Heat dissipating material for LCD touch liquid crystal display and preparation method and application thereof
A technology of liquid crystal display and heat dissipation material, which is applied in heat exchange materials, chemical instruments and methods, instruments, etc., can solve the problems of poor thermal conductivity and electrical insulation performance, poor tensile yield strength, and inability to have both performances, etc. Achieve the effects of low production cost, good thermal conductivity, and improved elongation at break and thermal conductivity
- Summary
- Abstract
- Description
- Claims
- Application Information
AI Technical Summary
Problems solved by technology
Method used
Image
Examples
Embodiment 1
[0024] In an embodiment of the present invention, a heat dissipation material for an LCD touch liquid crystal display is composed of the following raw materials in parts by weight: 15 parts of graphite, 9 parts of nickel nitrate, 5 parts of vinyl triethoxysilane, and dibenzoyl 3 parts of p-quinone dioxime, 11 parts of diacetone acrylamide, 20 parts of waste rubber powder.
[0025] Mixing vinyl triethoxy silane with 5.5 times the mass of deionized water to prepare a vinyl triethoxy silane solution; mixing diacetone acrylamide with 7.8 times the mass of ethanol to prepare a diacetone acrylamide solution. The waste rubber powder is crushed, passed through a 120-mesh sieve, and then placed in a polytetrafluoroethylene reactor with the vinyltriethoxysilane solution, sealed, and then filled with nitrogen to make the pressure reach 4.8MPa, and then heated to 82°C , And heated and stirred for 1.4h at this temperature to obtain a modified waste rubber mixture. Graphite, nickel nitrate an...
Embodiment 2
[0027] In an embodiment of the present invention, a heat dissipation material for LCD touch liquid crystal display screens is composed of the following raw materials in parts by weight: 23 parts of graphite, 17 parts of nickel nitrate, 12 parts of vinyl triethoxysilane, and dibenzoyl 7 parts of p-quinone dioxime, 19 parts of diacetone acrylamide, 30 parts of waste rubber powder.
[0028] Mixing vinyl triethoxy silane with 5.5 times the mass of deionized water to prepare a vinyl triethoxy silane solution; mixing diacetone acrylamide with 7.8 times the mass of ethanol to prepare a diacetone acrylamide solution. The waste rubber powder is crushed, passed through a 120-mesh sieve, and then placed in a polytetrafluoroethylene reactor with the vinyltriethoxysilane solution, sealed, and then filled with nitrogen to make the pressure reach 5MPa, and then heated to 82°C. The mixture was heated and stirred for 1.4 hours at this temperature to obtain a modified waste rubber mixture. Graphi...
Embodiment 3
[0030] In an embodiment of the present invention, a heat dissipation material for LCD touch liquid crystal display screens is composed of the following raw materials in parts by weight: 17 parts of graphite, 11 parts of nickel nitrate, 7 parts of vinyl triethoxysilane, and dibenzoyl 4 parts of p-quinone dioxime, 13 parts of diacetone acrylamide, 22 parts of waste rubber powder.
[0031] Mixing vinyl triethoxy silane with 5.5 times the mass of deionized water to prepare a vinyl triethoxy silane solution; mixing diacetone acrylamide with 7.8 times the mass of ethanol to prepare a diacetone acrylamide solution. Crush the waste rubber powder and pass it through a 120-mesh sieve, then place it and the vinyltriethoxysilane solution into a polytetrafluoroethylene reactor for sealing, then fill it with nitrogen to make the pressure reach 4.9MPa, and then heat to 82°C , And heated and stirred for 1.4h at this temperature to obtain a modified waste rubber mixture. Graphite, nickel nitrate...
PUM
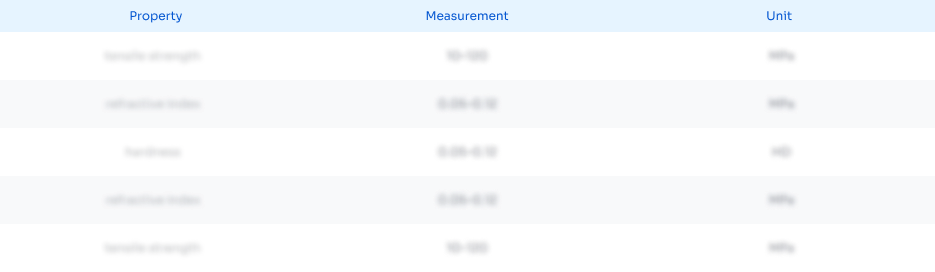
Abstract
Description
Claims
Application Information

- R&D
- Intellectual Property
- Life Sciences
- Materials
- Tech Scout
- Unparalleled Data Quality
- Higher Quality Content
- 60% Fewer Hallucinations
Browse by: Latest US Patents, China's latest patents, Technical Efficacy Thesaurus, Application Domain, Technology Topic, Popular Technical Reports.
© 2025 PatSnap. All rights reserved.Legal|Privacy policy|Modern Slavery Act Transparency Statement|Sitemap|About US| Contact US: help@patsnap.com