Nickel-based superalloy electroslag remelting slag system
A nickel-based superalloy, electroslag remelting technology, applied in the field of nickel-based superalloy electroslag remelting slag system, can solve the problems of increasing the number of oxide inclusions, difficult to accurately control alloy composition, affecting the quality and processing performance of steel ingots, etc. , to achieve the effects of good anti-water absorption and air absorption, easy processing and deformation, and enhanced machinability
- Summary
- Abstract
- Description
- Claims
- Application Information
AI Technical Summary
Problems solved by technology
Method used
Image
Examples
Embodiment 1
[0026] 1) Preparation of self-fusing electrode rod
[0027] Take the components in Table 1, with a total weight of 31kg, and prepare a GH3536 nickel-based superalloy self-fusing electrode rod with a diameter of φ100mm by vacuum induction melting and casting.
[0028] Table 1 Composition ratio wt% of GH3536 superalloy
[0029] C Si mn Mo Cr W co Fe Ni 0.098 0.15 0.17 8.74 21.20 0.69 1.56 18.43 margin
[0030] 2) Configure electroslag remelting slag system
[0031] Weigh CaF 2 4.20kg, Al 2 o 3 0.96kg, MgO0.72kg, SiO 2 0.12kg, of which the impurity content is less than 1.0%, and the impurity is unavoidable impurity, including MnO, TiO 2 , CaO, FeO, where MnO≤0.2%, TiO 2 ≤0.2%, CaO≤0.1%, FeO≤0.3%, configured as an electroslag heavy melting slag system with a total weight of 6kg.
[0032] 3) Electroslag remelting
[0033] Mix the prepared electroslag remelting slag evenly, bake it at 800°C for 4 hours, use a graphite electrode rod to...
Embodiment 2
[0037] 1) Preparation of self-fusing electrode rod
[0038] Take the components in Table 2, with a total weight of 31kg, and prepare a GH3536 superalloy self-fusing electrode rod with a diameter of φ100mm by vacuum induction melting and casting.
[0039] Table 2 GH3536 superalloy composition ratio wt%
[0040] C Si mn Mo Cr W co Fe Ni 0.098 0.15 0.17 8.74 21.20 0.69 1.56 18.43 margin
[0041] 2) Configure electroslag remelting slag system
[0042] Weigh CaF 2 4.44kg, Al 2 o3 0.90kg, MgO0.6kg, SiO 2 0.06kg, of which the impurity content is less than 1.0%, and the impurity is unavoidable impurity, including MnO, TiO 2 , CaO, FeO, where MnO≤0.2%, TiO 2 ≤0.2%, CaO≤0.1%, FeO≤0.3%, configured as an electroslag heavy melting slag system with a total weight of 6kg.
[0043] 3) Electroslag remelting
[0044] Mix the prepared electroslag remelting slag evenly, bake it at 800°C for 4 hours, use a graphite electrode rod to melt the slag, and...
Embodiment 3
[0048] 1) Preparation of self-fusing electrode rod
[0049] Take the components in Table 3, with a total weight of 31kg, and prepare a GH3536 superalloy self-fusing electrode rod with a diameter of φ100mm by vacuum induction melting and casting.
[0050] Table 3 GH3536 superalloy composition ratio wt%
[0051] C Si mn Mo Cr W co Fe Ni 0.098 0.15 0.17 8.74 21.20 0.69 1.56 18.43 margin
[0052] 2) Configure electroslag remelting slag system
[0053] Weigh CaF 2 4.32kg, Al 2 o 3 1.08kg, MgO 0.6kg, SiO 2 0kg, the impurity content is less than 1.0%, and the impurity is unavoidable impurity, including MnO, TiO 2 , CaO, FeO, where MnO≤0.2%, TiO 2 ≤0.2%, CaO≤0.1%, FeO≤0.3%, configured as an electroslag heavy melting slag system with a total weight of 6kg.
[0054] 3) Electroslag remelting
[0055] Mix the prepared electroslag remelting slag evenly, bake it at 800°C for 4 hours, use a graphite electrode rod to melt the slag, and pour it ...
PUM
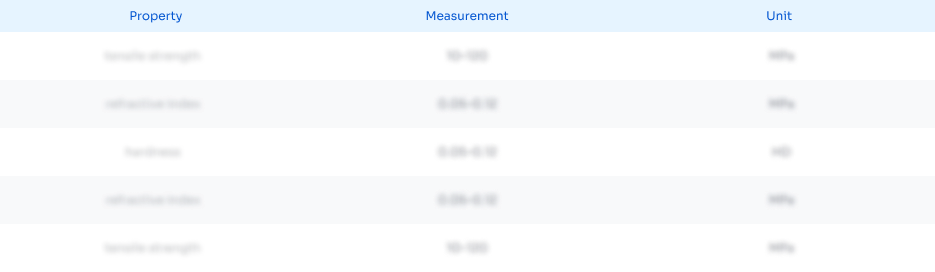
Abstract
Description
Claims
Application Information

- Generate Ideas
- Intellectual Property
- Life Sciences
- Materials
- Tech Scout
- Unparalleled Data Quality
- Higher Quality Content
- 60% Fewer Hallucinations
Browse by: Latest US Patents, China's latest patents, Technical Efficacy Thesaurus, Application Domain, Technology Topic, Popular Technical Reports.
© 2025 PatSnap. All rights reserved.Legal|Privacy policy|Modern Slavery Act Transparency Statement|Sitemap|About US| Contact US: help@patsnap.com