Fiberglass reinforced plastic raw material for manufacturing oil separation tank
A glass fiber reinforced plastic and oil separator technology, which is applied in the field of composite materials, can solve the problems of destroying molecular structure, reducing material strength, cutting glass fibers, etc., and achieves the effects of good stain resistance, improved corrosion resistance, and reduced stress concentration.
- Summary
- Abstract
- Description
- Claims
- Application Information
AI Technical Summary
Problems solved by technology
Method used
Examples
Embodiment 1
[0024] A kind of glass fiber reinforced plastic raw material that is used to manufacture grease trap, is made of the material of following parts by weight:
[0025] 45 parts of unsaturated polyester resin, 8 parts of epoxy resin, 6 parts of phenolic resin, 38 parts of composite fiber filler, 2 parts of antioxidant, 1 part of polymerization inhibitor, 4 parts of toughening agent, 2 parts of curing agent, 1 part of accelerator agent; the mixed modified fiber filler is made of the following parts by weight: 63 parts of glass fiber, 4 parts of kaolin, 5 parts of zeolite powder, 5 parts of graphene, and 6 parts of kapok fiber.
[0026] Further, the antioxidant is composed of antioxidant 1010 and antioxidant 1076.
[0027] Further, the polymerization inhibitor consists of hydroquinone and p-hydroxyanisole.
[0028] Further, the toughening agent is composed of dibutyl phthalate and polyvinyl butyral.
[0029] Further, the curing agent is composed of ethylenediamine, diaminodiphenyl...
Embodiment 2
[0038] A kind of glass fiber reinforced plastic raw material that is used to manufacture grease trap, is made of the material of following parts by weight:
[0039] 48 parts of unsaturated polyester resin, 9 parts of epoxy resin, 8 parts of phenolic resin, 40 parts of composite fiber filler, 2.5 parts of antioxidant, 2 parts of polymerization inhibitor, 6 parts of toughening agent, 3 parts of curing agent, 2 parts of accelerator agent; the mixed modified fiber filler is made of the following parts by weight: 65 parts of glass fiber, 5 parts of kaolin, 7 parts of zeolite powder, 6 parts of graphene, and 7 parts of kapok fiber. All the other method steps are the same as in Example 1.
Embodiment 3
[0041] A kind of glass fiber reinforced plastic raw material that is used to manufacture grease trap, is made of the material of following parts by weight:
[0042] 50 parts of unsaturated polyester resin, 11 parts of epoxy resin, 10 parts of phenolic resin, 42 parts of composite fiber filler, 3 parts of antioxidant, 3 parts of polymerization inhibitor, 7 parts of toughening agent, 4 parts of curing agent, 3 parts of accelerator agent; the mixed modified fiber filler is made of the following parts by weight: 67 parts of glass fiber, 6 parts of kaolin, 8 parts of zeolite powder, 7 parts of graphene, and 8 parts of kapok fiber. All the other method steps are the same as in Example 1.
PUM
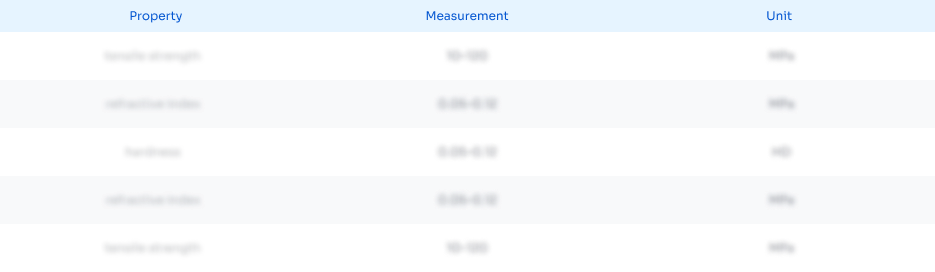
Abstract
Description
Claims
Application Information

- Generate Ideas
- Intellectual Property
- Life Sciences
- Materials
- Tech Scout
- Unparalleled Data Quality
- Higher Quality Content
- 60% Fewer Hallucinations
Browse by: Latest US Patents, China's latest patents, Technical Efficacy Thesaurus, Application Domain, Technology Topic, Popular Technical Reports.
© 2025 PatSnap. All rights reserved.Legal|Privacy policy|Modern Slavery Act Transparency Statement|Sitemap|About US| Contact US: help@patsnap.com