Technique for producing shining stainless steel pipe
A stainless steel tube and production process technology, applied in the field of natural color whitening treatment of stainless steel tubes, can solve the problems of corroded skin, pulmonary edema, sore throat, etc., and achieve the effect of accelerating the cooling speed, high safety, and ensuring the surface quality of the finished product
- Summary
- Abstract
- Description
- Claims
- Application Information
AI Technical Summary
Problems solved by technology
Method used
Image
Examples
Embodiment 1
[0028] The specific embodiment of the present invention is as figure 1 As shown, a bright stainless steel pipe production process, the equipment used includes a heat treatment box 1, a cooling pipeline 2 and a water washing box 3 arranged in sequence along the moving direction of the stainless steel pipe 4. The heat treatment box 1 is provided with a high-frequency heating tube 11 with a coil wound outside, and the stainless steel tube 4 passes through the high-frequency heating tube 11 . Both the heat treatment box 1 and the cooling pipeline 2 are filled with a protective gas with a pressure of 0.4 MPa, and the protective gas is nitrogen. The washing box 3 is provided with a water inlet 31 and a water outlet 32, wherein the water inlet 31 and the water outlet 32 are sequentially arranged along the opposite direction of movement of the stainless steel pipe 4, the water inlet 31 is arranged at the bottom of the washing box 3, and the water outlet 32 is arranged on the top of...
Embodiment 2
[0036] The difference from Example 1 is that both the heat treatment box 1 and the cooling pipeline 2 are filled with nitrogen gas with a pressure of 0.65 MPa. The production process of bright stainless steel pipe includes unwinding, forming, welding and cutting, among which, the following steps are also included between welding and cutting:
[0037] 1) Heat treatment step: place the stainless steel tube 4 in a heat treatment box 1 filled with nitrogen, the air pressure in the heat treatment box 1 is 0.65MPa; make the temperature of the stainless steel tube 4 reach 1100°C, and the heat treatment time is 300 seconds;
[0038] 2) Cold treatment step: move the stainless steel tube 4 to the cooling pipeline 2 filled with nitrogen for natural cooling, the cold treatment time is 420 seconds, and the air pressure in the cooling pipeline 2 is 0.65MPa;
[0039] 3) Cleaning step: the stainless steel tube 4 is moved to the washing tank 3, and the stainless steel tube 4 is cleaned by the ...
Embodiment 3
[0041] The difference from Example 1 is that both the heat treatment box 1 and the cooling pipeline 2 are filled with nitrogen gas with a pressure of 0.5 MPa. The production process of bright stainless steel pipe includes unwinding, forming, welding and cutting, among which, the following steps are also included between welding and cutting:
[0042] 1) Heat treatment step: place the stainless steel tube 4 in a heat treatment box 1 filled with nitrogen, and the air pressure in the heat treatment box 1 is 0.5 MPa; make the temperature of the stainless steel tube 4 reach 1060° C., and the heat treatment time is 360 seconds;
[0043] 2) Cold treatment step: move the stainless steel tube to the cooling pipeline 2 filled with nitrogen for natural cooling, the cold treatment time is 360 seconds, and the air pressure in the cooling pipeline 2 is 0.5MPa;
[0044] 3) Cleaning step: the stainless steel tube 4 is moved to the washing tank 3, and the stainless steel tube 4 is cleaned by the ...
PUM
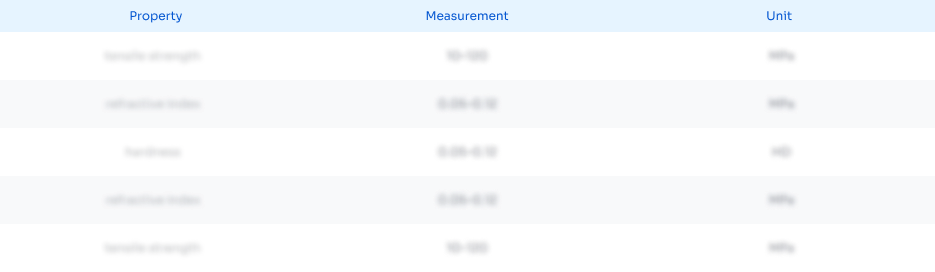
Abstract
Description
Claims
Application Information

- R&D
- Intellectual Property
- Life Sciences
- Materials
- Tech Scout
- Unparalleled Data Quality
- Higher Quality Content
- 60% Fewer Hallucinations
Browse by: Latest US Patents, China's latest patents, Technical Efficacy Thesaurus, Application Domain, Technology Topic, Popular Technical Reports.
© 2025 PatSnap. All rights reserved.Legal|Privacy policy|Modern Slavery Act Transparency Statement|Sitemap|About US| Contact US: help@patsnap.com