Lubricating oil composite filter aid and preparation method thereof
A filter aid, lubricating oil technology, applied in lubricating compositions, chemical instruments and methods, other chemical processes, etc., can solve the problems of unsatisfactory permeability, increased filtration cost, poor oil quality, etc., and achieve ideal screening Filtering effect, accelerating pre-filtering layer formation, increasing toughness and rigidity effect
- Summary
- Abstract
- Description
- Claims
- Application Information
AI Technical Summary
Problems solved by technology
Method used
Image
Examples
preparation example Construction
[0026] A preparation method of a lubricating oil composite filter aid, mainly comprising ingredients; acidification, washing, drying, roasting, and screening of inorganic minerals; washing, drying, and screening of organic cellulose; and inorganic minerals and organic cellulose The mixing and other steps are composed.
[0027] 1. Ingredients
[0028] The ingredients consist of inorganic minerals and organic cellulose. The proportion of inorganic minerals is 50-90%, at least two or more of activated clay, diatomite, bentonite, activated carbon, perlite, zeolite, attapulgite, sepiolite, fly ash, steel slag powder, and slag powder The proportion of organic cellulose is 10-50%, which is selected from one or more of sawdust, sawdust, bagasse, bran, paper pulp, rice husk, bamboo chips, straw residue, and lignocellulose.
[0029] Activated white clay is commonly known as activated clay, and its main component is montmorillonite minerals. It has the ability to absorb colored substan...
Embodiment 1
[0057] A composite filter aid suitable for filtering waste lubricating oil, the preparation process of which is as follows:
[0058] (1) Ingredients: by weight percentage, it includes the following components: 10% activated clay, 40% diatomaceous earth, 10% activated carbon, 10% fly ash, and 30% sawdust.
[0059] (2) Batching, acidification, washing, drying, roasting, sieving of inorganic minerals: Four active clay (10%), diatomaceous earth (40%), activated carbon (10%) and fly ash (10%) After the two materials are mixed evenly, place them in 5mol / L sulfuric acid solution, keep the soaking temperature at 80°C, and the solid-to-liquid ratio at 1:5, and pickle for 8 hours under constant stirring. After the pickling, wash the material until the pH value is neutral, filter it with suction, and dry it at 70-105°C to constant weight. The inorganic mixture material is roasted at 450°C for 2 hours, cooled to room temperature, and sieved to control the particle size of the material to...
Embodiment 2
[0065] Compared with Example 1, the process conditions are the same, the difference is that the proportion of ingredients is different; the proportion of ingredients is: activated clay 5%, diatomaceous earth 30%, activated carbon 20%, slag micropowder 20%, sawdust 25%.
[0066] The use of composite filter aids:
[0067] Using the lubricating oil composite filter aid obtained in Example 2, according to the ratio of 1:20 to the waste oil, add it to the waste lubricating oil refined by sulfuric acid-clay, keep the oil temperature at 80°C, and filter, before and after filtration , the turbidity decreased from 6NTU (scattering turbidity unit) to 0.3NTU, and the color changed from reddish brown to light yellow and transparent, while the reference two groups (using activated clay and diatomaceous earth as a single filter aid, activated by acid washing and roasting) The operation is the same as this composite filter aid, the ratio of filter aid to waste oil is 1:20), after filtration,...
PUM
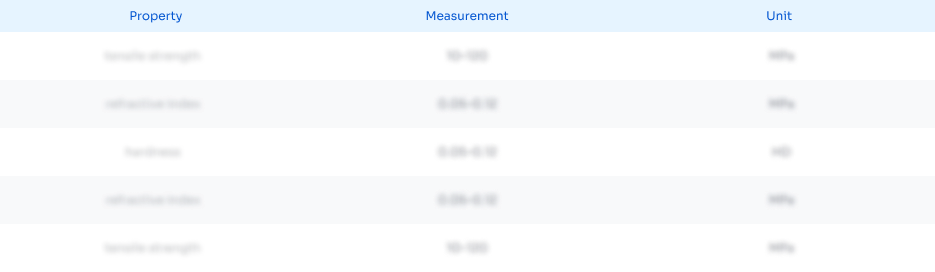
Abstract
Description
Claims
Application Information

- R&D Engineer
- R&D Manager
- IP Professional
- Industry Leading Data Capabilities
- Powerful AI technology
- Patent DNA Extraction
Browse by: Latest US Patents, China's latest patents, Technical Efficacy Thesaurus, Application Domain, Technology Topic, Popular Technical Reports.
© 2024 PatSnap. All rights reserved.Legal|Privacy policy|Modern Slavery Act Transparency Statement|Sitemap|About US| Contact US: help@patsnap.com