popular Technical Reports.
© 2025 PatSnap. All rights reserved.Legal|Privacy policy|Modern Slavery Act Transparency Statement|Sitemap|About US| Contact US: help@patsnap.com