Two-stage selective heterogenite leaching method
A selective, leaching water technology, applied in the field of hydrometallurgy, can solve problems such as deterioration of the operating environment, increased iron content, and complex treatment processes, and achieve the effects of friendly operating environment, reduced cobalt loss, and simple operation
- Summary
- Abstract
- Description
- Claims
- Application Information
AI Technical Summary
Problems solved by technology
Method used
Image
Examples
Embodiment 1
[0028]The hydrocobalt ore with a particle size of -200 mesh accounting for more than 80% and water are made into a pulp with a concentration of 33%; then sulfuric acid is added to the pulp, and the amount of sulfuric acid added is 10% of the mass fraction of the hydrocobalt ore, and stirred at room temperature for 0.5h; After solid-liquid separation, leaching solution and copper leaching slag are obtained. The copper leaching slag is subjected to two-stage cobalt leaching in a certain concentration of sulfuric acid aqueous solution, and solid-liquid separation is carried out after leaching to obtain a cobalt-rich leaching solution and leaching slag. The conditions for the second reduction and leaching of cobalt are as follows: the concentration of the pulp is 20%, the initial concentration of sulfuric acid is 10g / L, the leaching temperature is normal temperature, the amount of reductant iron powder is 1 times the theoretical amount, and the stirring and leaching is 0.5h.
[00...
Embodiment 2
[0034] The hydrocobalt ore with a particle size of -200 mesh accounting for more than 80% and water are made into a slurry with a concentration of 33%; then sulfuric acid is added to the slurry, and the amount of sulfuric acid added is 15% of the mass fraction of the hydrocobalt ore, and stirred at room temperature for 1 hour; After liquid separation, leachate and copper leaching slag are obtained. The copper leaching slag is subjected to two-stage cobalt leaching in a certain concentration of sulfuric acid aqueous solution, and solid-liquid separation is carried out after leaching to obtain a cobalt-rich leaching solution and leaching slag. The conditions for the second reduction and leaching of cobalt are: pulp concentration 33%, initial sulfuric acid concentration 15g / L, leaching temperature 45°C, reductant iron powder addition amount 1 times the theoretical amount, stirring leaching time 1h.
[0035] result.
[0036] The copper leaching rate is 96.84%.
[0037] The cobal...
Embodiment 3
[0040] The hydrocobalt ore with a particle size of -200 mesh accounting for more than 80% and water are made into a slurry with a concentration of 33%; then sulfuric acid is added to the slurry, and the amount of sulfuric acid added is 15% of the mass fraction of the hydrocobalt ore, and stirred at room temperature for 2 hours; After liquid separation, leachate and copper leaching slag are obtained. The copper leaching slag is subjected to two-stage cobalt leaching in a certain concentration of sulfuric acid aqueous solution, and solid-liquid separation is carried out after leaching to obtain a cobalt-rich leaching solution and leaching slag. The conditions for the second reduction and leaching of cobalt are: pulp concentration 20%, initial sulfuric acid concentration 20g / L, leaching temperature 50°C, reductant iron powder 1.5 times the theoretical amount, stirring leaching time 1.5h.
[0041] result.
[0042] The copper leaching rate is 97.12%.
[0043] The cobalt leaching ...
PUM
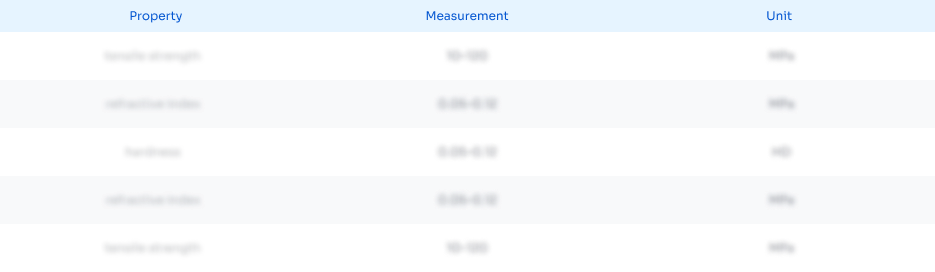
Abstract
Description
Claims
Application Information

- Generate Ideas
- Intellectual Property
- Life Sciences
- Materials
- Tech Scout
- Unparalleled Data Quality
- Higher Quality Content
- 60% Fewer Hallucinations
Browse by: Latest US Patents, China's latest patents, Technical Efficacy Thesaurus, Application Domain, Technology Topic, Popular Technical Reports.
© 2025 PatSnap. All rights reserved.Legal|Privacy policy|Modern Slavery Act Transparency Statement|Sitemap|About US| Contact US: help@patsnap.com