Production process capable of effectively reducing cracks of antimony-containing weather-proof round steel
A production process and weather-resistant technology, which is applied in the field of metallurgy, can solve problems such as grain boundary segregation of antimony elements, adverse effects on steel surface quality, and low production efficiency, so as to achieve high production efficiency, reduce antimony-containing weather-resistant round steel cracks, and surface good quality effect
- Summary
- Abstract
- Description
- Claims
- Application Information
AI Technical Summary
Problems solved by technology
Method used
Examples
Embodiment 1
[0037] (1) Converter smelting
[0038] High-quality molten iron is used for converter smelting, among which, the mass content requirements of components in molten iron entering the furnace are: Si: 0.45%, P: 0.094%, S: 0.030%, and the temperature of molten iron entering the furnace is T = 1310°C;
[0039] Converter smelting controls tapping end point [C]=0.05%, end point [P]=0.012%, tapping temperature is 1635°C, the tapping process adopts sliding plate slag blocking operation, tapping time is 4.0 minutes, tapping 1 / 4 hour Deoxidizer, alloy and slag are added to molten steel in turn,
[0040] Among them, the added deoxidizer is 1kg / t each of calcium carbide and aluminum cake; the added alloys are 5.8kg / t silicon manganese, 2.5kg / t ferrosilicon, 15.8kg / t ferrochrome, 4.0kg / t copper, 0.62 antimony alloy kg / t, nickel plate 3.3kg / t; the added slag is lime 800kg / furnace (120 tons per furnace, the same below), synthetic slag 200kg / furnace;
[0041] (2) Refining process
[0042]Th...
Embodiment 2
[0051] In step (2), "this furnace is a pouring furnace, and the temperature of the hanging bag after soft blowing is controlled to be 1615-1630°C" is changed to "this furnace is a continuous pouring furnace, and the temperature of the hanging bag after soft blowing is controlled as 1600~1615 DEG C", the degree of superheat in step (3) is 40 DEG C and amends to 29 DEG C, all the other operations are identical with embodiment 1.
[0052] The chemical composition of the antimony-containing weathering round steel produced in this embodiment is calculated by mass percentage: C 0.09%, Si 0.35%, Mn 0.50%, Cr 0.91%, Cu 0.43%, Sb 0.06%, Ni 0.32%, sulfur The content is controlled to be 0.011%, the oxygen content is controlled to be 22ppm, the Ti content is controlled to be 0.038%, and the rest is Fe and trace elements.
[0053] Tracking of the obtained continuous casting slabs and rolled products: the surface quality of the continuous casting slabs and rolled products is good, no cracks...
Embodiment 3
[0055] Modify the pulling speed in step (3) to 1.82m / min, modify the heating rate in step (4) to 16.7°C / min, modify the tapping rhythm to 58 seconds, and the rest of the operations are the same as in Example 2.
[0056] Follow up the obtained continuous casting slabs and rolled materials: the surface quality of the continuous casting slabs and rolled materials is good, no cracks occur, and the pass rate of one-time flaw detection is 95.4%. it is good.
PUM
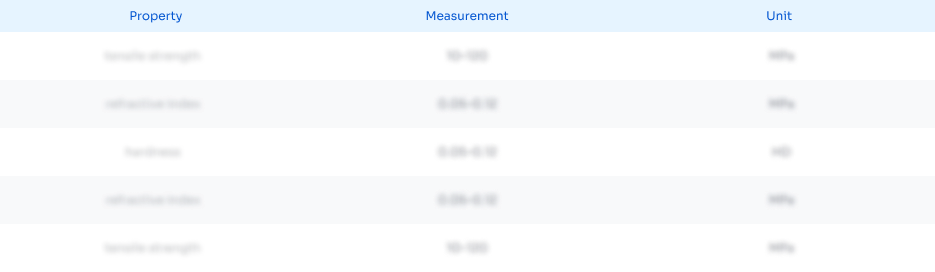
Abstract
Description
Claims
Application Information

- R&D
- Intellectual Property
- Life Sciences
- Materials
- Tech Scout
- Unparalleled Data Quality
- Higher Quality Content
- 60% Fewer Hallucinations
Browse by: Latest US Patents, China's latest patents, Technical Efficacy Thesaurus, Application Domain, Technology Topic, Popular Technical Reports.
© 2025 PatSnap. All rights reserved.Legal|Privacy policy|Modern Slavery Act Transparency Statement|Sitemap|About US| Contact US: help@patsnap.com