Methyl methacrylate modified silicon resin coating and preparation method thereof
A technology of methyl methacrylate and modified resin, applied in coatings and other directions, can solve the problems of general silicone resin adhesion performance, poor mechanical properties and anti-corrosion requirements, affecting thermal protection performance, etc., to speed up the coating process. Curing speed, stable product performance, anti-pollution effect
- Summary
- Abstract
- Description
- Claims
- Application Information
AI Technical Summary
Problems solved by technology
Method used
Image
Examples
Embodiment 1
[0039] Synthesis of addition products: Add 67.43g of trimethoxysilane, 101.354g of toluene and 0.926g of platinum catalyst solution into a 500ml three-necked flask equipped with a reflux condenser, a thermometer and a magnet, and raise the temperature to 60°C. Add 50.06 g of methyl methacrylate dropwise into the liquid funnel, react for 1 hour, then raise the temperature to 85°C, react for 2 hours and then lower the temperature to below 40°C and carry out vacuum distillation to 120°C to obtain the addition product.
[0040] The molar ratio of trimethoxysilane to toluene is 1:2, and the molar ratio of methyl methacrylate is 1.1:1; the amount of chloroplatinic acid is the sum of the mass of trimethoxysilane and methyl methacrylate (50-100)* 10 -6 ;
[0041] Synthesis of modified resin (5% addition product, mole fraction): put 11.12g of addition product, 61.30g of methyltrimethoxysilane, and 99.15g of phenyltrimethoxysilane into a three-necked bottle, drop 8.74g Water and an ap...
Embodiment 2
[0047] Synthesis of addition products: Add 153.25g of trimethoxysilane, 92.14g of toluene and 1.996g of platinum catalyst solution into a 500ml three-necked flask equipped with a reflux condenser, a thermometer and a magnet, and raise the temperature to 60°C. Add 100.12 g of methyl methacrylate dropwise into the liquid funnel, react for 1 hour, then raise the temperature to 85°C, react for 2 hours and then lower the temperature to below 40°C and carry out vacuum distillation to 120°C to obtain the addition product. The molar ratio of trimethoxysilane to toluene is 1:1, and the molar ratio of methyl methacrylate is 1.25:1; the amount of chloroplatinic acid is the sum of the mass of trimethoxysilane and methyl methacrylate (50-100)* 10 -6 ;
[0048] Synthesis of modified resin (10% addition product, mole fraction): put 9g of addition product, 22.08g of methyltrimethoxysilane, and 40.125g of phenyltrimethoxysilane into a three-necked bottle, drop 8.735g of water , and add an ap...
Embodiment 3
[0055] Addition product synthesis and equipment are as above;
[0056] Synthesis of modified resin (20% addition product, mole fraction): put 22.24g of addition product, 20.433g of methyltrimethoxysilane, and 49.57g of phenyltrimethoxysilane into a three-necked bottle, drop 9g of water , and add an appropriate amount of hydrochloric acid as a catalyst (keep the drop rate of 1-2 seconds per drop); hydrolyze at room temperature (30°C) for one hour; raise the temperature to 60°C, and react for 2 hours; after the condensation is completed, change the distillation device and heat up to 85°C. The product methanol is distilled out (about three hours), and a certain amount of petroleum ether is added after the reaction is complete, so that the mass fraction of the resin is 90%.
[0057] Synthetic silicone oil: put 91.15g of methylphenyldimethoxysilane into a three-necked bottle, drop in 9g of water, and add an appropriate amount of hydrochloric acid as a catalyst (keep the water drop ...
PUM
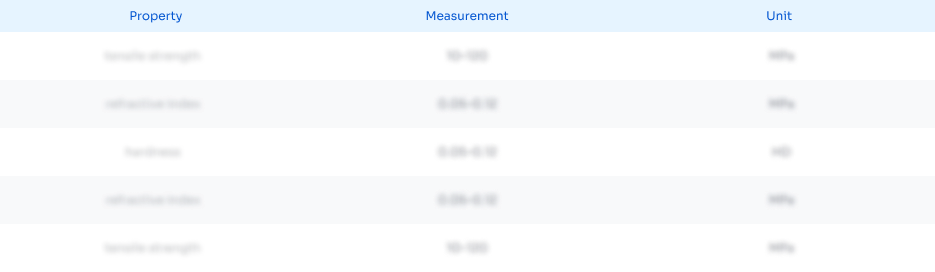
Abstract
Description
Claims
Application Information

- Generate Ideas
- Intellectual Property
- Life Sciences
- Materials
- Tech Scout
- Unparalleled Data Quality
- Higher Quality Content
- 60% Fewer Hallucinations
Browse by: Latest US Patents, China's latest patents, Technical Efficacy Thesaurus, Application Domain, Technology Topic, Popular Technical Reports.
© 2025 PatSnap. All rights reserved.Legal|Privacy policy|Modern Slavery Act Transparency Statement|Sitemap|About US| Contact US: help@patsnap.com