Acrylate emulsion of water-based ink for soft PVC (Polyvinyl Chloride) and preparation method thereof
An acrylate and water-based technology, which is applied to the acrylate emulsion of soft PVC water-based ink and its preparation field, can solve the problems affecting the stability and printing effect of water-based ink, poor adhesion of printing substrates, poor color paste compatibility, etc. problem, to achieve the effect of increased strength, improved adhesion, and good water resistance
- Summary
- Abstract
- Description
- Claims
- Application Information
AI Technical Summary
Problems solved by technology
Method used
Image
Examples
Embodiment 1
[0035] Take 15 parts of methyl acrylate, 10 parts of ethyl acrylate, 10 parts of methyl methacrylate and 8 parts of methacrylic acid and mix uniformly to obtain mixture A; 10 parts of butyl acrylate, 10 parts of vinyl acetate, methyl methacrylate Mix 6 parts with 1.2 parts of ethylene glycol diacrylate to obtain mixture B; 15 parts of butyl acrylate, 15 parts of methyl methacrylate and 1.2 parts of ethylene glycol diacrylate to obtain mixture C, set aside.
[0036] Add 200 parts of deionized water to the reactor, raise the temperature of the reactor to 83, then add 3 parts of 1-allyloxy-2-hydroxypropanesulfonate sodium, stir for five minutes and then add ammonium persulfate 0.35 servings.
[0037] Add the mixture A into the reaction kettle dropwise, and control the dropping within 1.5 to 2.5 hours. After holding the heat for half an hour, add 8.5 parts of 22% ammonia water at one time, and continue stirring for ten minutes.
Embodiment 2
[0041] Take 12 parts of ethyl acrylate, 15 parts of hydroxyethyl methacrylate, 3 parts of methyl methacrylate, 9 parts of ethyl methacrylate, and 10 parts of acrylic acid to obtain mixture A; 4 parts of methyl acrylate, ethyl acrylate 10 parts of butyl methacrylate, 5 parts of butyl methacrylate, 2 parts of methyl methacrylate, 5 parts of ethyl methacrylate, 0.5 parts of dicyclopentyl acrylate, and 1.4 parts of diethylene glycol diacrylate were mixed uniformly to obtain mixture B ; 18 parts of butyl acrylate, 2 parts of ethylene tertiary carbonic acid, 5 parts of methyl methacrylate, 1 part of styrene, 0.5 parts of dicyclopentyl acrylate, 0.5 parts of 1,3-butanediol diacrylate to obtain mixture C ,spare.
[0042] Add 185 parts of deionized water into the reactor, raise the temperature of the reactor to 85°C, then add 0.5 parts of allyl polyether sodium sulfate, 2.7 parts of allyl phenoxy polyether ammonium sulfate, and stir for five Minutes later, 0.45 parts of ammonium persu...
Embodiment 3
[0047] Take 8 parts of hydroxyethyl acrylate, 7 parts of hydroxypropyl acrylate, 14 parts of hydroxypropyl methacrylate, 2 parts of methyl methacrylate, 10 parts of sodium p-styrenesulfonate, 6 parts of itaconic acid, fumarate Mix 7 parts of monobutyl acrylate to obtain mixture A; 12 parts of tert-butyl acrylate, 9 parts of isooctyl methacrylate, 6 parts of methyl methacrylate, 1 part of styrene, 1.5 parts of ethylene glycol diacrylate, Mix 0.6 parts of polyethylene glycol diacrylate to obtain mixture B; 14 parts of tert-butyl acrylate, 8 parts of butyl methacrylate, 6 parts of ethyl methacrylate, and 1 part of ethylene glycol diacrylate to obtain mixture C. spare.
[0048] Add 220 parts of deionized water into the reactor, raise the temperature of the reactor to 80°C, then add 3.8 parts of sodium vinylsulfonate, stir for five minutes and then add 0.5 parts of sodium persulfate.
[0049] Add the mixture A into the reaction kettle dropwise, and control the dropping within 1.5 ...
PUM
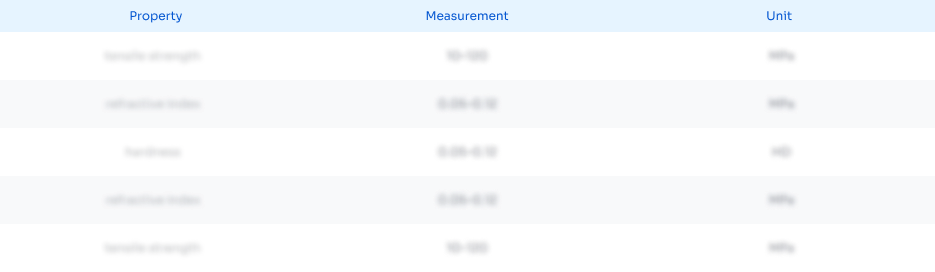
Abstract
Description
Claims
Application Information

- Generate Ideas
- Intellectual Property
- Life Sciences
- Materials
- Tech Scout
- Unparalleled Data Quality
- Higher Quality Content
- 60% Fewer Hallucinations
Browse by: Latest US Patents, China's latest patents, Technical Efficacy Thesaurus, Application Domain, Technology Topic, Popular Technical Reports.
© 2025 PatSnap. All rights reserved.Legal|Privacy policy|Modern Slavery Act Transparency Statement|Sitemap|About US| Contact US: help@patsnap.com