High-speed tool steel for sintering procedure of metal injection molding
A high-speed tool steel and injection molding technology, applied in metal processing equipment, transportation and packaging, etc., can solve the problems of poor mechanical properties, reduced mechanical properties of materials, and limited improvement effects, etc., to improve mechanical properties and increase mechanical properties , increase the effect of bridging
- Summary
- Abstract
- Description
- Claims
- Application Information
AI Technical Summary
Problems solved by technology
Method used
Image
Examples
Embodiment 1
[0031] The ratio of the weight percentage of the iron element in the master alloy phase metal powder to the weight of the iron element in the ultrafine metal iron powder or nano-metal iron powder in the high-speed tool steel is 81.34%, and the master alloy phase metal powder The ratio of the weight of the iron element in the body in the high-speed tool steel to the weight of the ultra-fine metal iron powder or nano-metal iron powder in the high-speed tool steel is 1:1. The weight percentages within tool steel are as follows:
[0032] Fe Cr Mo C W V mn Si 40.67 4.125 5 0.83 6.125 1.975 0.275 0.325
[0033] The generated high-speed tool steel is a complete SKH51 tool steel material phase, the sintering temperature can be reduced, the mechanical properties can be improved, and the shortcomings of traditional high-temperature sintering can be avoided.
Embodiment 2
[0035]The ratio of the weight percentage of the iron element in the master alloy phase metal powder to the weight of the iron element in the ultrafine metal iron powder or nano-metal iron powder in the high-speed tool steel is 81.34%, and the master alloy phase metal powder The ratio of the weight of the iron element in the body in the high-speed tool steel to the weight of the ultra-fine metal iron powder or nano-metal iron powder in the high-speed tool steel is 1:2, and the chemical components of the master alloy phase metal powder are in the The weight percentages in high speed tool steel are as follows:
[0036] Fe Cr Mo C W V mn Si 27.15 4.125 5 0.83 6.125 1.975 0.275 0.325
[0037] The high-speed tool steel produced by the iron element in the master alloy phase metal powder and ultra-fine metal iron powder or nano-metal iron powder is a complete SKH51 tool steel material phase, the sintering temperature can be reduced, the mechanical pr...
Embodiment 3
[0039] The ratio of the weight percentage of the iron element in the master alloy phase metal powder to the weight of the iron element in the ultrafine metal iron powder or nano-metal iron powder in the high-speed tool steel is 81.34%, and the master alloy phase metal powder The ratio of the weight of the iron element in the body in the high-speed tool steel to the weight of the ultra-fine metal iron powder or nano-metal iron powder in the high-speed tool steel is 1:3, and the chemical components of the master alloy phase metal powder are in the The weight percentages in high speed tool steel are as follows:
[0040] Fe Cr Mo C W V mn Si 20.34 4.125 5 0.83 6.125 1.975 0.275 0.325
[0041] The high-speed tool steel produced by the iron element in the master alloy phase metal powder and ultra-fine metal iron powder or nano-metal iron powder is a complete SKH51 tool steel material phase, the sintering temperature can be reduced, the mechanical p...
PUM
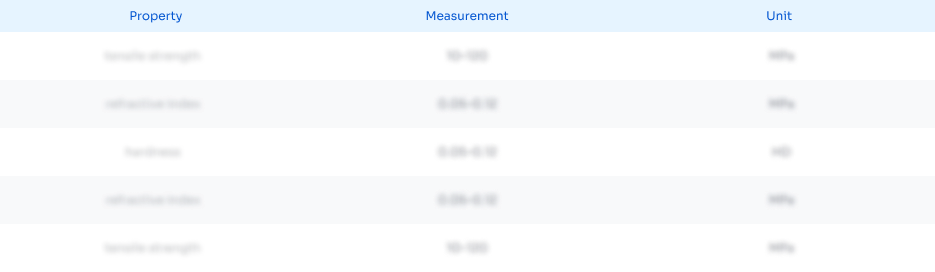
Abstract
Description
Claims
Application Information

- R&D
- Intellectual Property
- Life Sciences
- Materials
- Tech Scout
- Unparalleled Data Quality
- Higher Quality Content
- 60% Fewer Hallucinations
Browse by: Latest US Patents, China's latest patents, Technical Efficacy Thesaurus, Application Domain, Technology Topic, Popular Technical Reports.
© 2025 PatSnap. All rights reserved.Legal|Privacy policy|Modern Slavery Act Transparency Statement|Sitemap|About US| Contact US: help@patsnap.com