Preparation method of polycrystalline mullite fiber
A polycrystalline mullite and fiber technology, applied in the direction of inorganic raw materials such as artificial filaments, can solve the problems of strict equipment requirements, difficult process control, high production costs, etc., and achieve tight bonding, uniform grain size, and complete crystal phase structure Effect
- Summary
- Abstract
- Description
- Claims
- Application Information
AI Technical Summary
Problems solved by technology
Method used
Examples
Embodiment 1
[0018] With water as solvent, aluminum powder, AlCl 3 Reflux the raw material to obtain a colorless and transparent polyaluminum chloride sol; add acidic silica sol, add spinning aid, concentrate in vacuum, and remove part of the free water to obtain a viscous precursor sol; prepare the precursor by spinning the sol through the spinning method Fiber, the obtained precursor fiber is dried and heat-treated to finally produce polycrystalline mullite fiber.
[0019] Wherein, the reflux temperature is 90° C., and the reflux time is 5 hours. Said adding to the acidic silica sol, the amount of substance m (Al):m (Si)=3:1. The described spinning aid is 3% polyvinyl alcohol in mass fraction. The viscosity of the precursor sol is 4000. The drying temperature is 60° C., and the drying time is 4 hours. The heat treatment temperature is 800° C., and the heat treatment time is 2 hours. The temperature of the vacuum concentration is 50°C.
Embodiment 2
[0021] With water as solvent, aluminum powder, AlCl 3 Reflux the raw material to obtain a colorless and transparent polyaluminum chloride sol; add acidic silica sol, add spinning aid, concentrate in vacuum, and remove part of the free water to obtain a viscous precursor sol; prepare the precursor by spinning the sol through the spinning method Fiber, the obtained precursor fiber is dried and heat-treated to finally produce polycrystalline mullite fiber.
[0022] Wherein, the reflux temperature is 100° C., and the reflux time is 8 hours. Said adding to the acidic silica sol, the amount of substance m (Al):m (Si)=3:1. The described spinning aid is 3% polyvinyl alcohol in mass fraction. The viscosity of the precursor sol is 6000. The drying temperature is 80° C., and the drying time is 6 hours. The heat treatment temperature is 1300° C., and the heat treatment time is 3 hours. The temperature of the vacuum concentration is 60°C.
Embodiment 3
[0024] With water as solvent, aluminum powder, AlCl 3 Reflux the raw material to obtain a colorless and transparent polyaluminum chloride sol; add acidic silica sol, add spinning aid, concentrate in vacuum, and remove part of the free water to obtain a viscous precursor sol; prepare the precursor by spinning the sol through the spinning method Fiber, the obtained precursor fiber is dried and heat-treated to finally produce polycrystalline mullite fiber.
[0025] Wherein, the reflux temperature is 95°C, and the reflux time is 6h. Said adding to the acidic silica sol, the amount of substance m (Al):m (Si)=3:1. The described spinning aid is 3% polyvinyl alcohol in mass fraction. The viscosity of the precursor sol is 4000. The drying temperature is 70° C., and the drying time is 5 hours. The heat treatment temperature is 1000° C., and the heat treatment time is 2 hours. The temperature of the vacuum concentration is 55°C.
PUM
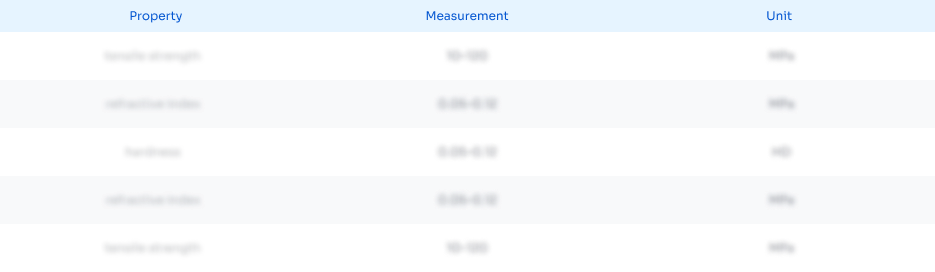
Abstract
Description
Claims
Application Information

- R&D
- Intellectual Property
- Life Sciences
- Materials
- Tech Scout
- Unparalleled Data Quality
- Higher Quality Content
- 60% Fewer Hallucinations
Browse by: Latest US Patents, China's latest patents, Technical Efficacy Thesaurus, Application Domain, Technology Topic, Popular Technical Reports.
© 2025 PatSnap. All rights reserved.Legal|Privacy policy|Modern Slavery Act Transparency Statement|Sitemap|About US| Contact US: help@patsnap.com