Nickel base alloy material resisting abrasion and hydrofluoric acid corrosion and preparing method of nickel base alloy material
A nickel-based alloy and hydrofluoric acid-resistant technology, which is applied in the field of fluoroplastic processing, can solve the problem that the wear resistance and corrosion resistance cannot be maximized, and the hydrofluoric acid resistance and wear resistance and corrosion resistance cannot be satisfied at the same time. problems, to achieve good market potential, popularization and development benefits, and low manufacturing costs
- Summary
- Abstract
- Description
- Claims
- Application Information
AI Technical Summary
Problems solved by technology
Method used
Image
Examples
Embodiment 1
[0029] Embodiment 1 This embodiment 1 provides a wear-resistant and hydrofluoric acid corrosion resistant nickel-based alloy, which is prepared according to the following composition ratio and process:
[0030] (1) The composition ratio of the materials and the amount of 100KG raw materials are listed in Table 1 below:
[0031] Table 1 Component distribution ratio and amount of each raw material
[0032]
[0033]
[0034] (2) The specific preparation method includes the following steps:
[0035] (1) Add about 1 / 3 of electrolytic nickel to an intermediate frequency furnace with a capacity of 100KG, then add all graphite, all metallic chromium, all nickel boron, all pure iron, 1 / 2 electrolytic copper, 1 / 3 Of industrial silicon, and finally covered with a layer of nickel plate;
[0036] (2) Raise the intermediate frequency power to smelt the charge to fully alloy the melt;
[0037] (3) Add remaining electrolytic copper and electrolytic nickel, and continue smelting until the melt is fully ...
Embodiment 2
[0041] Embodiment 2 This embodiment 2 provides a nickel-based alloy with wear resistance and hydrofluoric acid corrosion, which is prepared according to the following composition ratio and process:
[0042] (1) The composition ratio of the materials and the amount of 100KG raw materials are listed in Table 2 below:
[0043] Table 2 Composition ratio and the amount of each raw material
[0044] element Target composition (%) Allocation value (%) Matching weight Remarks C0.070.08 0.08kg Cr0.20.2 0.2kg B2.22.3 12.78kg nickel boron 18% boron in nickel boron Si3.03.0 3.0kg Fe1.21.1 1.1kg A small amount of Fe in other raw materials Cu19.019.0 19.0kg Ni margin74.32 63.84kg
[0045] (2) The specific preparation method includes the following steps:
[0046] (1) Add about 1 / 3 of electrolytic nickel to an intermediate frequency furnace with a capacity of 100KG, then add all graphite, all metallic chromium, all nickel boron, all pure iron, 1 / 2 electrolytic copper, 1 / 3 The industrial silicon...
Embodiment 3
[0052] Embodiment 3 This embodiment 3 provides a nickel-based alloy with wear resistance and hydrofluoric acid corrosion, which is prepared according to the following composition ratio and process:
[0053] (1) The composition ratio of the materials and the amount of 100KG raw materials are listed in Table 3 below:
[0054] Table 3 Component distribution ratio and the amount of each raw material
[0055]
[0056] (2) The specific preparation method includes the following steps:
[0057] (1) Add about 1 / 3 of electrolytic nickel to an intermediate frequency furnace with a capacity of 100KG, then add all graphite, all metallic chromium, all nickel boron, all pure iron, 1 / 2 electrolytic copper, 1 / 3 The industrial silicon is finally covered with a layer of nickel plate.
[0058] (2) Increase the power of the intermediate frequency to melt the charge to fully alloy the melt.
[0059] (3) Add remaining electrolytic copper and electrolytic nickel, and continue smelting until the melt is fully a...
PUM
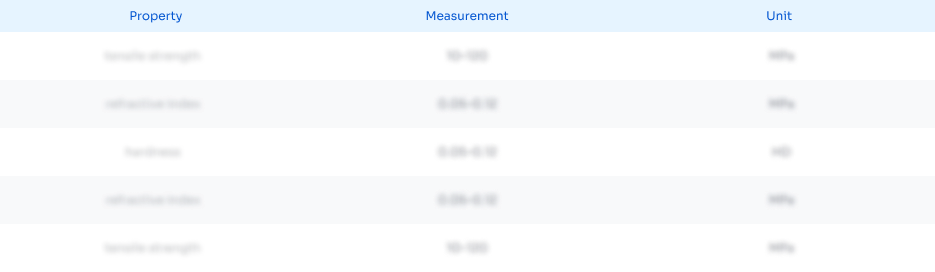
Abstract
Description
Claims
Application Information

- R&D
- Intellectual Property
- Life Sciences
- Materials
- Tech Scout
- Unparalleled Data Quality
- Higher Quality Content
- 60% Fewer Hallucinations
Browse by: Latest US Patents, China's latest patents, Technical Efficacy Thesaurus, Application Domain, Technology Topic, Popular Technical Reports.
© 2025 PatSnap. All rights reserved.Legal|Privacy policy|Modern Slavery Act Transparency Statement|Sitemap|About US| Contact US: help@patsnap.com